By Bruce Geiselman
When people imagine exhibitors at a thermoforming trade show, they might not think of 3D printer manufacturers, but 3D Systems recently demonstrated molds that its printers have produced for thermoforming clients.
3D Systems recently announced that Canadian thermoforming company Icon Technologies Ltd., of Winkler, Manitoba, purchased an EXT 1270 Titan Pellet 3D printer for producing large thermoforming molds with dramatically increased speed and significantly lower costs.
At its booth at the SPE Thermoforming Conference 2023 in Cleveland in October, 3D Systems displayed 3D printed thermoforming molds for a recreational vehicle fender skirt (printed with glass-fiber polycarbonate) and a marine dashboard (printed with carbon-fiber polycarbonate). In addition to displaying the molds, 3D Systems showed off the thermoformed parts. 3D Systems 3D printed these initial molds on the Titan printer for Icon Technologies, who then formed the parts from these molds.
Large-format pellet-extrusion additive manufacturing (AM) uses readily available thermoplastic pellets common to other plastics manufacturing processes like injection molding, and the pellets cost as little as one-tenth the price of traditional FDM filaments, according to 3D Systems.
The fender skirt mold took 15 hours to print and cost about $84 in material, according to 3D Systems. Printing the marine dashboard thermoforming mold took 120 hours with a material cost of about $445.
Thermoformers have a choice of materials that 3D Systems has found effective for mold production. One is a carbon-fiber ABS, another is a glass-filled polycarbonate, a third is a carbon-filled polycarbonate, and there is a high-temperature special blend nylon material for higher-temperature applications.
Composite materials are proven solutions for heavy-gauge sheet forming, with molds reported to have endured well over 1,000 shots with little to no apparent wear, according to 3D Systems.
EXT Titan Pellet 3D printers can help reduce raw material costs by up to 88 percent and cut mold production lead times by up to 65 percent compared to traditional methods, according to 3D Systems.
Traditional thermoforming mold production materials and methods involve wood, aluminum or ceramic molds, but John Loewen, founder and CEO of Icon Technologies, said 3D printing molds offers significant advantages.
“Traditional methods typically have a longer lead time,” Loewen told Plastics Machinery & Manufacturing on the show floor. “They’re typically performed by an outside party. Lead times are extremely important to us and to our customers, especially these days. Everybody wants product. R&D times are shortening. So, to bring this in house, where we are able to design and print a tool virtually over a weekend, this is preferred.”
Icon Technologies selected Titan printers for its needs after visiting its Colorado Springs, Colo., facilities, to see where the printers are made. 3D Systems also printed thermoforming tools for Icon in different materials.
Many of the products Icon Technologies produces are for the recreational vehicle market, which has been booming.
“They do a lot of work in the RV industry as well as other industries,” Brad Mount, global director of business development for Titan, 3D Systems, told PMM at the show. “During COVID, the RV market [demand] shot up. That’s really a very great part of their business, and with that, there were pressures to be able to produce thermoformed parts quicker and less expensively and competitively. It’s always an advantage.”
Icon Technologies is still evaluating the full impact of adopting 3D printing for producing some of their molds but is encouraged by what company officials have seen so far.
“They haven’t fully proven this yet, but with initial tools printed with the Titan and resulting formed parts, they believe they will achieve anywhere from a 50 to 70 percent cost savings and a lead time reduction of 60 to 70 percent in their tool production,” Mount said.
Icon Technologies is the second thermoformer to recently begin using 3D Systems Titan printing technology to produce thermoforming molds. Duo Form, an Edwardsburg, Mich., thermoforming company, also is using Titan technology for some of its molds, the companies announced earlier this year. Duo Form molds also were on display at the 3D Systems trade booth in Cleveland.
Thermoformers adopting 3D printing technology for mold production is a trend that Mount expects will continue growing.
“This is what we refer to as a killer application for us and for thermoforming customers,” Mount said. “They’re used to using traditional tooling methods for quite some time now. But a lot of them are learning about using 3D printing in the process to improve lead times, for much faster production of tools, and for reducing costs as well. It’s getting a lot of attention. It is absolutely growing.”
Icon Technologies and Duo Form both purchased 3D Systems EXT 1270 Titan Pellet 3D printers for their mold production.
The printers have print volumes up to 50 inches by 50 inches by 72 inches, which makes it possible to print most large thermoforming tools. EXT Titan Pellet systems are compatible with a range of nozzle sizes that enable it to print finer layers than other systems, according to the company. When a thermoforming mold requires a finer surface or a tighter tolerance, the optional CNC spindle tool head enables the printer to machine a smoother, more accurate surface without having to move the mold to a separate CNC machine.
“With our Titan printers, thermoforming customers are commonly using the combined 3D printing and milling capabilities in the Titan printer,” Mount said. “It’s kind of a hybrid method to produce that tool. The milling toolhead is optional and not always needed. But a lot of the thermoforming companies we’re working with seem to want the spindle capability included.”
The EXT 1270 Titan Pellet large-format 3D printer features a single pellet extruder as standard, but can be customized with up to three toolheads, including a second pellet extruder, a filament extruder, and a 3-axis milling spindle. Combining the abilities of a pellet extruder with a filament extruder allows a user to print with two materials and select the right extrusion method for their application, according to the company.
Titan Additive LLC (Titan Robotics), of Colorado Springs, Colo., became a part of 3D Systems, Rock Hill, S.C., in February 2022.
Contact information:
3D Systems Inc., Rock Hill, S.C., 803-326-3930, www.3dsystems.com
Icon Technologies Limited, Winkler, Manitoba, 888-362-4266, www.icondirect.com
Bruce Geiselman
Senior Staff Reporter Bruce Geiselman covers extrusion, blow molding, additive manufacturing, automation and end markets including automotive and packaging. He also writes features, including In Other Words and Problem Solved, for Plastics Machinery & Manufacturing, Plastics Recycling and The Journal of Blow Molding. He has extensive experience in daily and magazine journalism.
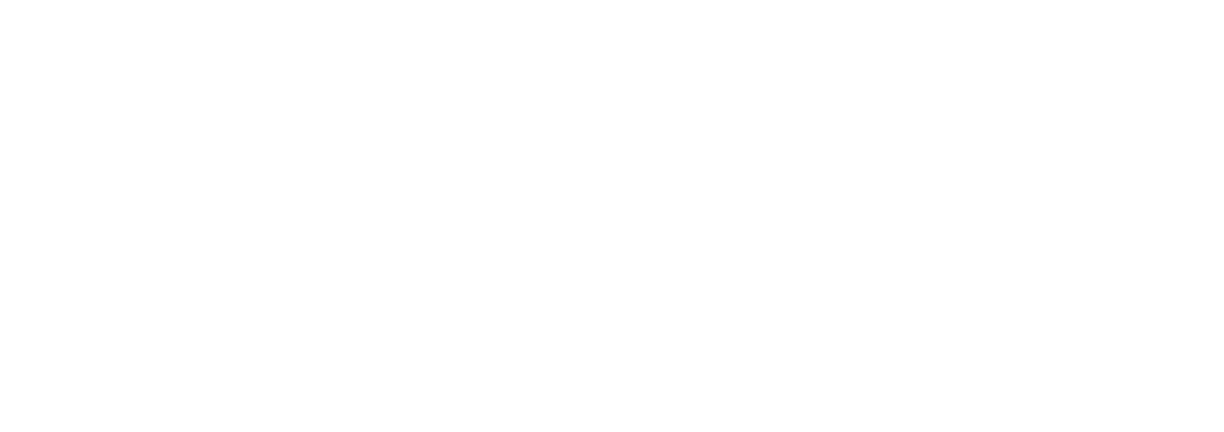