When asking industry officials what the next evolution might be for LSR, the responses varied and offered insight into technological improvements from different parts of the supply chain.
At Arburg, officials are continuing to see the industry evolve from single-material molding to two material molding. Applications benefiting from the functionality of LSR combined with thermoplastic, or another grade of LSR, continue to grow. However, LSR does not naturally adhere to all substrate materials and this can sometimes present an engineering challenge in marrying the material combinations. This is often overcome through mechanical interlocks or surface treatment of the substrate.
M.R. Mold & Engineering Corp. of Brea, Calif., has been building LSR molds for more than 28 years. Officials said there are many technologies that the industry can be focused on to help LSR evolve, for example, developing zero deflection platens and continuing to perfect shot size control. There also is a need for pressure transducers that can read single-digit psi. Where traditional transducers read 30,000 psi, silicone requires 10 psi. Material manufacturers can help the evolution by developing a purge compound for silicone so that material isn't wasted and develop materials that are consistent batch to batch and do not fowl or contaminate the mold. Feed mechanisms on machines also need to be easier to clean.
Geri Anderson, marketing director with M.R., said that it has been estimated that the LSR market is growing by 15 percent annually within the industry, both in dollar terms and in demand for molds, material and equipment being purchased.
"We have seen engineers attempting to get a single part to perform numerous functions in recent years in order to decrease the number of parts in an assembly," Anderson said. "This function has brought design and manufacturability challenges in building a mold. How to get the product to stay on the right side of the mold and devising a way to demold continues to evolve and brings out the creativity of those who know and understand silicone. Automation and flashless parts continue to be technological evolutions."
For one of the main markets in which silicone is used, medical devices continue to get smaller and smaller. This makes silicone components smaller and smaller (micro), said Anderson, and automation for micromolding an ever-increasing challenge.
The resin is acknowledged as high performance, having property characteristics for use in aggressive environments, according to officials with MGS Mfg. Group. LSR injection molding requires specialized tooling (injection molds); runnerless gate techniques (cold deck); machinery with specific injector technology, and it requires unique set up and process engineering.
LSR resins process much more differently than thermoplastics and require strict resin-handling disciplines in order to be successful, said officials with MGS.
"LSR injection molding requires a dedicated business strategy; simply switching or adding LSR as another resin is typically not a good success plan," said John Berg, director of marketing at MGS. Many molders, specifically custom molders, process a wide variety of different thermoplastic resin grades but typically do not mold LSR in the same facility or at the same time within the same machine cell. Once there are more customer molders that expand their operations and dedicate
personnel, equipment and facilities to add LSR processing, OEMs and brand owners will have greater opportunities for new product development and launch.
"For the adept molder who can recognize and differentiate process requirements of thermoplastic and thermoset LSR resins within the same machine cell, an exciting business adventure awaits development," Berg said.
For others in the industry, continued advanced automation will be the focus.
"We see a trend of offshore molding diminishing and customers looking to mold in North America with automation," said Greg Roembke, president of mold maker Roembke Mfg. & Design Inc. of Ossian, Ind. Also, over the past several years his firm has witnessed the growth of "true" two-shot molding in the United States. Roembke identifies "true" two-shot as using one machine to inject two different materials. This is different than insert molding or over-molding.
"This may be a thermoset onto a thermoplastic or a thermoset onto a thermoset," Roembke said of two-shot molding. "We have completed many two-shot project already and many more are being currently discussed."
Angie DeRosa, managing editor
Related article: LSR in motion: More machinery firms tapping liquid silicone rubber niche
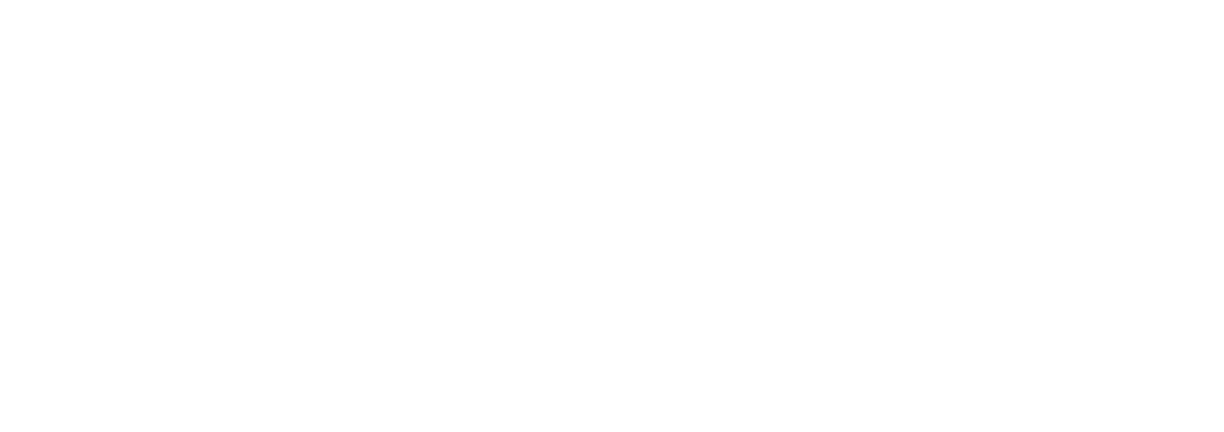