Thermoforming machines can last for decades if they are properly maintained.
That includes regularly scheduled upkeep, such as cleaning and lubricating mechanical systems (including bearings and shafts); inspecting and adjusting the tension of belts and chains; changing the grease on roller screws; changing air filters; and maintaining cutting tools.
“Preventive maintenance can ensure your machine works at optimal efficiency while minimizing unexpected downtime,” said Matthew Terauds, engineering manager at GN Thermoforming Equipment. “If you schedule your proper maintenance and downtime, your overall equipment efficiency will be improved. It allows for regular inspection of your components and pre-ordering of any parts before failure.”
Some GN Thermoforming machines manufactured in the early 1980s are still operating today, Terauds said.
Most processors have dedicated personnel who handle preventive maintenance, Terauds said. However, companies that have difficulty with staffing can purchase maintenance packages from GN in which technicians travel to the customer’s site regularly to inspect and maintain its machines.
In addition, GN technicians can provide customers with remote maintenance and repair assistance using communications platforms such as WhatsApp and Skype that allow for video conferencing. Technical support also can connect to a customer’s machine remotely to troubleshoot issues.
“We can view any errors and look at traces and machine logs, while viewing motor axis indicators such as current or torque, temperature and lag errors,” Terauds said. “We can even update machine programs to the latest version, which can offer customers new features.”
While thermoforming machines may last for four or five decades, there may be reasons for a processor to sell its equipment earlier.
“If a customer needs to move into a different direction or technology, they might need to sell earlier than this,” Terauds said. “Older hydraulic or pneumatic press machines used primarily for polystyrene production may need to be upgraded to servo-controlled presses with higher tonnage for PET production.”
Terauds offered five tips for keeping a thermoforming machine operating at peak efficiency:
Follow OEM guidelines for machine maintenance: Keep a maintenance log and investigate all unexpected changes in performance or sounds.
Follow correct tooling setup procedures: Over time, operators will become familiar with equipment and start taking shortcuts, but this can lead to tooling or machine damage and unexpected downtime. “The risks do not outweigh the rewards,” Terauds said.
Maintain tooling between production runs: Inspect the dies for burrs or rough edges when removing them or if cutting performance changes. Doing so will increase the life of the die and allow for more efficient production runs.
Do not overlook utilities: Air and water quality will affect the performance of the machine. Poor air quality can lead to sticking valves, and poor water quality can reduce the flow required for heat transfer.
Make sure all production staff are properly trained on machine operation and setup: Inexperienced or undertrained staff means a machine will never operate efficiently.
GN’s machines are durable and require minimal maintenance, Terauds said. However, maintaining the press roller screw is critical for machine operation. Terauds knows of a processor who did not grease the roller screw until it completely failed, resulting in an expensive and complicated repair that could have been easily avoided.
Gabler Thermoform
“The advantages of focusing on machine maintenance are significantly longer lifetimes, fewer breakdowns and corresponding production downtimes, also better resource planning, and, in the long term, correspondingly lower repair costs,” said Stephan Gotschol, area sales manager for Gabler Thermoform.
Successful processors follow the manufacturer’s specifications for maintenance schedules.
“In concrete terms, this means that successful manufacturers schedule approximately one hour per week for cleaning and inspection,” Gotschol said.
Failing to perform maintenance correctly can have catastrophic consequences.
“We are aware of a case, for example, where a company lubricated the pre-stretcher of its thermoforming machine with the wrong grease,” Gotschol said. “The consequence was that the pre-stretcher was irreparably damaged after only 1,000 operating hours, which led to a complete replacement of the pre-stretcher and caused a big bill.”
Gabler has developed a system in which information from sensors on customer machines is constantly collected and fed to cloud-based servers where Gabler technicians can evaluate a machine’s performance, Gotschol said. The system has been successfully implemented with the first customers and is being rolled out more widely, he said.
Thermoforming machines that are well-maintained should offer customers a long life of service.
“In our eyes, a machine should be driven for the rest of its life,” Gotschol said. “However, experience shows that machines are replaced after a lifetime of 10 to 15 years in order to keep up with technological development and, above all, the competition.”
Asked to identify the top maintenance steps, Gotschol listed: Following the OEM’s maintenance recommendations; regular inspection by technicians; process analysis by technicians or via teleservice; use of recommended operating materials by the manufacturer; and use of original spare parts.
Geiss LLC
Processors should view preventive maintenance as a “down payment on the cost of having maximum profitability,” said Michael Roche, GM of Geiss. “On the contrary, when maintenance is neglected and the machine ultimately fails as a result, the cost of lost opportunity very quickly exceeds the cost of performing the routine maintenance, in some cases, astronomically.”
Successful processors plan for routine maintenance, they schedule the needed downtime, and they maintain necessary spare parts, Roche said.
Planned maintenance should include: inspecting and testing all safety functions and guarding; keeping machinery clean and lubricated; changing important fluids (coolants, oils and grease); inspecting and changing filters; inspecting and replacing bearings as necessary; and ensuring the integrity of gaskets and seals.
While thermoforming machines typically do not wear out, a processor may decide to replace a unit as technology advances.
“Normally, the steel, aluminum, brass and so on that make up the basic machine structure does not really ‘wear out,’ ” Roche said. “But control system components become obsolete, unavailable and/or unsupported by their manufacturer, so there comes a point in time where it makes sense to invest either in a completely new machine or replace the control system with a state-of-the-art version. Most OEM machine builders do not spend their efforts in rebuilding older machines and retrofitting new controls.”
Normally, the time window for obsolescence on control system components is about 10 to 15 years after their introduction, Roche said.
Bruce Geiselman, senior staff reporter
For more information:
GN Thermoforming Equipment, Chester, Nova Scotia, 902-275-3571, www.gnplastics.com
Gabler North America, Louisville, Ky., 989-615-6365, www.gabler-thermoform.com
Geiss LLC, Durham, Conn., 203-988-9426, www.geissllc.com
Bruce Geiselman
Senior Staff Reporter Bruce Geiselman covers extrusion, blow molding, additive manufacturing, automation and end markets including automotive and packaging. He also writes features, including In Other Words and Problem Solved, for Plastics Machinery & Manufacturing, Plastics Recycling and The Journal of Blow Molding. He has extensive experience in daily and magazine journalism.
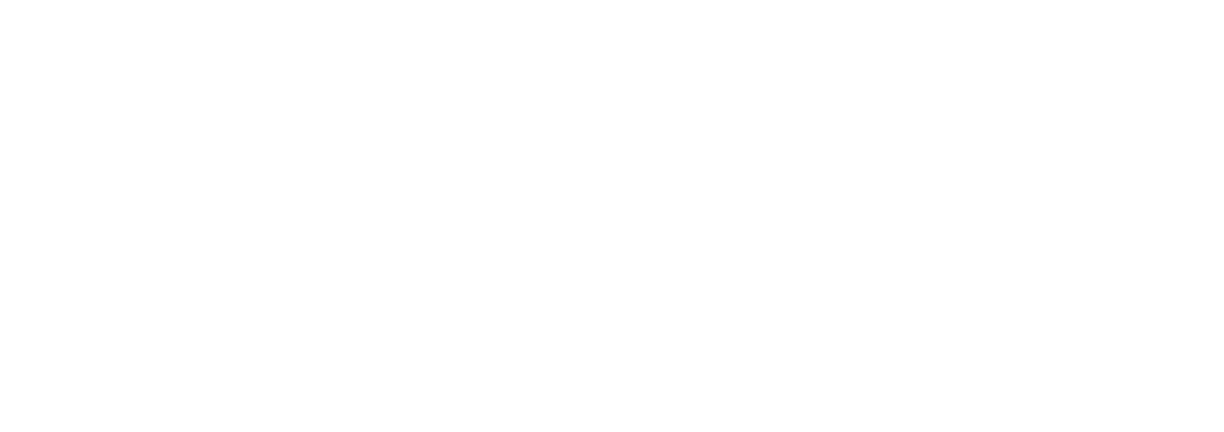