It is well worthwhile for a medical tubing manufacturer to establish the feasibility of producing a new form of tubing on a lab level before making the investment of time, energy, and money to crank out the product on full-scale equipment. Quirks, unanticipated variables, or miscalculations cost a lot less on a lab scale than they do on an extrusion line going full tilt. Startup and shutdown of a continuously operating extrusion line is a relatively unforgiving process.
Davis Standard LLC, Pawcatuck, Conn., has designed and installed a new laboratory line at its technical center, dedicated to enabling medical extrusion processors in their efforts to develop innovative medical tubing R&D concepts into production capabilities.
The line, installed earlier this year, is engineered for end-product development of small, tight-tolerance tubing typical of that used in medical applications. Situated in a dedicated, climate-controlled area, it offers a clean environment for trials. Medical product suppliers can test new resins, make samples for proof-of-concept, and conduct downstream R&D before making significant investments in their own processing equipment lines.
Wendell Whipple, vice president of Davis-Standard's Pipe, Profile and Tubing Group, says, "There continues to be significant growth and development in medical tubing applications."
He says the newly installed line gives Davis-Standard a way to contribute to the success of medical tubing extrusion processors by providing them with "a fully equipped option to develop new products."
"This is a new version of an existing technology that Davis-Standard acquired from the acquisition of Harrel," he said. "We moved the controls from a single board computer to the PLC world." There are no new lines in the field with this setup, but systems that Harrel supplied are in place in the upper Midwest and northern California.
Model MEDD (Medical Equipment Direct Drive), Davis-Standard's premier compact extruder, is optimized for clean environments with closed, ventilated and air-conditioned space. It features two interchangeable barrels, in 1-inch and three-quarter-inch 24:1 length-to-diameter sizes, to cover a range of development opportunities in medical tubing. The system has bump/taper, multi-lumen, and micro-bore tubing capabilities.
The replaceable feed section liner may be smooth, grooved, corrosion-resistant Inconel, or wear resistant. The system has an extensive screw inventory. Melt pumps with servo drives were designed by Harrel.
The line incorporates Davis-Standard's patented alternate polymer process, which allows two different durometer materials to run through one head, holding size, shape and dimensions with a very short transition yet providing a product that is soft on one end and more rigid on the other for medical catheter products. These products allow the surgeon to push and move the catheter while having a soft material inside the body.
The system can process common thermoplastics as well as some high-temperature plastics.
The EPIC-III programmable logic control monitors melt pressure and temperature transducer points inside each barrel heat zone, data that can also help optimize screw designs.
Zumbach Electronics Corp. supplied laser and ultrasonic gauging, including trim control and two gauging systems. Conair Group supplied desiccant drying capabilities of up to three resins simultaneously and downstream equipment.
The new lab line cost $600,000 to install and it replaced a co-extrusion microbore tubing line.
Space is available on the lab line for processor-supplied equipment such as a payoff or coiler. Contact Jason Baird at [email protected] or Bill Lee at [email protected].
Merle R. Snyder, senior correspondent
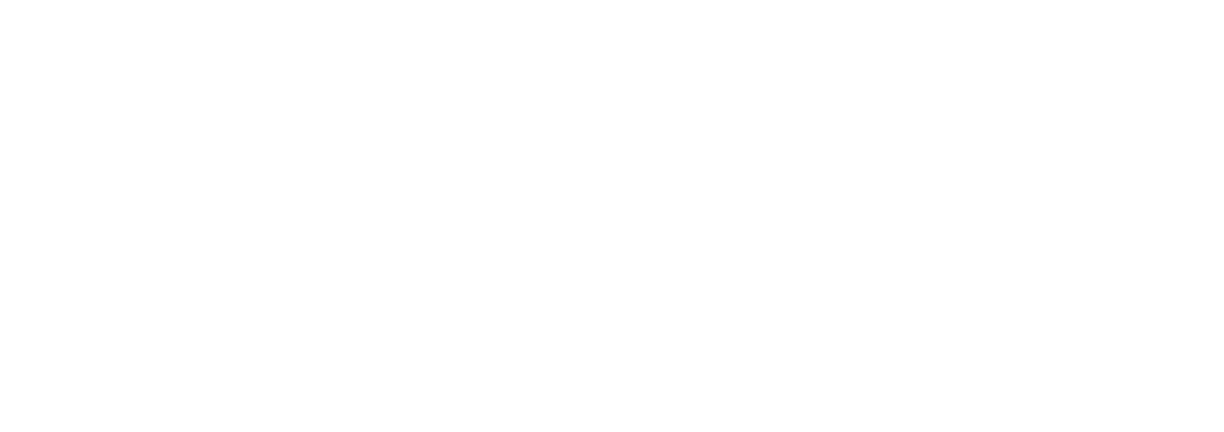