When Rod Groleau started his career in the 1960s, molding machines were not very sophisticated — they leaked, broke down and were not very safe. Controls generally consisted of two knobs.
The time was ripe for a college kid willing to dissect and study the process, then devote his working life to improving it — first addressing process monitoring techniques and eventually developing better molding procedures and training thousands of molders on how to apply them.
Some of his credits: the first modern process control system, first commercial mold pressure sensor and a complete line of specialized controls and information systems for injection molders. Many of the things injection molders do today to create better parts can be traced back to Groleau.
He recently answered questions for Plastics Machinery Magazine.
When you first became interested in injection molding, what was the process like?
GROLEAU: We were basically squeezing plastics into a hole in somewhat of a controlled crash. We used hydraulic pressure to squeeze the plastic in and we called it traditional molding. There was a control on the machine for speed but it was just a knob that you turned and it really didn't control speed. When you asked a molder "What do you do when you want to speed up?" he would say "That depends." They couldn't write down how they used these two controls.
What did you decide to do about it?
GROLEAU: I started thinking about how we could fill the mold in a way that was separate from packing it. The problem was if you used pressure to squeeze plastic in, you were not controlling speed. And if you use speed, you have to have an abundance of pressure; and if you run into the end of the cavity, you have a real catastrophe. So the first step was to separate filling from packing the mold — to decouple it. That was the beginning of Decoupled Molding. Later that two-stage process, called Decouple II, was expanded to Decouple III — fill, pack and then hold the plastic in the mold. Thinking about it in this way allowed a velocity control for fill and gives you the capacity to move plastic independently of its viscosity.
How did you and Don Paulson start Control Process Inc.?
GROLEAU: Don was my thesis adviser at the General Motors Institute [Kettering University] and I had to use his lab for my statistical experiments. We got to know each other pretty well but I went off to grad school at Michigan State and he left to become director of research at New Britain Machine Co. His plan was to develop a cavity pressure controller but he needed to do it quickly for the 1968 plastics show. So he got hold of me and that's when I started building stuff in my apartment, in married student housing.
Did you get it built in time?
GROLEAU: Yes, and it worked, but we didn't want anyone to open the panel! We were at the plastics show and went out to dinner with one of Don's very good friends from the Navy
and from Yale. We mapped out a business idea on a napkin for a cavity pressure controller and this guy said he could raise $100,000 seed capital before breakfast. So at 1 a.m. Chicago time he started calling friends on the East Coast and he raised the money we used to start Control Process Inc.
Once you started thinking about molding as a decoupled process, was there an "ah-ha" moment or did you move forward through a lot of trial and error?
GROLEAU: When we first started Control Process, we were tightly affiliated with New Britain Machine Co. They sold a lot of injection molding machines in the early 1970s to the company that is now Nypro. That company ordered machines that were quite different. The filling of the mold was done with system pressure. It was not adjustable, so the pressure was always wide open and there was a limit switch to turn off the pressure. They wanted to fill the mold as fast as they could possibly push the plastic and to make sure they did not run into the end of the cavity. I started thinking about that process and it was my first inkling about a different approach to getting the mold full. I realized that we were limited by how much pressure we could use to pack the mold.
What sort of development work were the machinery makers doing at that time?
GROLEAU: They were selling a lot of machines and molders were ordering bigger machines. It was a growth period. They were focused on developing mechanical parts but not the hydraulics. All the machinery makers were pretty much using the same pumps and solenoids and valves and relays. All the power controls were mostly standard from one machinery maker to the next.
As you were developing process monitoring products at Control Process, who were your customers?
GROLEAU: Initially we signed a contract with New Britain Machine but they allowed us to keep selling things to others. Eventually we were selling more directly to other customers than we were to New Britain, so we ended that agreement and went our own way.
At what point did we enter the modern era of injection molding?
GROLEAU: It was when we realized we needed machines that could control velocity of fill independently of resistance to the plastic. We had to have hydraulic systems that were non-load sensitive. I developed a load sensitivity test. The first iteration was to inject into a mold with the resistance of the flow channels, and then, while on cycle, inject into the air. The air shot has little resistance. If the machine is not load sensitive, the fill times into the mold and into the air will be the same. Once machine builders understood why we were interested in this test as a measure of
machine capability, they worked hard to improve hydraulics circuits and to make their machines non-load sensitive. We now use instrumentation to do the test.
Describe the various iterations of the DART system.
GROLEAU: We introduced DART (Data Acquisition and Retrieval with Transducers) in 1991. It allowed you to collect and replay data but was on a single machine basis. There was no way to do multiple machines. So with DARTNet we put a sentry box on each machine and collected the data in a central computer, but it still needed a lot of tweaking and setup on the machine. DartVision in 1996 was the first Windows-based product and eDART in 2000 was the industry's first digital data acquisition platform with smart sensor technology. With the DART systems, molders for the first time had the ability to save data from every cycle. So if you have been running an 8-second cycle on a 16-cavity mold for 10 years and someone sends back a defective part and you know the date and time it was made, the archived data becomes a powerful tool that lets you see how that part was made. Think about the value of that for air bag sensors, or baby seats, or medical products.
In 1999 your training and consulting business was merged with your equipment company and the new Master Molder Certification program became more important. How many people have you trained as Master Molder I, Master Molder II or through your Train the Trainer program?
GROLEAU: More than 2,000. These are our "process missionaries." They have all been through the same program and every one of them can step in and do exactly the same job.
Today, what constitutes state-of-the-art process monitoring equipment?
GROLEAU: State-of-the-art involves making systems robust in terms of reliability, easy to install for the mold builder and generating valuable information at the machine and wherever a molder needs it. It should also include ease of communication with experts off-site. Our Call RJG chat button, which was integrated into eDART two years ago, gives floor users ready access to resolve problems beyond their capability.
What mistakes do you see molders making over and over?
GROLEAU: The biggest mistake is to not take the time to make a robust molding process before it goes into production. We are really addressing this now with a few special customers and having great success. We start with the design and simulation, then build the mold. Essentially, you start with a process that was developed on the simulator where you can actually predict how you are going to mold something, then develop a process that does not change. If the process does not make parts correctly, you find out what varied then you put it back to where it should be. Few people have the diligence and build enough time and money into their schedule to do it, so they pay by the shot for the whole life of the program. That's the biggest mistake I see. Companies that develop a robust process upfront don't have to invest in troubleshooting. They just figure out what has changed and put it back. It can actually save time and money if done correctly.
If you could solve one problem for injection molders, what would it be?
GROLEAU: To have molders and brand owners work to develop truly robust processes during the development phase, so that molds could be started and run repeatedly with few problems and easy, predictable startups. So that the only time unusable parts are made is during startups and when something is broken in the process. That means no tweaking necessary over time … ever! Many molders have never seen truly capable processes, so they have a hard time visualizing the ideal state where almost no rejects are ever made and all of them can easily be segregated or contained with straightforward process monitoring. Companies that do this correctly reap huge rewards and try not to give their "secret techniques" away.
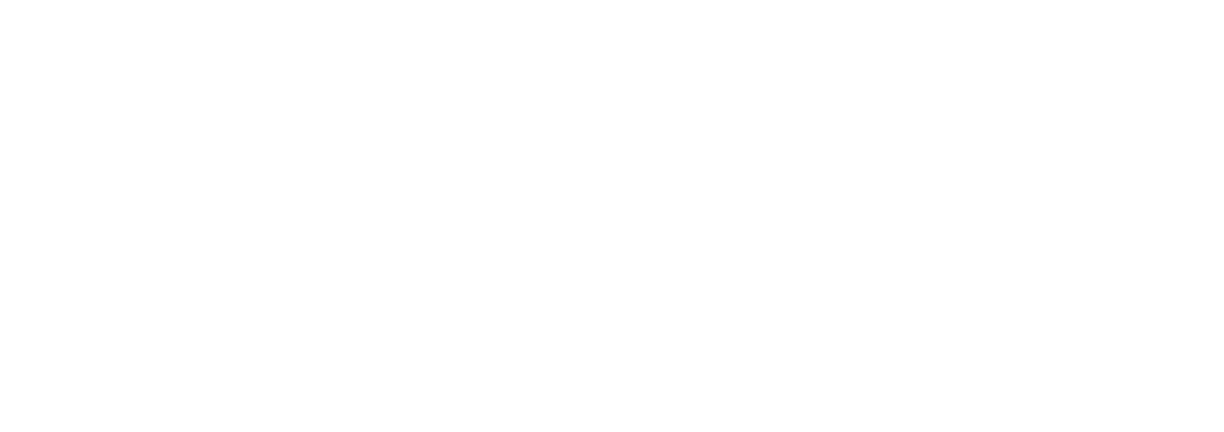