Companies push capabilities to remedy mold flow-imbalance issues
It is an age-old issue with potentially expensive consequences: short shots, flash or over-packing conditions from cavity to cavity or within a single cavity, leading to part warpage, loss of mechanical properties, weak weld-line strength and ultimately, scrap parts, industry sources say.
Several companies are evolving products and services to address flow imbalance in injection molds. New and novel developments are being made in manifold, runner or gating designs; mold-cavity sensor technology that captures pressure or temperature data to adjust hardware components upstream; rheological-based flow control; and a system of melt-flow control operated from the injection press itself.
The latest refinements and advances build upon the success of multilevel manifold systems or the adjustment of process parameters to counteract uneven melt flows. These approaches are increasingly targeting a wider cavitation range. Flow balancing is no longer limited to high-cavitation tooling, stack or family molds but can occur in low cavitation and even single-cavity tools with a single gate that handle large shot sizes, have complex internal geometries or use multiple materials or filled polymers. In fact, there is a growing need for single-cavity molds to be analyzed at the intra-cavity level, due to part quality problems directly related to shear issues, says David Hoffman, senior instructor and training development manager with Beaumont Technologies Inc., Erie, Pa.
"Problems in a single-cavity mold can be attributed to material property differences within a cross section of a part that results in filling pattern and melt-temperature variations, and this ultimately affects how the part is formed," says Hoffman. Beaumont has seen a "balanced" four-cavity mold produce parts similar in short shot weight yet two of the cavities yielded scrap parts continually due to differences in material properties found within the various flow groups in the mold.
"Balance has to go beyond basic balanced filling and should consider a balance of filling, packing, temperatures and pressures among them," Hoffman says.
Industry experts from firms such as hot runner supplier D-M-E Co., Madison Heights, Mich., and monitoring software maker RJG Inc., Traverse City, Mich., say a naturally balanced runner design cannot easily be characterized as good or bad during the design process because some materials are more susceptible to shear-induced flow imbalance than others. In many cases, a geometrically balanced runner system is less likely to create much shear imbalance if the resin itself is a low-stress material that does not shear much. A thick-walled part may minimize the significance of filling imbalance because it is easy to pack. Low-tolerance parts may meet specifications even with some imbalance in filling.
"A thin-walled high-cavity mold with high-pressure losses may see less than 5 percent imbalance while a thicker part that is easier to fill may make good parts with well over 10 percent imbalance," says Michael Groleau, project manager and co-owner of RJG.
NEW BALANCE
Geometrically balanced runner systems rely on consistent flow lengths and flow channel diameters to each cavity, as well as uniformly experienced pressures and temperatures throughout the mold, but Beaumont Technologies asserts that rheologically balanced runner systems, which address the relationship between melt viscosity, melt temperature and shear, represent the next generation of balanced melt-delivery systems.
"There is an assumption that the viscosity of the melt going into each cavity is the same but it is not, because a lot is happening to the material when it is pushed into the mold at today's higher molding speeds and high pressures," says Hoffman.
When melt travels through the runner, the melt near the mold wall is subject to shear thinning and shear heating, and the temperature can often rise more than 150 degrees Fahrenheit while the viscosity can be significantly lower compared with plastic moving in the center of the flow channel, says Hoffman. Due to the laminar flow conditions that exist, the layers of hotter, shear-thinned outer melt and cooler, more viscous inner melt do not mix.
When the layered melt continues to flow within a part or a runner system, it will impact the cavity fill pattern and material property balance.
Beaumont's MeltFlipper (single- and multi-axis systems) and line of fixed (SRC) or adjustable (iMARC) mold insert technologies are for the first time being applied to molds with four or fewer cavities.
"Installations of MeltFlipper, iMARC and SRC applications in cold runner molds with one, two or four cavities increased more than 20 percent in the past two years," says Hoffman. These technologies are placed into the melt stream of a runner system at strategic locations to mix or rotate the melt as a means of creating uniform shear and material property conditions to and within each cavity.
In addition to further optimizing the molding process and part quality attributes through rheological means and getting the word out that its technology is useful on low-cavity tools, Beaumont has developed an early version of Therma-flo Moldometer, said to be the first approach specifically designed to characterize the injection moldability of polymers. The patent-pending method, an alternative to melt flow index (MFI) and older rheometer methods that omit the thermal exchange between the melt and mold and the frozen layer, has been enhanced since 2012, says Hoffman.
Thermo-flo is currently a service that Beaumont provides but it will consider selling complete turnkey systems in the future.
Therma-flo evaluates a plastic's flow under a wide range of process conditions and part geometries to better reveal the thermal exchange between the melt and the mold. Tests conducted on a given material evaluate the influence of mold geometry, injection rate and temperature, providing a clear map of how a given material will react under different velocities and part thicknesses.
"For example, you can find that two 10 MFI PBT materials will flow dramatically differently from one another as the velocity and part thicknesses are changed," says Hoffman.
CAVITY SEARCH
RJG's eDART is attached to a machine to measure screw position, injection pressure and machine sequencing signals. Cavity pressure monitoring is the most common implementation of the eDART system and reveals how the pressure develops as filling is completed and packing begins. The sensor is placed at the end of fill and provides detailed diagnosis of filling or imbalance problems in the mold.
RJG currently is developing a new multichannel cavity-pressure system that allows injection molders to connect up to eight strain-gauge sensors to one connection point on the mold, simplifying in-mold installation. For use with eDART, the interface reduces the per-mold cost by up to 26 percent compared to a piezoelectric option, up to 40 percent over a single-channel strain-gauge sensor and up to 55 percent over an embedded sensor plate.
Priamus System Technologies LLC, Brunswick, Ohio, launched Priamus FillControl, its automatic hot runner balancing system, several years ago with version 1.0 and offers version 1.9 today. That new system replaces the Priamus Fill system the company stopped selling last December. Priamus FillControl uses a cavity-temperature sensor at the end of fill to detect the melt temperature then overwrites the nozzle tip temperatures using a proprietary algorithm to achieve equal mold filling. Priamus prefers the use of a temperature-cavity sensor to a pressure sensor, says Marcel Fenner, technical manager.
"The melt front is much clearer to detect as there is a very specific spike when the melt reaches the temperature sensor; the melt either reaches the sensor or it does not. With pressure sensing you always need to have a certain amount of pressure to measure. In addition, the temperature sensor is half the price and is more responsive," says Fenner. The temperature signal can also be used to trigger switchover to holding pressure, which brings higher process consistency. Priamus FillControl is offered in an H version for hot runners, a V version for LSR (cold runner molding) and an M version for machine control.
Priamus FillControl was launched with new built-in screen shot functions and setup wizards for enhanced user-friendliness, as well as program enhancements that allow the user to review data from previous cycles. Generic trends for every function (monitoring, viscosity, control) can be derived from the system and a touch screen with larger icons eases data entry and navigation. FillControl can also be used with pressure cavity sensors that the company offers. The system is compatible with more than 20 hot runner temperature controllers and is scalable for use with molds up to 128 cavities. The control technology is being developed for use with powder metal injection molding and ceramic molding, says Fenner.
Late last year, Priamus discontinued sales in the U.S. of its Pass Controller system, designed to record cavity pressure and temperature to determine melt viscosity in real time for each molding cycle. This capability is included in the FillControl system.
HONE THE HOT RUNNER
Hot runner supplier Mold-Masters, Georgetown, Ontario, improved the performance of its iFlow two-piece brazed plate manifold technology, which is designed as a proven alternative to manifolds with gun-drilled or pressed-in intersections. Melt flow channels are formed with one half of the channel machined into one half of the mold block and the other half of the channel machined in the other mold block half. The two pieces of mold steel are joined through a vacuum brazing process in a design that eliminates dead spots or steel variations, says Ken Jacob, master solutions engineer at Mold-Masters.
Mold-Masters keeps cavity side tool dimensions and sizes tight (within net 1 percent) to minimize the creation of a steel imbalance.
"We split the plate of steel so we can machine it exactly to the flow channel dimensions we desire, and we also incorporate level changes in the melt channel we are forming to balance the flow," Jacob says.
Mold-Masters' iFlow manifold design was enhanced several years ago to operate at maximum pressure rating of 30,000 psi (2000 bar) compared to 20,000 psi previously. Jacob says the upgraded performance of the manifold allows the technology to reach into new markets. Its brazed plate technology is being used in single-cavity molds and stack molds, as well as multi-cavity tools with 96, 128 and 144 cavities.
Mold-Masters also enhanced the robustness of its one-year old Melt-Cube direct side edge gating system for better cavity-to-cavity balance. Easy flowing (MFI=130 grams/10 minutes) materials can be handled at higher pressures (1900-bar hold pressure/ 2000-bar peak pressure) and higher processing temperatures (608 degrees Fahrenheit vs. 536 degrees Fahrenheit). The updated design, for simultaneous gating of 2 to 16 cavities, has a 20 percent higher pitch density over competing circular side gating systems. A dedicated temperature control zone at the gate and minimized gate to parting line distance provides optimal thermal conditioning and excellent vestige control.
The acquisition of Mold-Masters in 2013 by Milacron LLC has prompted Milacron's D-M-E unit, which supplies mold bases and related components to scale back or tailor its technologies to molds with 24 or fewer cavities, says Craig Kovacic, manager of hot runner systems at D-M-E. The company dropped its valve gate line in favor of the valve gate products from Mold-Masters, but it continues to offer a hot tip nozzle.
D-M-E provides primarily gun-drilled tooling, a proven approach as long as heating control is precise.
"Five years ago we went back to employing 8.5mm flexible heaters that better follow the contour of the mold vs. a tubular design, which allows us to incorporate more heat zones and achieve a more uniform heating profile in the manifold," says Kovacic.
Ewikon Molding Technologies Inc., Rockford, Ill., employs mechanical and temperature balancing of the manifold to minimize flow imbalances. Where the melt reaches a change in direction — whether it is a level change, channel split or divider — Ewikon installs its flow element technology that is a section of the melt channel itself that enhances melt flow while eliminating any chance for dead spots or hang-up points. The technology, available since 2008, is being realized for the first time with manifolds up to 96 drops.
The flow element is made in two halves that are vacuum brazed together. An optimum flow channel design can be manufactured into the element, says David Boxall, president of Ewikon Molding Technologies. After brazing, the element is turned into a round plug that is oversized to the bore. A guided heat shrink approach installs the element into the manifold and seals the system for 3000-bar melt pressure.
Ewikon has produced what it calls micro manifolds for years for the Babyplast line of molding machines. For the past three years it began offering a concept where several of the micro manifold systems are put into a single mold, all fed by a single bridge manifold.
"Each micro manifold, installed into the mold base, essentially becomes a single zone of temperature control, for an improved heating profile," says Boxall. During the past three years, Ewikon built and installed several micro manifold systems for use in direct-gated 192-cavity toolmaking parts weighing 0.8 gram.
BALANCE FROM THE PRESS
Sumitomo Demag Plastics Machinery, Strongsville, Ohio, attacks flow imbalances with its zero-defect Z-Molding system concept that optimizes machine setup, injection and clamping functions to pare down part defects, especially with difficult-to-mold or multi-cavity tools, says Tony Marchelletta, Midwest regional manager.
Initially offered in 2009 on a limited basis with Sumitomo's SE line of all-electric servo presses, the zero-defect (Z-Molding) approach is part of 95 percent of machines sold in the U.S. to date. Z-Molding is comprised of several patent pending technologies that allow part molding with reduced stress and enhanced part properties. This includes the Flow Front Control (FFC) system that controls/restricts screw motion and positioning to optimize the flow front, preventing overfilling or short shots; and Minimum Clamping Molding (MCM) software, which detects the minimum point at which the mold halves are completely parallel and defines the threshold where flash-free molding can occur. This is the optimum point at which the best cavity venting exists, says Marchelletta.
The unit also features Sumitomo's Intelligent Servo Control (ISC), which uses sensors to look at clamp tonnage during the cooling stage to determine if a cavity will flash or short shot. Since Sumitomo produces its own servomotors and drives it can see and adjust to minute variations in clamping tonnage, says Marchelletta. ISC delivers up to 25 percent faster response.
Sumitomo has zero-defect molding in the production of electrical bobbins in eight cavities on its 84-ton SE75EV all-electric press at the Plastec West/MD&M West show last year in Anaheim. The machine's Flash Speed Mode delivered fast response control of velocity and pressure before and after velocity/pressure switchover for precise injection and control of shot size, which was 137 grams (4.8 ounces).
Sumitomo also developed a new single layer (SL) screw and injection unit concept in collaboration with a Hong Kong-based customer designed to keep shear to a minimum, which is a benefit for temperature-sensitive materials. A mold builder and material supplier's collaboration focused on minimizing the chance for flow imbalances. The SL concept was introduced two years ago at NPE and is beginning to gain traction, the company says.
Mikell Knights, senior correspondent
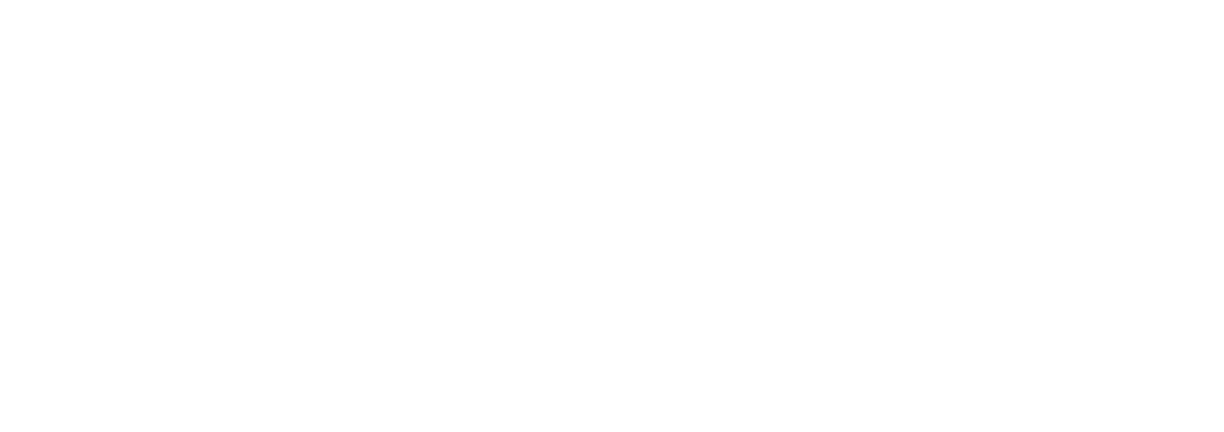