LF-Sizer Designed for blown film lines, D.R. Joseph's layflat control system takes measurements soon after the frost line to ensure the bubble is the proper size. Suitable for use with both large and small dies, the system includes two sensors as standard, with the possibility of expansion to four sensors. It can detect a number of problems, including air leaking out of the bubble, thermal air expansion upon startup, and ambient air or process changes up or down the frost line. Standard compressed air under at least 70 pounds per square inch of pressure is required.
What's new? An optional control feature for non-internal-bubble cooling film lines. The new control uses an ultrasonic sensor facing the bottom of the bubble flare to measure neck height, then coordinates the competing tasks of managing layflat width and neck height during startup, hole recovery and normal production. It uses information from the ultrasonic sensor to vary air-ring blower speed, which controls neck height. The information is communicated by standard serial data communication to an A1000, P1000 or V1000 inverter from Yaskawa America Inc., Waukegan, Ill.
Benefits Establishment of the set point to within 0.25 inch. By coordinating the layflat width and neck height, the optional feature reduces time from startup to production and improves the production rate. Controlling and maintaining neck height on high- and medium-stalk bubbles improves consistency of the properties, such as impact strength, of HDPE and medium-density PE film. Users can also experience better layflat control and elimination of dart impact failures.
D.R. Joseph Inc.,Arlington, Texas, 817-987-2030, www.drjosephinc.com
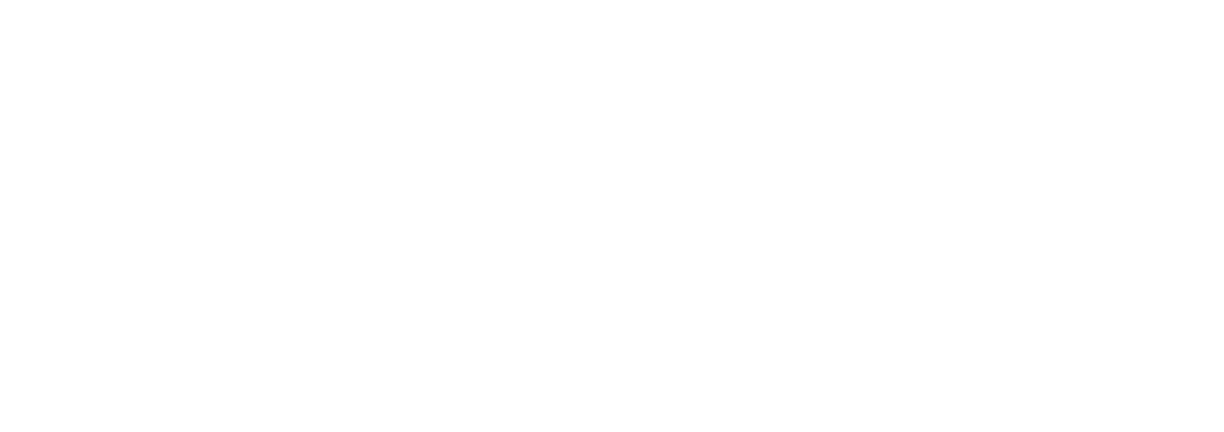