Japanese machinery manufacturer Maruho Hatsujyo Innovations (MHI) has developed the Eagle-Omni blister package machine. It has a small footprint and is aimed at packaging development, materials testing and production.
The Eagle-Omni, with a forming area of 5.9 inches by 3.7 inches, can produce up to 20 blister packs per minute. The standard maximum depth is about 1.2 inches with an option to increase that to about 1.6 inches. The unit forms, seals and punches packs in sequential operations.
It can accommodate forming film up to 19.7 inches wide and lidding film up to 11.8 inches wide.
MHI said the cost-effective, deep-draw Eagle-Omni is capable of everything from manual prototyping to fully automated operation. It features a recipe-driven format change, easy changeovers and versatile feeding solutions.
The Eagle-Omni is suitable for packaging solids, powders, liquids or devices. It handles a wide range of forming materials — including PVC, polyvinylidene chloride, Aclar-brand film, PP and PET — and all typical lidding substrates.
The unit is 6.7 feet long, 2.1 feet wide and 38.1 feet high.
It uses a platen forming and platen sealing operation. The entire mold assembly is bolted to the platen.
The Eagle-Omni is the fourth thermoforming packaging machine to be offered by MHI in the U.S. The servo-driven Eagle-Rx is designed for batch production where quick changeovers are needed. The Eagle-Pro mini blister machine is aimed at production of small-lot orders with multiple products. The manually driven Eagle-Uni Thermoformer has a maximum speed of five cycles per minute.
MHI also announced in April that it has launched a rapid prototyping service using 3-D printing technology for its machinery clients. The service creates test blister pack products.
“The service makes available sample blister cavities nearly identical to final production, saving time and money compared with traditional metal tooling prototypes,” the company said.
MHI said the new service gives its customers the ability to “try before they buy” new or modified packaging, including packages being tested as part of stability studies. The reduced cost also allows testing of multiple designs to determine which is most suitable for a particular product.
“Historically, tooling lead times were measured in weeks, and prototyping was often prohibitively expensive,” product manager Benjamin Voelcker said. “In reducing turnaround times and alleviating costs, our new approach allows customers the time and resources to find blister packaging solutions that best suit their products.”
MHI is a subsidiary of Japanese health-care company Maruho Co. Ltd., which is based in Osaka.
Ron Shinn, editor
Contact:
Maruho Hatsujyo Innovations (MHI), Norwell, Mass., 617-653-1617, www.mhi-innovations.com
Ron Shinn | Editor
Editor Ron Shinn is a co-founder of Plastics Machinery & Manufacturing and has been covering the plastics industry for more than 35 years. He leads the editorial team, directs coverage and sets the editorial calendar. He also writes features, including the Talking Points column and On the Factory Floor, and covers recycling and sustainability for PMM and Plastics Recycling.
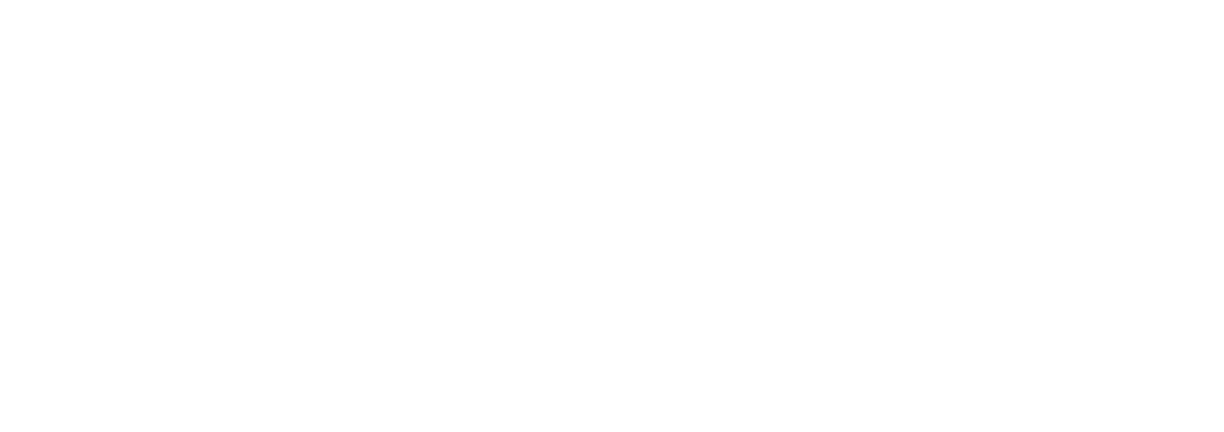