
By Bruce Geiselman
Sinterit, based in Kraków, Poland, recently introduced its Nils 480, a new selective laser sintering (SLS) 3D printer designed for manufacturers looking to print more production parts quickly.
Nils 480 marks the launch of an industrial line of printers, and it is an addition to Sinterit’s existing compact line of printers that features the Lisa X, Lisa Pro and Lisa. The Nils 480 answers different needs, according to the company. The compact printers may be best for advanced smaller print volumes associated with R&D and educational uses, while the Nils 480 would be best suited for printing larger volumes of parts, bigger parts and end-use parts, the company said.
“What’s different about Nils 480 from other Sinterit products?” asked Tim Sheehan, VP of Sinterit’s sales and marketing in the U.S. “First of all, it’s 10 times faster and larger. It has been created to help support industrial printing with selective laser sintering, whereas the Lisa products are compact. They fit very well in an office environment or in a small lab. A Nils would find itself on a factory floor making parts.”
High capacity for material
Another factor that differentiates the Nils 480 is that it can store 70 pounds of material and continuously print.
“This means that it can run for roughly a month before you need to add powder and reset your operation,” Sheehan said. “It really takes you from prototype building to production building of parts.”
Once a build is complete, the printed material is auto dispensed to a cooling chamber, and once the material cools, an operator can remove the print and move it to a powder-handling station where the part is cleaned and excess material is removed and vacuumed away for reuse.
“Our system vacuums off the excess powder, runs it through a cyclone separator, which separates chunks from powder and then takes it and runs it through a sieve,” Sheehan said. “Then we recapture it.”
The efficient and immediate recapture and reuse of the polymer powder reduces waste and costs, Sheehan said. The ability to operate uninterrupted for weeks at a time increases operational efficiency and reduces costs, he added.
The Nils 480 features a large printing volume, fast build time and automated systems for bulk additive manufacturing users, the company said. Sinterit officials claim the return on investment (ROI) of the Nils 480 can be achieved in just 40 days, making it an attractive option for additive manufacturing newbies.
The Nils 480 is selling for $59,900, or $72,900 for the Nils 480 industrial set, which includes a printer and a powder-handling station, Sheehan said. Normally, customers would purchase the industrial set.
Larger print bed
The size of the print bed is 7.9 inches by 7.9 inches by 13 inches high. The printer has build speeds of 10mm to 14mm per hour and full-bed printing in 30 hours. However, most printing jobs will be completed within 24 hours, according to the company. A Galvo scanner system, which uses mirrors to direct the laser beam instead of physically moving the laser unit itself, is the key element responsible for the speed.
The printer works with a range of materials. Sinterit currently offers nine different powders suitable for nearly all applications, and more powders will be introduced in the future. The available materials include polyamide (PA) 12, PA 11, PA 11 with carbon fiber, PP and TPE. Third-party materials also can be used.
An automated powder-distribution system is designed to limit waste while providing a large printing area, the company said.
A Nils 480 printer can be installed in half a day, and it requires only electric power and compressed air. The printer also comes with Sinterit Studio 3D printing software designed for auto-nesting, slicing and modifying printing profiles. The printer can be purchased as a stand-alone product or with post-production equipment for cleaning and sandblasting printed parts. The downtime between refills is only 15 minutes.
Bruce Geiselman, senior staff reporter
Contact:
Sinterit USA, Boston, 978-302-6153, www.sinterit.com
Bruce Geiselman
Senior Staff Reporter Bruce Geiselman covers extrusion, blow molding, additive manufacturing, automation and end markets including automotive and packaging. He also writes features, including In Other Words and Problem Solved, for Plastics Machinery & Manufacturing, Plastics Recycling and The Journal of Blow Molding. He has extensive experience in daily and magazine journalism.
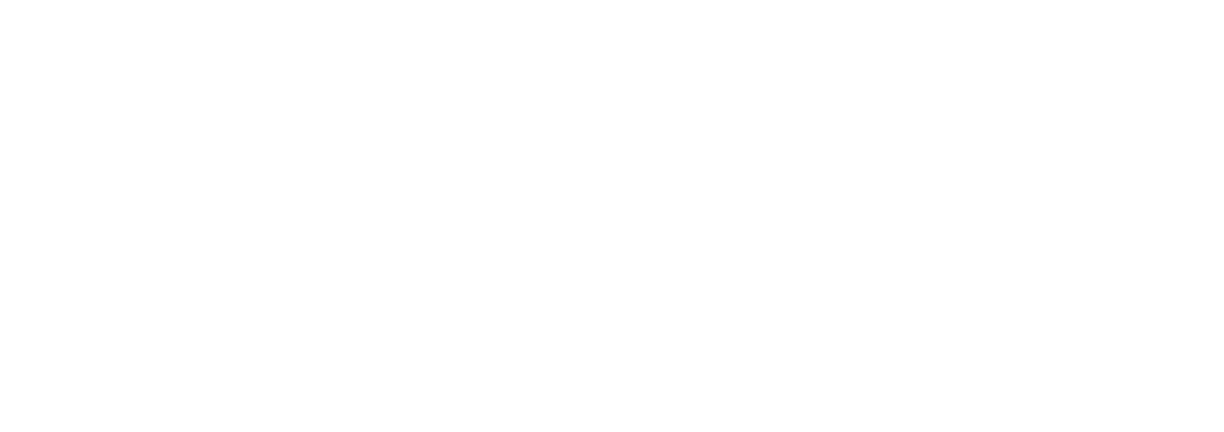