By Julie Holmquist and Lisa Eischens
Cortec Corporation
Plastic injection molds can cost tens of thousands of dollars. This makes corrosion protection a top priority to avoid asset deterioration. Unfortunately, molders often find that traditional rust preventives clog mold pores and require extra work to clean off before the molds can be used.
Molders frequently also lack sufficient indoor storage space for molds, forcing them to place costly equipment outdoors where it is at greater risk for deterioration from harsh elements such as wind, rain, sun and fluctuating temperatures. Then when they bring the mold in to be used, they too often have to spend extra time and effort de-rusting the equipment before putting it into service.
The good news is that there are other ways to protect molds effectively and efficiently from corrosion. These products have received a warm welcome in the tool and die industry over the last couple of years because they solve practical problems for molders in a remarkably easy way.
Rust Prevention on the Surface of the Mold
The internal surface of the mold that actually forms the injected plastic is one of the most critical components to keep corrosion-free. Some important worker safety and environmental advantages can be found in protecting this surface with a partially biobased, non-traditional aerosol product like Cortec’s EcoAir Tool & Die Rust Preventative.
EcoAir Tool & Die Rust Preventative also excels in protective abilities. In humidity testing, it lasted three times longer before failure than Quaker Ferrocote 61 MAL HCL 1, a petroleum-based product commonly used in steel processing. It also significantly outperformed Henkel Pennsteel 100, another rust preventive used in steel coil processing.
Rust Preventive | Time to Failure (Hours) |
None (Control) | 24 |
Quaker Ferrocote 61 MAL HCL 1 | 216 |
Henkel Pennsteel 100 | 432 |
EcoAir Tool & Die Rust Preventative (aka VpCI-325) | 648 |
*Cortec Laboratories Project #12-228-1825.bis
The bag-on-valve spray can allows easy atomization over a large surface area, like that of a plastic injection mold. The product itself offers a degree of cleaning action to displace water, grime and process fluids from the surface of the metal. Perhaps the biggest advantage is that workers do not have to clean EcoAir Tool & Die Rust Preventative off the mold before the mold can be used, saving time and worker hassle.
Outer Protection of the Mold
The outside of the plastic injection mold also needs protection. This may be required during storage or overseas shipment. In either case, the mold could face weeks — or perhaps even months — in an uncontrolled environment, sometimes traveling overseas or just sitting in an unprotected storage yard.
MilCorr VpCI Shrink Film is a particularly durable plastic film that contains corrosion inhibitors and UV-resistant additives for protection in such circumstances. As evidence of its versatility and durability, MilCorr VpCI Shrink Film has been used in military and offshore storage applications and has performed well even in several cases of hurricane weather.
The corrosion inhibitors protect the metal surfaces from rusting, while the UV additives protect the film from deteriorating in the sunlight. MilCorr VpCI Shrink Film is relatively easy to apply simply by cutting the right size of material, wrapping it around the injection mold and heat-shrinking the edges.
Extra Insurance for Internal Surfaces
Because injection molds are so large, so valuable and sometimes make such long trips from the manufacturer to the end user, suppliers typically want to do all they can to avoid corrosion en route. Otherwise, the customer may reject the piece, requiring more rework and shipping expenses for the supplier. Given these costs (which vary from case to case), it is often worth buying even a little extra protection to be sure this does not happen.
One simple and cost-effective option is to add a VpCI-309 Pouch inside the cavity. These pouches consist of Vapor phase Corrosion Inhibitors packaged in a breathable bag that allows the corrosion inhibitor molecules to diffuse and condition the void space. These Vapor phase Corrosion Inhibitors travel throughout the cavity as a vapor and attach (or “adsorb”) themselves onto the metal surfaces with which they come in contact, forming an invisible protective layer on the inside of the mold.
Their vapor action allows them to protect hard-to-reach cavities or areas that might have been missed during traditional liquid rust preventive application. The same vapor-phase action will also enable the corrosion inhibitors to float away after the cavity is opened, eliminating the need to clean this protective layer off the metal before the tooling can be used.
The Cortec Suite of Corrosion Inhibitors in Action
An example of how these materials can be used in everyday life was demonstrated in early 2019, when a mold and die manufacturer took the following steps to protect a 40,000-pound (18,144-kilogram) P20 two-cavity automotive interior plastic injection mold from corrosion on its way from Michigan to Europe. The mold needed five to six weeks of protection as it traveled overseas to the client’s facility.
The shipment was successful. While the client was pleased with the level of protection (no corrosion occurred), they were also happy with side benefits such as package appearance and ease of product removal (or lack of removal, in the case of EcoAir Tool & Die Rust Preventive). They wanted their supplier to use the same method on future molds — which was doubly good news for the supplier, considering this method was about half the cost of traditional oils and greases.
There is a lot to learn from this story of protecting a P20 plastic injection mold. These same strategies can be used in just about every stage of a new mold’s life cycle — from shipment to storage. And the methods are easy enough for practically any mold manufacturer or user to start benefiting from them right away.
Contact Cortec for more information: www.cortecvci.com.
Author bios:
Notes:
Cortec Case History 626: Automotive Tool and Die Preservation. Cortec Corporation: Saint Paul, MN. May 2019. https://www.corteccasehistories.com/?s2member_file_download=access-s2member-level1/ch626.pdf.
Special thanks to Jessica Carpenter Glanz ([email protected]) for consultation regarding the tool and die industry.
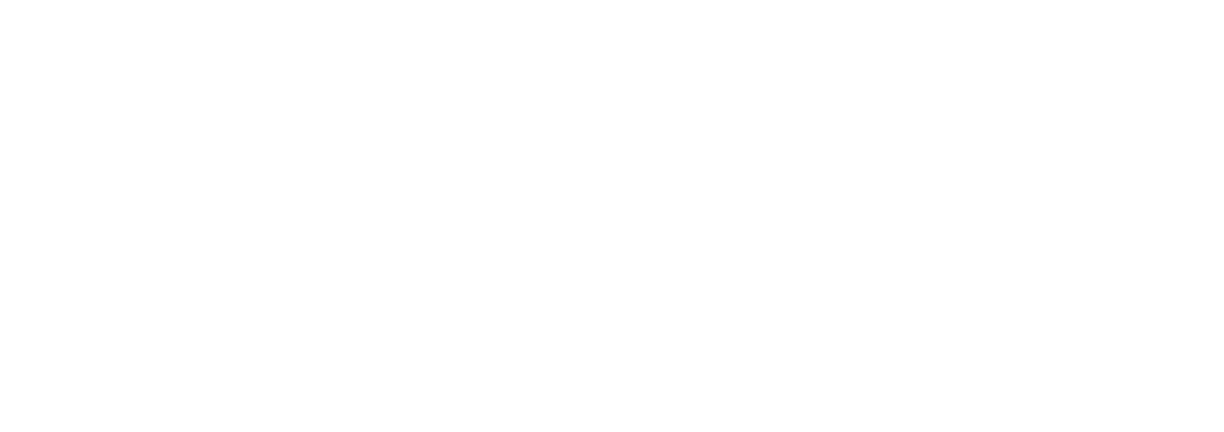