By Karen Hanna
Jobs tied to tens of billions of dollars’ worth of plastics-based goods could find a home in the Rust Belt, according to a nonprofit dedicated to promoting the shale gas resources of Ohio, Pennsylvania and West Virginia.
“Ohio manufacturing operations are well positioned to capture a significant share of the annual $25 billion of imported plastic products,” Shale Crescent USA states in a report released in December 2022.
Related: Supply chain challenges point up advantages of reshoring
Formed in 2016 with support from industry backers, unions, and community and economic development agencies, Shale Crescent USA sees a possible economic boon in manufacturing plastics-based goods in the same region — which it refers to as SCUSA — where resin precursors can be extracted and refined using the controversial method of fracking.
“By attracting manufacturers and ancillary environmental support companies to the region, SCUSA in effect brings operation of the entire supply chain to the center of the country’s largest end market. Shared proximity to raw materials and market has the potential to make Shale Crescent USA one of the most economic and sustainable petrochemical and manufacturing hubs in the world,” the organization’s report states.
Since its founding, Shale Crescent USA has spent over $1 million on research while promoting the viability of made-in-America manufacturing,
“Most of the people alive today, even in management positions, they don’t remember when made-in-the-USA was the norm,” said Greg Kozera, director of marketing for the organization “And we’re in a position to go back there.”
Untapped resources
The oil and gas industry had long eyed the deep reservoirs of natural gas trapped in shale in Ohio, Pennsylvania and West Virginia, but no one knew how to extract them, said Kozera, an industry veteran who once worked for Halliburton.
Starting around 2008, advances in horizontal drilling, as well as the ability to hydraulically fracture individual lines multiple times, have opened new possibilities, and gas production in the region that Shale Crescent USA promotes has blossomed. According to the Shale Crescent USA report, the three states now account for about 35 percent of U.S. natural gas production — compared with just 3 percent in 2010.
If it were a country, the region would rank third — just behind the U.S. and Russia, and ahead of Iran, China and Qatar — in gas production, states the report, titled “Global Economic Factors Align Favoring U.S. Based Plastic Product Manufacturing over China Operation.”
“To put this in perspective, the well-known energy state of Texas has twice the land mass of OH, WV, and PA combined, but produces far less natural gas at roughly 25% of U.S.,” the report states.
Landing new jobs
For manufacturers, the proximity to the precursors of plastics — along with a majority of consumers in the U.S. — presents opportunities. Among those cashing in is Shell Chemical Appalachia LLC, which in November 2022 opened an ethylene cracker plant outside Pittsburgh. According to Shale Crescent USA, it’s just one of five world-scale plants the region could support.
“With great market access, innovative offers and connected infrastructure, Shell Polymers Monaca is well positioned and ready to serve customers with high-quality, competitive products,” said Huibert Vigeveno, Shell downstream director, in a press release.
Ohio — where Shale Crescent USA is headquartered — is within a day’s drive of 50 percent of the U.S. population, accounting for 70 percent of the country’s PE consumption and 77 percent of its PP consumption. Thirty percent of Canada’s population is similarly within reach.
The American Chemistry Council (ACC) estimated in a report in 2017 that a $36 billion investment in gas production in West Virginia, Ohio and Pennsylvania, along with Kentucky, would result in 101,000 jobs, $23.0 billion in chemicals and resins, and $5.4 billion in compounded and manufactured plastics products. In addition to other benefits, the investment also would catalyze $2.9 billion in additional yearly tax revenues.
“This is the only place I can think of on planet Earth where a company can literally build on top of their feedstock, which is the oil and gas, natural gas liquid, underneath,” said Kozera, who believes ACC’s forecast could be conservative. For his guide, he looks to the numbers of manufacturing jobs in the U.S. before the sector declined.
“We lost millions of jobs,” he said. “Are we going to get them all back? No, because some of those jobs, automation is going to eliminate some of those jobs, anyway.”
The Shell plant, which has facilities for an ethylene manufacturing process and three PE manufacturing units, is expected to employ 600 full-time, permanent workers, according to a report prepared by the Robert Morris University School of Business. It will produce 3.5 billion pounds of PE a year.
Predicting success for reshoring
To illustrate the economic potential of U.S. oil and gas deposits, Shale Crescent USA envisioned a match-up between hypothetical manufacturing plants in Ohio and Zhejiang province, China. Ready access to liquid natural gas — a source for both resin and the energy to run the plants that turn resin into parts — is a major advantage, it found.
Milacron provided insights about molding costs to Shale Crescent USA for its study comparing probable manufacturing costs at hypothetical competing plants in Ohio and in Zhejiang province.
“We do support their initiatives, bringing more jobs to the U.S.,” said Brian Miller, senior strategic marketing manager at Milacron LLC, Batavia, Ohio. “That's fantastic. We'd like to do as much as we can to help.”
The report examined the likely costs of producing eight plastics-based goods: eating utensils, children’s booster seats, dust pans, window shutters, pallets, toothbrushes, bulk containers and storage boxes. In some cases, the Ohio plant won out by significant margins.
Bulky and heavy items — which are more expensive to ship — could provide the best margin for domestic manufacturers. But competitive manufacturing costs aren’t the only advantages, according to the study. Other advantages include the potential to innovate more quickly, as well as “reduced emissions, energy efficiency, reduced costs, inventory advantages, and opportunities to develop and expand based on the unique advantage of possessing both world-class supply and demand within the same region,” the report states.
Among the factors behind a trend toward cost parity are the rapidly rising wages of manufacturing workers in China. Over the past 25 years, they have increased more than tenfold, and they’re doubling every six or seven years, according to Shale Crescent USA.
“Labor’s not a big deal anymore,” Kozera said. “I talk to processors, and they say, ‘Well, we can’t compete with China; they’ve got cheap labor.’ So? Doesn’t matter. Two things: Chinese labor costs are going up, and with automation, you don’t need as many people. So, all of a sudden, labor’s a small percentage of the cost. The three things that do cost are energy, raw materials and ocean transportation.”
On those fronts, American manufacturing has advantages.
For example, Shale Crescent USA found that energy costs would run 6.48 cents per kilowatt hour (kWh) in Ohio compared to 10.08 cents per kWh in China to run machinery at the hypothetical plants. More importantly, U.S.-based manufacturers have access to reliable power at prices that are steady and predictable, while Chinese manufacturers cope with unreliable energy sources and fluctuating prices.
With refineries available in the U.S., domestic manufacturers also have an advantage over their counterparts in China, who are forced to rely on imports of more-expensive oil-based naphtha.
Finally, issues involving transportation, which have caused customers of mold makers and manufacturers to consider shortening their supply chains, continue to reverberate.
“Can you imagine what happens to this cell phone case?” Kozera said, gesturing to his phone during a video call. “Probably made in China, but it’s made in China with Middle East oil because they don’t have any, so they get their oil from the Middle East, 7,000 miles to China, and it’s naphtha, so … they pay more for their oil. … And they’re finally creating the polyethylene they need, and then once they make this thing, and they’re making it using coal for an electricity source, which is not the cleanest form in the world, particularly the way they burn it, and then they’re going to ship this thing another 15,000 miles to get to me.”
In addition to costs related to shipping, that transaction causes further harm to the environment, he said, and complicates the supply chain.
According to Shale Crescent USA, ships emit nearly 1 billion tons of carbon dioxide a year — about 2 percent of global energy-related emissions. Every year, the shipment of toothbrushes alone contributes emissions equivalent to what’s put out by 6,200 passenger cars.
In all, making parts in Ohio could reduce the supply chain by 15,000 to 20,000 miles, according to Shale Crescent USA.
“If you want to do something good for the planet, if you want to take a cold shower, that’s great,” Kozera said. “But you can do better than that: Buy American.”
Leveraging location
Kozera looks forward to eliminating some of that waste — while giving hope to communities in the U.S. where manufacturing was gutted.
A father of three adult children who all moved from the region in search of jobs, he said he’s convinced Ohio, Pennsylvania and West Virginia have the makings of a comeback.
“The numbers show that you can make stuff here cheaper than you can in China. And now it’s a matter of companies here believing that and acting upon that. ... I think it’s a matter of people making that decision and believing that, ‘Oh my gosh, we can do this,’ ” he said.
Karen Hanna, senior staff reporter
Karen Hanna | Senior Staff Reporter
Senior Staff Reporter Karen Hanna covers injection molding, molds and tooling, processors, workforce and other topics, and writes features including In Other Words and Problem Solved for Plastics Machinery & Manufacturing, Plastics Recycling and The Journal of Blow Molding. She has more than 15 years of experience in daily and magazine journalism.
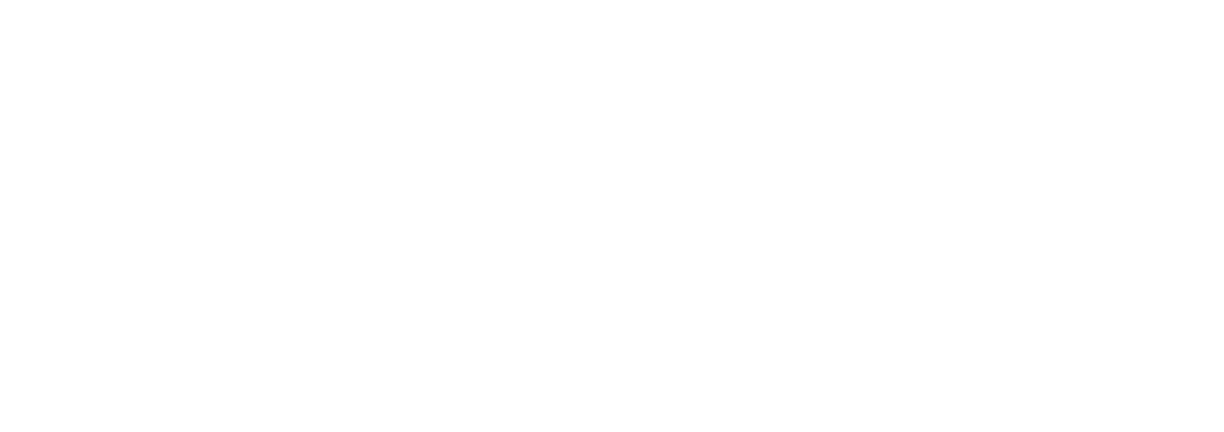