Injection molding of liquid silicone rubber is on a growth trajectory. But the thermoset has finicky characteristics that make the molding of it tricky and that requires a mindset change for those accustomed to molding thermoplastics. Machinery and mold makers are beefing up their efforts to address this niche material and the benefits it brings to products.
Especially in the medical device market, LSR is finding a home because of unique characteristics including its biocompatibility, stability and bacterial resistance. It is also hypoallergenic and high performing. Traditional thermoplastic elastomers customer products, such as fitness bands, tend to be sticky and will pull hair on an arm. LSR, however, is not sticky. In product design and processing, complex geometries can be achieved along with undercuts not possible with thermoplastics.
LSR processing has been on display this year at various trade shows, including Fakuma, where Engel displayed its e-victory 200H/80W/120 combi injection molding machine that was automated with an Engel viper 20 linear robot. The machine was processing sensor housings with integrated seals. At Taipei Plas 2014, Arburg showcased waste-free production of LSR via its hydraulic Allrounder 370 S with a clamping force of 700 kilonewtons (71 metric tons) and a size 290 injection unit. The mold was supplied by Rico Elastomere Projecting GmbH with an open cold runner system. It manufactured at a cycle time of 50 seconds per four bottle openers. Reinhardt Technik GmbH supplied the LSR dosing unit and parts were demolded through compressed air.
Beyond the machinery-focused trade shows, though, LSR processing has been on display at events like Lightfair International, an architectural and commercial lighting trade show, where Sur-Seal Corp. of Cincinnati was molding an optical-grade silicone. A.L.P. Lighting Components Inc. of Niles, Ill., also showed examples of optical-grade silicone.
That is the newest market for LSR, said Steve Broadbent, Engel Machinery Inc.'s project engineer for LSR and elastomers processing machinery. Other markets will continue to dominate, however.
"The biggest growth, based on market, is medical," he said. "It still is not the same volume as in automotive, but it is where the growth is. Automotive is high volume, but it is a mature market."
The material generally requires a higher temperature range for operating and has a much better compression set. However, silicone in general is not compatible with petroleum; therefore, it is mostly used in electrical components for automotive.
Think of the Chevy Volt as a perfect example.
"Thirty new parts that were all silicone launched just because of that vehicle," said Broadbent.
Engel also is seeing growth in consumer goods. On the processor side, the growth in consumer and medical markets is causing expansion at Dymotek Corp. of Ellington, Conn., which specializes in thermoplastics injection molding, silicone molding and plastics engineering. Officials there are adding a second facility sized at 48,000 square feet. That's 13,000 square feet larger than its original facility.
"We have long-term business plans that within five years that will be full," said Victor Morando, vice president of engineering services for Dymotek. There is a large medical project that will launch in the facility in 2015. It currently houses six presses with more to come next year.
Dymotek uses robotics where needed. One of its cells operates with two Arburg 200-ton presses making four parts that get kitted up in a commercial product. That cell operates with the help of two ABB robots and a cooling conveyor.
LSR molding always is tied to an assembly. Dymotek purchased three more LSR 220-ton two-shot presses from Arburg this year. It now has six LSR two-shot presses.
In terms of the market growth potential, Morando said, "We are not even scratching the surface yet."
The design flexibility, in part, gives the material its allure. There was a two-shot application that had a 2mm wall section and a 0.2mm wall section.
"You would look at it in a thermoplastic application and you would never attempt it," Morando said of the undercut in that particular part. "The problem with it on the thermoplastic side is, could you get that thin area to fill out? Would that area distort or tear?"
LSR is a paradigm-shifting material, one where engineers used to dealing with thermoplastics or other thermosets have to be trained to accept the differences and to design for the material.
"Unless you really have that in an engineer's mind, they don't design for it," said Morando. "To get it out of the niche, you need to have more information available."
Dymotek has done a number of presentations for customers in-house. At MGS Manufacturing Group in Germantown, Wis., two-day training is available for customers who purchase its portable LSR injector unit.
In LSR, a two-component material, there is a cross-linking of parts A and B that takes place in the mold, explained Mark Voelkner, who heads up business development for MGS' Universal Multishot Systems equipment. The mold accelerates cross-linking typically heated above 300 degrees Fahrenheit. Some processors will require a lower temperature.
"LSR is inherently compressible and that creates some nuances in the process that thermoplastic elastomers or thermoplastic resins do not have," said Voelkner. "There is variation in an LSR process due to the compressibility. It's like you have to compress it to make it move. Likewise, on the recovery stage, you have to also understand your shot volume. We believe our machine controls that to a very high degree. Shot-to-shot consistency with our machine is something that we can maintain. We recognize that as a key to design."
MGS built its first machine of this design in 2005. The Universal Shot Systems model E-30cc PH plunger horizontal servo LSR injector unit is portable and typically has been installed on multishot presses.
"The requirements in our industry are always changing," said Voelkner. "What we've created is a portable injection unit for LSR that can be integrated with a molder's thermoplastic molding machine or silicone."
The system mechanically interfaces on the non-operating side of the molding machine and electrically through the robot interface. The first unit sold by MGS was integrated into a 500-ton molding machine. The company offers a horizontal floor mount that officials say works well with molding machines from 150-300 tons. Depending on shot size and mold size characteristics, units also can be made as a mold mount model where they are bolted directly on the injection mold.
Demand for this portable unit has taken off over the past two years.
"The first five years we had hardly any growth, just very few machines," Voelkner said. "Within the last two years real growth has been recognized."
Geographically, Engel's Broadbent said that Wisconsin and Missouri have seen the largest growth along with the U.S./Mexico border region to include Nogales and Tijuana. Those regions are significant for medical molding. Another trend is that OEM suppliers are bringing LSR in-house as a capability rather than contracting out their work. Companies that have done this include B. Braun Medical Inc., based in Bethlehem, Pa., and Baxter International Inc. of Deerfield, Ill.
Worldwide, Europe does a lot of developments in LSR, also for multi-component molding. Mexico is at the beginning with LSR technology and will be a significant market for the automotive industry in the next few years.
"They will follow U.S. trends very closely," predicted Broadbent.
Most of the growth will be for high-end producers in the United States, Europe and Mexico and now the material is coming up more and more in China for high-tech production for each kind of application and industry. China also is moving faster and faster for medical parts for LSR.
In terms of the learning curve required for processing LSR, Broadbent maintains that a company should hire people that are experienced in LSR or hire someone with no experience at all.
"Do not try to convert plastics people into silicone," he said. "As a molder, you are almost better off hiring a new engineer with no experience."
Elmet Elastomere of Oftering, Austria, supplies injection molds, pumping equipment, cold decks, peripheral devices. At Elmet North America in Lansing, Mich., officials focus on hands-on intensive training through a four-day liquid injection molding class that only is offered at Elmet's tech center in Lansing. Participants are tasked with building an LIM cell from scratch and then practicing process troubleshooting and learning process shutdown and proper maintenance. That training incorporates Elmet's technologies such as LSR cold runner tooling and dosing systems with machine technology from Engel and Arburg.
Elmet itself has experienced double-digit sales growth since establishing its North American operation in 2012, said Daniel Schölmberger, technical sales and marketing manager. The company produces all of its molds in Austria.
"In plastics molding everything is pretty much black and white," he said. "With silicone, it's real different. It is not as either/or as it is with thermoplastics. The process itself is much more delicate which requires specially trained technicians."
Demolding with thermoplastics, for example, is performed with ejector pins in 98 percent of cases. With LSR, use of ejector pins is not common and if the pins are used, it requires engineering them differently. Also, hot runner systems are used in thermoplastics versus cold deck systems in LSR.
"You want to cool everything before the cavity to avoid curing," Schölmberger said.
Angie DeRosa, managing editor
Read related article: Where LSR might be headed
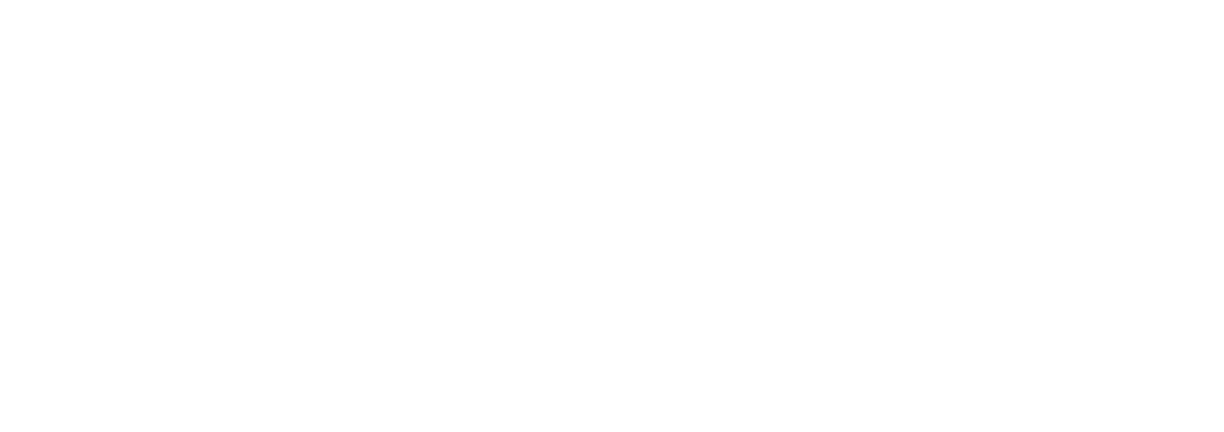