Not a Six Sigma black belt? What’s lean manufacturing, you ask?
Here’s what a couple practitioners mean when they speak of lean:
- “Identify what works well and ... focus on doing the things we do well, better, and more frequently.” — Carl Livesay, GM of Mercury Plastics in Baltimore
- “Think of lean simply as a gap of where we are now to where we want to be.” — David Rizzardo, associate director of the Maryland World Class Consortia (MWCC) and author of the text, “Lean – Let’s Get It Right!”
- “A strategy designed to embed a culture of continuous improvement where everyone strives to eliminate waste in company processes by utilizing the appropriate tools to add ever-increasing value for the customer” — “Lean – Let’s Get It Right!”
Courtesy of the Maryland World Class Consortia Ltd., which provides employers with lean training, here are some abridged definitions of other key concepts to thinking lean:
Benchmarking
The process of measuring products, services and practices against those organizations known to be leaders in one or more aspects of their operations.
Bottleneck
The slowest operation (choke point) in a manufacturing process. Do not confuse this with a company’s “constraint” taken from TOC (Theory of Constraints), which is the slowest operation in an entire manufacturing system that, if remedied, would increase overall company throughput.
Brainstorming
A technique teams use to generate ideas on a particular subject. Each person on the team is asked to think creatively and write down as many ideas as possible. The ideas are not discussed or reviewed until after the brainstorming session.
Cost of Poor Quality (COPQ)
The costs associated with providing poor quality products or services. There are four categories: internal failure costs (costs associated with defects found before the customer receives the product or service), external failure costs (costs associated with defects found after the customer receives the product or service), appraisal costs (costs incurred to determine the degree of conformance to quality requirements) and prevention costs (costs incurred to keep failure and appraisal costs to a minimum).
DMAIC
A Six Sigma structured problem-solving methodology: define, measure, analyze, improve and control.
Eight Wastes
The original seven wastes typically found in mass production:
- Overproduction — producing ahead of customer or next process demand
- Waiting — operators standing idle waiting for the next processing stop
- Transportation — unnecessary transport of materials
- Overprocessing — performing unnecessary or incorrect processing due to poor tool and product design
- Inventory — having more than the absolute minimum inventory needed
- Motion — unnecessary movement by employees during the course of their work
- Defects — production of defective parts.
An eighth waste is commonly recognized as underutilized resources or human imagination.
Error & Mistake-Proofing (a.k.a. Poka-Yoke)
A manufacturing technique of preventing errors by designing the manufacturing process, equipment and tools so that an operation literally cannot be performed incorrectly.
Failure Mode Effect Analysis (FMEA)
A systematized group of activities to recognize and evaluate the potential failure of a product or process and its effects, identify actions that could eliminate or reduce the occurrence and document the process.
5S
A method of workplace organization and visual controls developed by Hiroyuki Hirano. It is a structured and disciplined method of organizing and running the workplace — factory, office or service sector activity — for improved productivity, safety, and quality at reduced cost and higher efficiency. The five terms starting with “S” are:
- Sort means to separate needed tools, parts and instruction from unneeded materials and to remove the latter.
- Set-in-order means to neatly arrange and identify parts and tools for ease of use.
- Shine means to conduct a cleanup campaign.
- Standardize means to conduct sort, simplify and scrub activities at frequent intervals to maintain a workplace in perfect condition.
- Sustain means to form the habit of always following the first four steps.
Flow
A main objective of the Lean production effort, and one of the important concepts that passed directly from Henry Ford to Toyota. Ford recognized that, ideally, production should flow continuously all the way from raw material to the customer, and envisioned realizing that ideal through a production system that acted as one long conveyor.
Gemba
A Japanese word (occasionally genba) that literally means “the real place,” used in process improvement contexts to refer to the place where value is added, such as a manufacturing area or a workshop. Gemba refers to any work area where humans create value.
Gemba Walk
A term used to describe personal observation of work taking place in the gemba. Companies adhering to Lean principles will often have regularly scheduled gemba walks by executives/managers.
Just-In-Time (JIT)
JIT is a system for producing and delivering the right items at the right time, in the right amounts. The key elements of JIT are flow, pull, standard work and takt time. Principles that are fundamental to time-based competition include waste elimination, process simplification, set-up and batch-size reduction, parallel processing and layout redesign.
Jidoka
Stopping a line automatically when a defective part is detected. Any necessary improvements can then be made by directing attention to the stopped equipment and the worker who stopped the operation. The jidoka system puts faith in the worker as a thinker and allows all workers the right to stop the line on which they are working.
Kaizen
Non-value-added waste (or “Muda”) exists everywhere, related to people, materials, facilities and production set-up. Kaizen refers to the series of activities whereby instances of waste are eliminated one by one at minimal cost, by workers pooling their wisdom. The whole secret to Kaizen is to create an atmosphere, a culture of continuous improvement, by focusing people on problems. In short, Kaizen means continuous improvement through incremental improvement.
PDCA (Plan, Do, Check, Act)
The PDCA Cycle is a systematic series of steps for gaining valuable learning and knowledge for the continual improvement of a product or process. ...
- Plan: This involves identifying a goal or purpose, formulating a theory, defining success metrics and putting a plan into action.
- Do: The components of the plan are implemented, such as making a product.
- Check: Outcomes are monitored to test the validity of the plan for signs of progress and success, or problems and areas for improvement.
- Act: This step closes the cycle, integrating the learning generated by the entire process, which can be used to adjust the goal, change methods or even reformulate a theory altogether.
These four steps are repeated over and over as part of a never-ending cycle of continual improvement.
Point-Of-Use Storage (POUS)
What you need where you need it. All material is stored where it is going to be used in the process. POUS reduces material handling requirements and makes it easier to determine raw material needs due to smaller shipments from vendors.
Root Cause Analysis
A problem-solving methodology that focuses on resolving the underlying problem instead of applying quick fixes that only treat immediate symptoms of the problem. A common approach is to ask “why” five times — each time moving a step closer to discovering the true underlying problem. Root cause analysis helps to ensure that a problem is truly eliminated by applying corrective action to the “root cause” of the problem.
Six Sigma
Six Sigma is a methodology that provides businesses with the tools to improve the capability of their business processes. This increase in performance and decrease in process variation leads to defect reduction and vast improvement in profits, employee morale and quality of product.
Takt Time
The pace of production (e.g. manufacturing one piece every 34 seconds) that aligns production with customer demand. Calculated as planned production time divided by customer demand. This helps provide a simple, consistent and intuitive method of pacing production. Is easily extended to provide an efficiency goal for the plant floor (actual pieces divided by target pieces).
Total Productive Maintenance (TPM)
A set of techniques, originally pioneered by Denso in the Toyota Group in Japan, to ensure that every machine in a production process is always able to perform its required tasks.
The approach is termed total in three senses. First, it requires the total participation of all employees, not only maintenance personnel but line managers, manufacturing engineers, quality experts and operators. Second, it seeks total productivity of equipment by focusing on all of the six major losses that plague equipment: downtime, changeover time, minor stops, speed losses, scrap and rework. Third, it addresses the total life cycle of equipment to revise maintenance practices, activities and improvements in relation to where equipment is in its life cycle.
Unlike traditional preventive maintenance, which relies on maintenance personnel, TPM involves operators in routine maintenance, improvement projects and simple repairs. For example, operators perform daily activities such as lubricating, cleaning, tightening and inspecting equipment.
Value-Stream Mapping
A simple diagram of every step involved in the material and information flows needed to bring a product from order to delivery. Value-stream maps can be drawn for different points in time as a way to raise consciousness of opportunities for improvement. A current-state map follows a product’s path from order to delivery to determine the current conditions. A future-state map deploys the opportunities for improvement identified in the current-state map to achieve a higher level of performance at some future point.
In some cases, it may be appropriate to draw an ideal-state map showing the opportunities for improvement by employing all known Lean methods including right-sized tools and value-stream compression.
More on lean manufacturing
Comco and Mercury Plastics show how they've improved through cutting waste.
Help is available to get smaller firms into lean manufacturing.
In-house program guides Engel through supply chain and labor challenges.
Commentary: Your workers are the key to continuous improvement.
Karen Hanna | Senior Staff Reporter
Senior Staff Reporter Karen Hanna covers injection molding, molds and tooling, processors, workforce and other topics, and writes features including In Other Words and Problem Solved for Plastics Machinery & Manufacturing, Plastics Recycling and The Journal of Blow Molding. She has more than 15 years of experience in daily and magazine journalism.
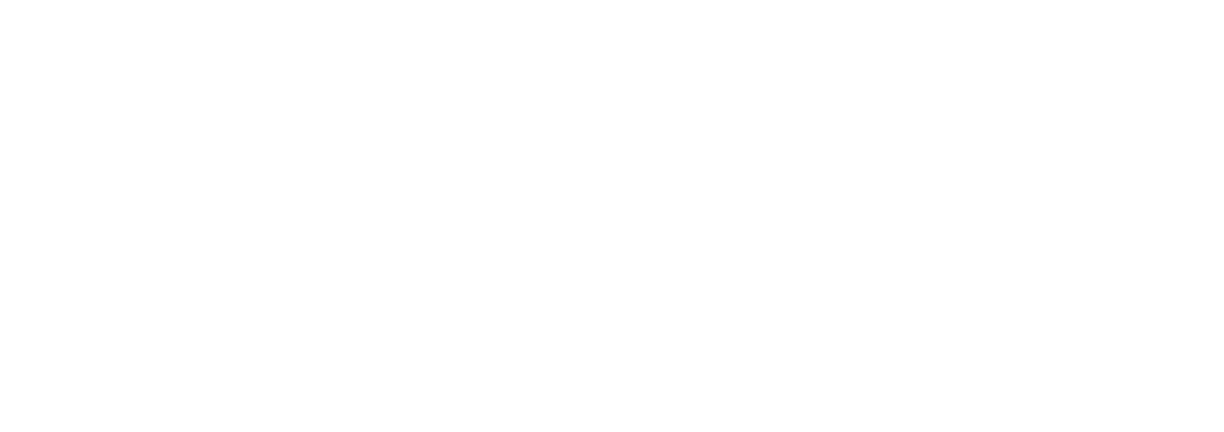