Cobot system developed to handle labor-intensive material removal
By Bruce Geiselman
Kane Robotics’ new Grit cobot is designed to work alongside humans to perform a variety of labor-intensive tasks including sanding, grinding, deburring and polishing in industries ranging from aerospace to construction.
The cobots work with materials including plastics, composites, wood, aluminum and steel, said Alan Hiken, company COO.
Kane Robotics isn’t a manufacturer of components, but it integrates end-of-arm tooling from companies including Applied Automation, ATI Industrial Automation and FerRobotics. The robot arms are manufactured by Universal Robots or Fanuc, depending on a customer’s preferences.
“There are many manufacturers of cobot arms, many manufacturers of end-of-arm tools, and we’d like to think we pick the best ones out there for our customers and put those into a turnkey finished solution,” Kane Robotics CEO John Spruce said.
“The Grit family of systems are pre-engineered. They’re prefabricated. When a customer orders a system from us, we can deliver them in a few short weeks. We’re up and running typically in a day or maybe two. We’re able to do that because we have standard designs and the customization that is necessary is limited.”
Kane demonstrated its collaborative robot system at Automate 2023, May 22-25, in Detroit, in conjunction with its end-of-arm tooling partners.
At the ATI Automation booth, Kane’s smaller Grit ST cobot system demonstrated ATI’s weld grinding tool using 3M abrasives.
In the Applied Automation booth, Kane showcased its Grit XL system designed for polishing large objects such as aerospace parts. Kane also performed sanding and finishing tasks using FerRobotics’ end-of-arm tool on the Grit XL’s robotic arm on an automobile hood and on a composite part used in seatbacks for commercial aircraft. The Grit XL system can handle large parts measuring up to 6 feet by 15 feet, Hiken said.
The Grit VM is a third version of the system that holds parts in a vertical orientation, but Kane did not display it at the show, Hiken said.
The Grit systems also can come equipped with vision systems.
“We do two things with vision systems,” Spruce said. “One is we can measure the dimension of a part with a camera, and we can feed those dimensions into our sanding programs, but more importantly, we’ve been developing quality assessment. We can use a camera to take images of a part, and we have machine learning algorithms, AI, look at the different images and determine whether the surface finish is a good or bad finish and whether more sanding needs to occur. We do that through AI and vision.”
Grit cobot systems are reconfigurable for different tasks and, with various sizes, they can accommodate a wide variety of jobs. A Grit system involves an average investment of $150,000, making the systems affordable for even smaller manufacturers, according to the company.
Kane Robotics said its users report a 50 percent to 80 percent improvement in productivity once the robots are installed to supplement manual labor. The cobots also reduce health risks and solve labor shortage issues for small- and medium-sized manufacturers, according to the company.
“There has been an increased demand for cobot solutions,” Hiken told PMM.
It used to be that employers looked at cobots for potential cost savings, but today, a lot of employers report they can’t find employees to perform manual sanding, polishing and deburring tasks, he said.
“Nobody really wants to put on a Tyvek suit, gloves, a respirator and a hood and spend eight hours a day sanding and inhaling dust and other contaminants,” Hiken said. “A lot of customers are looking for robotics to come in and take away some of that dull, dirty, tedious and repetitive work and allow the robot to do that. That’s freeing up their employees to do things that people are better suited to doing — judgment, creativity, applying some of their dexterity skills. We’re advocating an 80-20 rule in which the robot is doing 80 percent of the task and they are assisted by human technicians who do the other 20 percent.”
The cobots, by performing tedious tasks that could cause repetitive motion injuries and respiratory illness in humans, reduce health care costs for employers.
“If you spend a whole career with a grinder or a sander or a deburring tool, in your wrist or your shoulder, you develop repetitive motion injuries,” Spruce said. “It’s obviously painful and debilitating for the technicians, but it’s also expensive for the company. They have a valuable person who’s out of work while they’re rehabilitating, and you have the insurance costs.”
Kane already has deployed its cobots to customers who are removing coating and sanding surfaces for paint preparation or repairs on helicopter rotor blades; polishing fighter jet canopies; sanding primer from machine components; and deburring metal castings.
Contact:
Kane Robotics Inc., Chino, Calif., 909-248-4228, www.kanerobotics.com/
Bruce Geiselman, senior staff reporter
Bruce Geiselman
Senior Staff Reporter Bruce Geiselman covers extrusion, blow molding, additive manufacturing, automation and end markets including automotive and packaging. He also writes features, including In Other Words and Problem Solved, for Plastics Machinery & Manufacturing, Plastics Recycling and The Journal of Blow Molding. He has extensive experience in daily and magazine journalism.
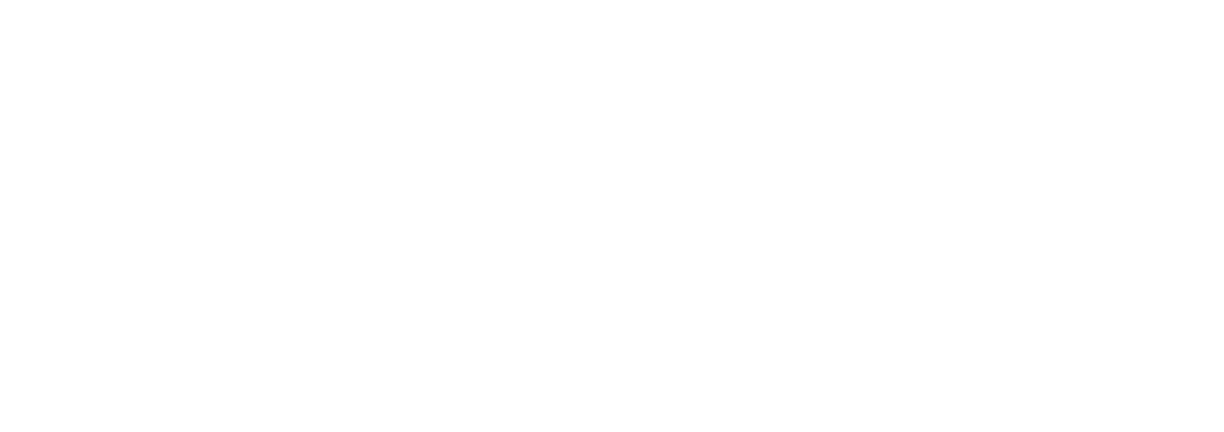