Geiss is offering an optional feature for its T10 thermoforming machine designed to streamline production of painted or screen-printed parts by combining thermoforming and UV curing into a single process.
For automotive parts, acrylic layers on thermoformed sheets have long offered scratch resistance and UV protection for the plastic blends underneath. However, manufacturers of cars, RVs and mobile homes increasingly demand significantly greater scratch resistance.
To improve scratch resistance, acrylonitrile styrene acrylate/PC thermoformed sheets with an acrylic surface are coated with lacquer, which offers a hardened surface. These parts are dried prior to thermoforming but not fully cured. The drying prevents surface damage during handling, but since they are not fully cured, the sheets can be shaped in the thermoforming machine. Normally, the forming process is followed by treatment in a UV tunnel or oven where the coating cures.
However, Geiss has eliminated the need for the additional step by integrating UV curing into the T10 thermoforming machine at the request of two of its customers who supply the automotive industry.
“The component is manufactured within 50 to 60 seconds in one cycle,” said Geiss Managing Director Wolfgang Daum. “There are no further handling processes.”
The technology is impressively simple, Daum said. Toward the end of the forming process, while a vacuum is still being applied to the sheet, a UV unit moves over the part lying on the forming tool and hardens the coating. The UV unit’s movement can be programmed directly through the machine’s control unit, depending on the part height and geometry. Shutters ensure that no UV radiation penetrates outside.
Applying the UV curing process to a part while it is still in the thermoforming machine reduces the risk of part deformation. It also speeds the curing process, along with residual heat.
“We use the residual heat from the molding process so that curing speeds up significantly,” Daum said. “In addition, we have no risk of component distortion because the part remains on the tool until the paint has hardened and the component has cooled down. Only then is it removed.”
Bruce Geiselman, senior staff reporter
Contact:
Geiss LLC, Durham, Conn., 203-988-9426, www.geissllc.com
Bruce Geiselman
Senior Staff Reporter Bruce Geiselman covers extrusion, blow molding, additive manufacturing, automation and end markets including automotive and packaging. He also writes features, including In Other Words and Problem Solved, for Plastics Machinery & Manufacturing, Plastics Recycling and The Journal of Blow Molding. He has extensive experience in daily and magazine journalism.
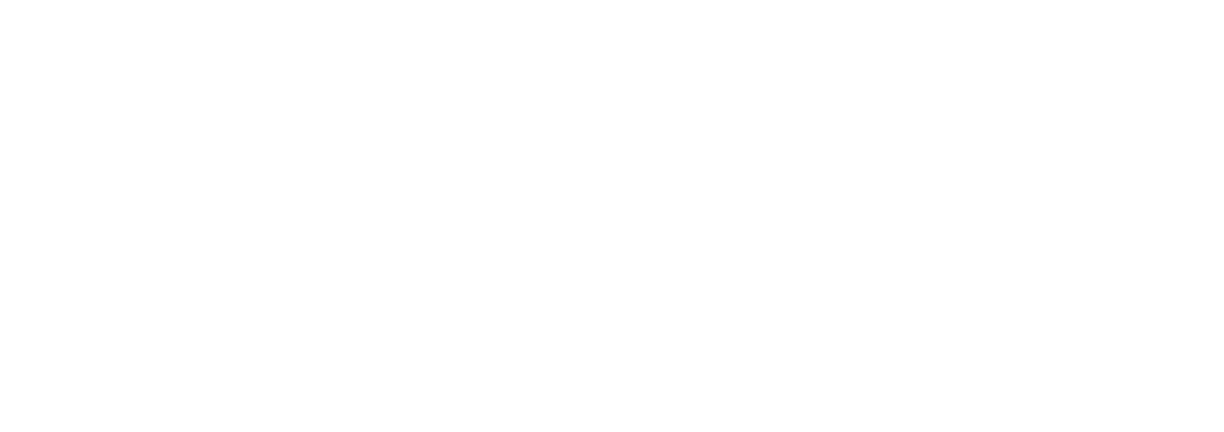