DeepHow uses AI to help manufacturers deal with skilled labor shortage
By Bruce Geiselman
AI-powered videos can help manufacturers quickly train workers, according DeepHow, a company that has put generative artificial intelligence (AI) to work toward that goal.
Plastics processors, and manufacturers in general, are facing an economic downturn at the same time they confront a labor shortage exacerbated by both the COVID pandemic and a growing number of retirements within the manufacturing workforce, which is made up largely of aging baby boomers.
Workforce participation remains below pre-pandemic levels, according to the U.S Chamber of Commerce in a Sept. 11 post titled “Understanding America’s Labor Shortage.” There are 1.5 million fewer Americans working today compared to February 2020.
Skilled workers are leaving the workforce through retirement and taking their training and knowledge with them, said Sam Zheng, CEO and co-founder of DeepHow. Manufacturers need a plan for replacing exiting workers, and for retaining the know-how that is vanishing with these industry veterans.
Traditional one-on-one apprenticeship training, only possible if experienced machine operators are still on staff, can be expensive, Zheng said. Training manuals often are available to workers, but he said younger workers learn better through visual instruction. Eighty-five percent of millennial and Gen Z workers prefer to learn from videos, he said.
“These younger-generation workers grew up learning very differently,” he said. “They are not reading manuals or your work instructions or traditional SOP documents. In fact, the longer the document, the less likely they are going to read it. They prefer to go online to watch videos on YouTube and TikTok. That’s why we thought about how we can leverage these more-engaging ways of delivering content.”
However, traditional editing of video content to produce step-by-step instructions can take a lot of time and employee effort, which is why Zheng began looking into how AI could automate the process.
Zheng, who has a doctorate in engineering psychology and was a former research scientist with Siemens, helped develop Stephanie, an AI platform that streamlines know-how capturing and knowledge transfer with simple, intuitive user interfaces.
Using a smartphone camera and app, users can record industry experts, such as experienced injection molding machine operators, performing their regular job duties while describing what they are doing. Stephanie’s workflow indexing software then uses AI technology, including natural language processing and image analysis, to extract useful workflow information from the video, organize and edit it, and turn it into useful step-by-step guidance expressed in an easy-to-follow format. The step-by-step guidance, with audio and closed captioning, is then saved to an online portal that allows workers to log in anywhere and anytime to interact with Stephanie and proceed at their own pace.
The platform also takes aim at another challenge companies face — language barriers, which can lead to misunderstandings, loss of productivity and a stressful work environment. Misunderstandings about procedures can lead to serious accidents, injuries or even death. To combat the problem, Stephanie uses generative AI to translate its instructional videos into more than 40 languages with both audio and closed captioning.
Stephanie can significantly trim training costs, according to DeepHow. Zheng said Stephanie can:
- reduce training time by 25 percent with direct productivity impact,
- reclaim 20 percent of an expert’s time by offloading training duties and job shadowing, and
- accelerate workforce onboarding by 40 percent, thus reducing the impact of high churn.
The DeepHow platform can keep track of which workers have watched which videos, as well as the skills particular workers have, so plant operators can make more-optimal resource allocations.
As AI technology advances, many fear that the technology may be used to replace workers. That’s not how Zheng sees Stephanie, though.
“But for us, we want to use the technology to help people train people, not to replace them,” he said.
More than 80 customers ranging from small businesses and organizations to large businesses are using DeepHow’s AI platform at more than 500 sites in 28 countries across six continents, according to the company.
Contact information:
DeepHow Corp., Royal Oak, Mich., [email protected], www.deephow.com
Bruce Geiselman
Senior Staff Reporter Bruce Geiselman covers extrusion, blow molding, additive manufacturing, automation and end markets including automotive and packaging. He also writes features, including In Other Words and Problem Solved, for Plastics Machinery & Manufacturing, Plastics Recycling and The Journal of Blow Molding. He has extensive experience in daily and magazine journalism.
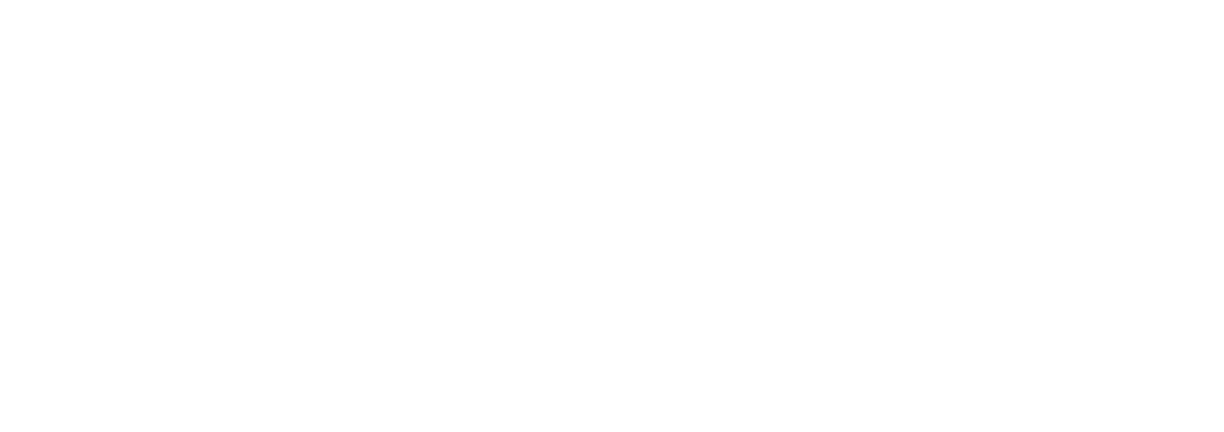