By Bruce Geiselman
Software available for free from a Canadian automation company can help manufacturers design, order and deploy their own automation cells.
With Vention’s Manufacturing Automation Platform (MAP), small to medium-sized manufacturers that previously couldn’t afford automation systems can take on automation more cost effectively and quickly, company CEO Etienne Lacroix said.
“We serve a decent amount of injection plastic manufacturers,” Lacroix said. “At Vention, we try to solve what we call the democratization of industrial automation. We want to make it simple for the professional that we find on each shop floor and manufacturing floor.”
Earlier in his career, Lacroix was an automation systems integrator, and he knew those services were not cheap.
“It’s very costly for manufacturers to acquire automated technology, and also it’s very risky for the provider of technology.”
Integrators often need to put in a lot of hours of manual engineering in adopting automation solutions for clients, and that can increase costs.
“Vention’s goal was to solve all that by productizing, or ‘Legofying,’ if I can use the Lego expression, that problem,” Lacroix said. “What we decided to build is what we call a MAP where users that are not necessarily control experts or robotics experts could self-serve themselves. … There are four capabilities: the act of design, the act of automating, the act of ordering and the act of deploying. We’re providing a hardware-software continuum along those capabilities to make sure that users can be successful by themselves without the need to work with an engineering firm or external service firm.”
Manufacturers using Vention’s cloud-based software can avoid using an“As a result, you’ll lower the cost of automation and make it available to significantly more manufacturing shops than today in the United States,” Lacroix said. “Today, around 80 percent of manufacturing sites have little to no automation.”
High-mix manufacturers typically find it more difficult to automate profitably, he said.
Vention software can walk manufacturers through choosing, purchasing and installing equipment for various tasks including palletizing, box erecting for case packing, machine tending, bin picking, and so on.
“We have around 16 applications that live on top of the Vention platform for which there is a very productized offering that users can leverage,” Lacroix said.
MAP includes various components.
MachineBuilder is 3D CAD software that offers users a fast and easy way to design and order industrial equipment. It is loaded with thousands of modular parts and smart design tools, with real-time pricing. Industrial equipment can be created in minutes from a web browser.
A second component, MachineLogic, offers no-code/low-code industrial automation programming that can simulate how industrial automation equipment designed using MachineBuilder would perform once deployed.
A third component, MachinePortal, enables collaboration among multiple parties on industrial equipment projects.
MachineCloud, a new software addition to Vention’s manufacturing automation platform, links the real automation cell and its digital twin. With MachineCloud, users can connect their automated equipment or robot cell designed on the Vention platform to the cloud, allowing the physical equipment to be controlled directly from the web browser and eliminating the common hassle of hardware and software commissioning, according to the company.
If a customer runs into problems or has questions about designing an automation cell, the customer can ask for a design review by a Vention application engineer, Lacroix said.
“We’ll have somebody here connecting with you that can see your intent, see the design you have started, for example, and help you finish that design and also make sure you have the right components,” Lacroix said. “Today, I would say around 40 percent of our client projects are entirely self-serve and 60 percent will receive some level of assistance from our team of application engineers.”
In addition to saving customers money, Vention’s services also can save clients time in adopting automation, Lacroix said.
“The time saving is even greater because it’s around three to five times faster,” he said. “First of all, we ship most of our orders the next day. The fact that you do everything in the same environment, you design your program, you order and you deploy in the same software continuum, the single digital thread, saves you a lot of software and human interface. As a result, it compresses project cycle time quite significantly.”
Once the automation equipment arrives, customers have the option of installing it themselves using detailed instructions provided by Vention or paying extra to have Vention’s technical staff do it for them.
Founded in 2016, Vention has 3,000 clients in North America and Europe and 14,000 machines in the field. In addition to its headquarters in Montreal, it has offices in Boston and Berlin.
Bruce Geiselman, senior staff reporter
Contact:
Vention, Montreal, Quebec, 800-940-3617, https://vention.io
Bruce Geiselman
Senior Staff Reporter Bruce Geiselman covers extrusion, blow molding, additive manufacturing, automation and end markets including automotive and packaging. He also writes features, including In Other Words and Problem Solved, for Plastics Machinery & Manufacturing, Plastics Recycling and The Journal of Blow Molding. He has extensive experience in daily and magazine journalism.
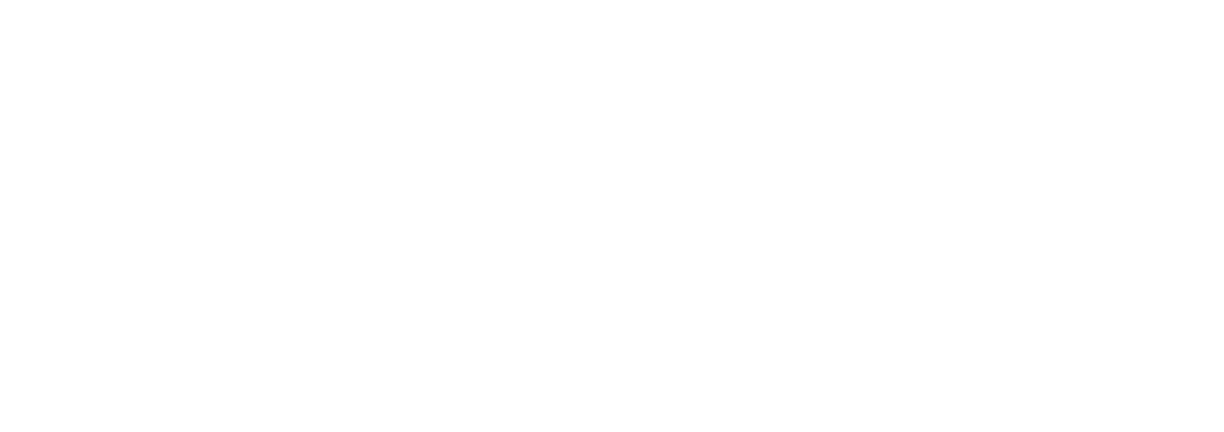