Dolco, one of the biggest thermoforming companies in the country, has found an edge after an acquisition that added extruder and thermoforming machine manufacturing to its capabilities.
Dolco, based in Wayne, Pa., is the umbrella name for a Tekni-Plex Inc. business unit that in 2018 bought sister manufacturing companies Commodore Technology and Commodore Plastics — known for building equipment and producing PS foam food trays, respectively. Commodore Plastics has been absorbed under the Dolco name, while Commodore Technology continues to make machinery.
“This arrangement has given us some advantages over the years,” said Fritz Seager, director of operations at Commodore Technology. “The biggest advantage has probably been in the tooling. When a customer wants something different, something unique to differentiate their product, we can go from concept to full-on production in under eight weeks.”
During a recent Plastics Machinery Magazine tour of the Dolco campus in Bloomfield, N.Y., where Commodore had its headquarters, it was clear that the combination of capabilities gives Dolco a unique and interesting advantage as a foam packaging manufacturer.
Commodore Technology manufactures PS foam extrusion systems, dies, thermoforming machines, trim systems, molds and other equipment. Originally established to build equipment for its sister company, Commodore Technology started selling machinery outside the contiguous U.S., particularly in South America, Central America and the Caribbean in 1988. In addition to supplying the Dolco campus in Bloomfield, it is now beginning to supply equipment and machinery-related services to some of Dolco’s other four packaging plants.
Every thermoforming machine that has been built by Commodore, whether for its own use or for outside customers, has been slightly improved from the previous machine, Seager said. “Every single one has some changes that make it better, more efficient or cheaper to build,” he said.
“There is nothing fancy about this equipment,” he said. “It is built with off-the-shelf parts without a lot of proprietary stuff. Maintenance and repairs are easy.”
Chuck Gallagher, VP of business development for Dolco, touted the equipment's versatility. “The simplicity of the equipment, along with its low price, makes it a very good fit for developing markets,” he said. “They need to be making plates, bowls, hinged-lid containers and trays all in the same plant. So, they need equipment that is much more flexible.”
Commodore markets five thermoforming machines. Three can accommodate sheet 20 inches to 30 inches wide and different size molds; two are for sheet 32 inches to 46 inches wide. It builds grinders and trim presses for the thermoforming machines. It also offers four extruders, as well as mold design and building services for trays and plates, hinged-lid containers, industrial carrier trays and custom molds for any thermoforming machine.
Founded in 1980 by George Braddon, Commodore manufactured a broad range of PS food trays and padded trays used by food processors and supermarkets, as well as in industrial applications.
The Bloomfield thermoforming plant specializes in products that can be produced using narrow rolls of material. These types of products generally mean shorter runs and more frequent machine changes. Dolco’s other plants run mostly wide-width material.
There is a historical explanation for that specialization. Braddon was an engineer at nearby Mobil Chemical, one of the largest foam plants in the world at the time, where there was an emphasis on wide rolls and long production runs.
“They would bring in a piece of equipment, get it up and running and never turn it off. Their business just exploded,” said Brad Braddon, George’s son, who ran both Commodore businesses for 12 years before they became part of Dolco. He is now VP for government affairs at Dolco Packaging.
“My father was entrepreneurial and saw what he thought would be a great opportunity in the lower-volume business Mobil turned down.”
As he pursued his plan, George Braddon found that the big, wide-roll thermoforming machines in common use at the time were not very efficient for short runs and frequent changeovers. He acquired an obsolete, first-generation thermoforming machine from a company that had gone out of business and rebuilt it for his needs. He later did the same again and again as Commodore’s plastic packaging business grew.
“I’m not sure that there was a lot of commercial equipment available at that time that would do the different things people wanted to do,” Seager said.
The extrusion and thermoforming equipment George Braddon designed and built for his own niche markets for foam trays was simple and flexible, and permitted quick product changes. “It caught some other eyes and was introduced to other markets that couldn’t afford or justify the expense of large-capacity equipment that was commercially available,” Seager said. “So, it worked out pretty well.”
Braddon found that selling extruders, thermoformers, tooling and auxiliary equipment allowed him to maintain the machine- and tool-building capability in-house. Commodore decided to sell machinery only outside the contiguous U.S. so that its foam packaging customers would not perceive Commodore as also selling machinery to its competitors.
The first exported machines went to plants in Puerto Rico and Jamaica.
Seager said that George Braddon “is really a smart guy and very resourceful. He would get a design idea, put something together in his machine shop to see what worked and then fix what did not work.”
Today, that do-it-yourself spirit is still evident at Dolco. It uses machines and equipment built on-site by its Commodore unit. This gives Commodore special expertise in setting up turnkey lines. “We are a really good fit for someone who’s new in getting into the business because we can hold their hand,” Gallagher said. “We have really good experience at actually running a plant.”
Most of the auxiliary equipment for the thermoforming lines also is built in-house.
The plant processes PS and recycled PS.
The product mix means the plant must make several changeovers in every 24-hour period. The plant runs 24/7.
Individual orders are shipped from stock that Dolco keeps on hand based on the customer’s ordering history. All production is to replace the stock supply.
The plant is not highly automated. “Our campus is not very big,” Gallagher said. “We are running a lot of variety, which doesn’t lend itself to automation, but we run an efficient process overall.” Big bundles of finished products are wrapped and moved by clamp truck.
One company official estimated that the Bloomfield plant, with its narrow-sheet machines, multiple sheet widths and fast changeover capabilities, is 10 percent more efficient in using material than most wide-sheet plants.
“They have to fit every item they make into one sheet width,” he said. “We make all our molds as tight as we can form them, and we adjust the sheet width to match. That is very unique.”
Even with the unique machinery-building capability in the building next door, the processing plant is committed to investing in maintenance to keep its machinery running. “The philosophy isn’t to run it into the ground and replace it,” Seager said. “It is to keep it running as if it was new for the entire time that we own it. We think it is always cheaper to maintain a piece of equipment than run it until it dies.
“One of the things we see is that on the older machines, the heating control isn’t as good as the newer machines, so we’ve replaced all the heating with more zones, different types of heaters and controls.”
The advantage of having a dedicated machinery supplier is spreading to other Dolco processing plants. Two other plants already have Commodore thermoformers and auxiliary equipment, and all four have tooling built at the Bloomfield location.
Commodore Technology is a well-known name in the areas of the world where narrow-width sheet thermoformers are popular but is not familiar to processors in the U.S. “Worldwide, I would say we are fairly well-known,” Gallagher said. “We are not the biggest seller of machinery, but we are really well-known in the markets where our footprint is a good fit.”
Ron Shinn, editor
Just the Facts
COMPANY: Dolco Packaging and Commodore Technology, a division of Dolco Packaging
PARENT COMPANY: Tekni-Plex Inc.
PLANT VISITED: Bloomfield, N.Y.
EMPLOYEES: 175 in Dolco Packaging; 28 in Commodore Technology
PRIMARY BUSINESSES: Dolco Plastics makes foam packaging for food and other uses; Commodore Technology makes PS foam extrusion systems, dies, thermoforming machines and associated equipment.
YEAR DOLCO ACQUIRED THE PLANT: 2018
Contact:
Dolco Packaging, Bloomfield, N.Y., 585-657-6110, www.tekni-plex.com
Ron Shinn | Editor
Editor Ron Shinn is a co-founder of Plastics Machinery & Manufacturing and has been covering the plastics industry for more than 35 years. He leads the editorial team, directs coverage and sets the editorial calendar. He also writes features, including the Talking Points column and On the Factory Floor, and covers recycling and sustainability for PMM and Plastics Recycling.
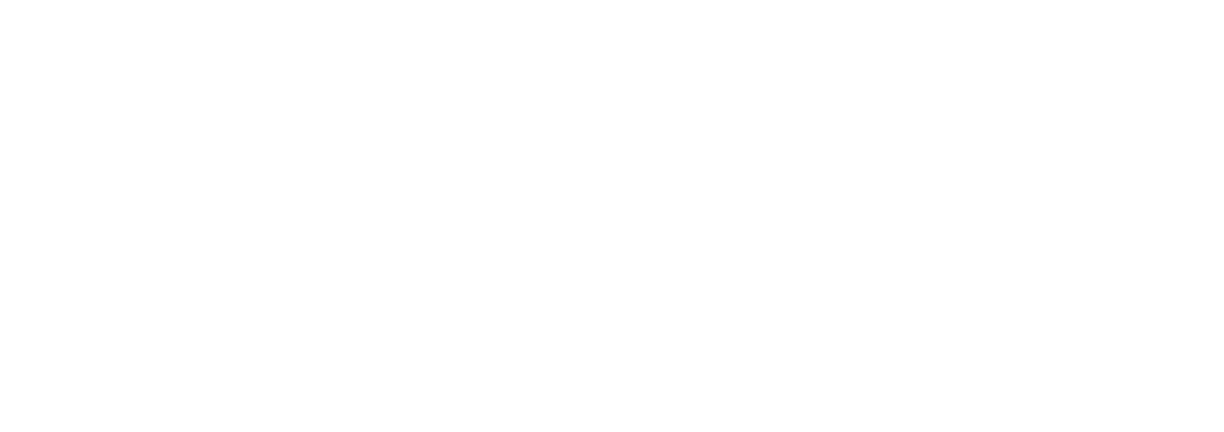