By Karen Hanna
Makers of plastic products for construction — including pipes, siding and insulation — are building into a market that’s growing, despite current economic headwinds, industry watchers say.
At a time when plastics are under fire in some circles as a threat to the environment, proponents see potential. They say builders and buyers willing to embrace plastic over traditional materials, such as wood and metal, could enjoy myriad sustainability advantages.
“It’s durable and sustainable. It’s resilient whenever it comes to ground shifts, earthquakes, floods,” said David Fink, the president of the Plastics Pipe Institute (PPI), the largest North American trade association for such products. “It’s just a better product at the end of the day.”
Whether surveying infrastructure spending or the market for new homes, Fink and other experts said in July they believe construction-project volume has long fallen short of actual need. But spending is increasing — from about $619 billion through the first five months of last year to this year’s January-to-May total of $686.9 billion, according to the U.S. Census Bureau, which will release June figures in this month.
Brisk business
Pipe maker Uponor North America, based in Apple Valley, Minn., is one company that’s enjoying the building boom. Demand for its building products is so high, its own facilities are expanding.
In May, officials snipped pipe to celebrate the opening of a $5.5 million, 25,000-square-foot expansion to the plastic processor’s Hutchinson, Minn., facility.
The company specializes in cross-linked PE pipes, mainly for plumbing, heating, hydronics and cooling systems, as well as residential fire-safety systems, said Kate Olinger, the U.S. company’s director of industry and regulatory affairs.
Of its 1,060 employees in the U.S. and Canada, Olinger said 400 work in Minnesota-based production facilities, using proprietary extrusion equipment from Uponor’s parent company in Finland. In addition to expanding its facilities, Uponor also recently added a full Building Information Management team that creates 3D designs of homes, so they can be built more quickly and sustainably.
The company, she said, is seeing “excessive demand.”
Making the case for plastics
Pawan Thampi is the VP for building products for John Burns Real Estate Consulting, which provides independent research and consulting services related to the U.S. housing industry. He said plastics are well-suited to construction applications, but many contractors are in no hurry to adopt new materials.
“Technological change happens at a glacial pace within homebuilding,” he said.
Given a chance, plastics is a winning material, depending on the application, proponents said. Among other advantages Thampi and others cited, plastic products are tough and light, and require fewer resources to manufacture, install and maintain than products made from other materials, making them cost-effective.
“If people want to look at facts and science, architects and developers and contractors can make decisions that actually reduce the carbon footprint of buildings by the materials they choose, and our products do very well when it comes to that,” Dobson said.
VSI, which represents eight extrusion companies in the U.S. and Canada that together account for more than 90 percent of the two countries’ siding production, is engaged in a couple of sustainability initiatives.
For example, it’s partnering in a pilot project to determine the feasibility of collecting and recycling post-consumer siding tear-offs. Its members also are touting a product that combines siding with insulation — an advancement that meets new regulations in some areas, including New England, for exterior insulation that improves energy efficiency, Dobson said.
Just as VSI is touting plastics for siding, so are Olinger, Fink and others when it comes to sourcing material for pipes. Plastic is resistant to damage from roots and corrosion-proof, so it doesn’t leak, and requires less pumping energy.
As an example of plastics’ resilience, he pointed to disasters that damaged infrastructure without harming pipes. In some cases, floods destroyed buildings, but left still-usable, fused PE water-carrying pipes behind, he said. In Paradise, Calif., the epicenter of a conflagration that killed 85 people in 2018, workers have installed new plastic piping systems.
“It’s because of the resiliency. They can rapidly recover. Because it’s easier to install, they can get the community back up and running faster,” Fink said. “And, again, it’s cost-effective.”
“We really think we have a great story to tell there from a sustainability [and] from a resiliency standpoint, our products last a very long time,” Olinger said. “… It’s easier to work with, easier to install, not as hard on people’s bodies to move around. If you think about carrying a 20-foot stick of steel pipe, that’s a pretty heavy thing to carry around.”
Josh Cottle is VP of sales and marketing for WL Plastics, which presents lunch-and-learn sessions to educate project planners about plastics’ advantages. Employing more than 600 people, the Fort Worth, Texas-basedThe company is working to push for the evolution of standards to allow greater use of recycled plastics. Cottle believes the efforts have huge potential, depending on the application and customers’ acceptance of the materials.
“Today, we can, as an industry, consume hundreds of millions of pounds of recycled polyethylene,” he said.
Almost all pipes for carrying potable water, sewage and natural gas now are made of plastic, but concrete still has the storm-runoff market cornered, with plastics accounting for only about 25 to 30 percent of those pipes, Fink said.
On the other hand, he said, “You look at in-house, [there is] very limited copper usage anymore.”
Pent-up demand
Aging housing stock and infrastructure suggest big demand ahead for makers of plastic products for the construction trades. However, supply chain disruptions and soaring interest rates could hamper the housing market, even as funds from the $1 trillion federal infrastructure bill passed last year begin sending a charge through industrial construction markets.
“Everybody today … is showing good growth,” said Fink, though he acknowledged mortgage rates might cause prospective buyers to pump the brakes on home purchases. “The housing market is slowed a little bit, mainly because of inflation and people are trying to raise interest rates to slow down inflation. You’re still going to need homes, people still need somewhere to live. And ... you have infrastructure in place that needs replaced, that needs rehabilitated. So even without new construction, there is a lot of work that needs to be done for rehabilitation.”
With millennials — the biggest generation since the baby boomers —According to the Census Bureau, seasonally adjusted construction spending totaled more than $1.6 trillion in 2021 — up from $1.5 trillion the previous year. The first five months of spending represented an increase of more than 37 percent over the $498.8 billion spent during the same time frame of 2019 — the last year before the COVID-19 pandemic disrupted the global economy.
The vinyl siding business, for example, has been busy.
“Essentially, we’re producing as fast as we can, but we’re not keeping up with the current demand,” Dobson said.
The Census Bureau’s numbers point to a backlog, with construction for 285,000 single-family homes authorized, but not started, in June. Meanwhile, new projects are slowing down. Building permits for houses in June hit a seasonally adjusted annual rate of 1,685,000 — 0.6 percent below the revised May rate of 1,695,000 but 1.4 percent above the June 2021 rate of 1,661,000.
“Builders, even though they are working on ... a record-high number of units, they’re actually slowing their new permits and new starts way down, basically doing a U-turn in the new-home construction market,” said Eric Finnigan, VP of research and demographics at John Burns Real Estate. “... We actually forecasted a decline by next year.”
Plastic can offset rising costs
Prices bear witness both to demand and to ongoing challenges procuring supplies and materials.
But, Finnigan said, builders aren’t bearing the burden.
“Every single category in the first quarter was up more than 10 percent, so you can also look at the Producer Price Index inputs to residential construction, and that’s been over 20 percent,” he said. “However, builders have been raising their prices to more than offset the increase in materials, and their margins have actually expanded over the last year.”
In some cases, inflation might actually make some building projects or materials more attractive than others. For example, Thampi said, rising energy costs could drive home the importance of energy efficiency. At the same time, rising costs for labor and materials could steer some people to remodel their homes, rather than trade up, Finnigan said.
Adding a deck or patio — often using composite materials — is a common choice, Finnigan said.
Rising prices also help make the case for vinyl, Dobson said, because plastic is a less-expensive material.
“If prices go up, our products are very affordable, especially the base vinyl siding products. They’re resource-efficient, they’re easy to put up,” he said.Falling behind on infrastructure
Regardless of current conditions, Fink said the state of U.S. infrastructure can’t be ignored forever. It’s aging — and fast.
“A lot of your infrastructure was built [during] World War I, World War II. So you’re talking early-1900s, mid-1900s, those pipes have met their usable lifetime; they’re falling apart,” Fink said.
Projects put off for too long could result in a catastrophe, said Fink, who believes the infrastructure spending approved last year is only a start. Eventually, he thinks people will be willing to dish out money to accelerate public projects currently focused on rehabbing just 1 percent or less of available infrastructure a year.
Much more is needed, he said.
“I’ve been glad to see that cities are starting to realize and starting to spend more, but they’re not to the point where they need to be. These cities probably need to be closer to 3 to 5 percent of their infrastructure replacement here in the next 10 to 20 years to really get caught up and provide people the quality of living that we’ve become accustomed to. We’re a First World nation that could turn into a Third World country if you can’t turn on your tap and get drinking water or flush your commode,” Fink said.
Shovel-ready jobs
All that work will require a lot of laborers, but Dobson, Fink and others said the construction and manufacturing industries have a ways to go to meet that need.
“Demand is really strong in our industry today,” said Cottle, at pipe maker WL Plastics, which last year purchased its ninth manufacturing facility. “There’s significant opportunity to do more pipe than we are doing as an industry today. Our biggest constraint, outside of some continued supply chain constraints, is definitely labor, getting enough people into our plants to run our assets safely.”
“We have some plants that are fully staffed. We have some plants that are 50 to 60 percent staffed,” Cottle said. “We have high turnover throughout the company. We get a lot of employees moving around for a little extra down the street here or there, not necessarily looking at the total benefits package that’s available to them at WL Plastics. It’s a challenge.”
With a portfolio that includes pipes measuring as much as 4.5 feet across, WL Plastics can’t automate as easily as other processors, Cottle said.
“Unfortunately, pipe is a little harder to automate. We produce very large products that weigh thousands and thousands of pounds and have a variety of configurations in how we package them; so, it’s not as easy as a robot pulling parts out of an injection molder and dropping them into a box.”
Attractive characteristics
Uponor, too, is struggling to find employees, but Olinger believes the company’s sustainability pitch makes a compelling case. In its 2021 sustainability report, the company touts not only the sturdy reliability of its pipes, but the projects it’s undertaken to help fish and corral plastic waste from escaping into the environment.
It’s a case Fink believes has merit. He hopes potential workers are listening.
“There’s good wages to be had in this industry. And for us as well, one of the things that we’re starting to advertise to the general population is, there’s good career paths within manufacturing. You can start as a line operator, and, if you’re interested and willing to learn, a lot of these manufacturing companies will teach you,” he said.
In construction, plastic is a good bet, Fink said. Among pipe buyers, the transition already has started — the use of plastic is growing more quickly than any other material.
“We’ll continue in my mind to win over the public and the engineering [departments], the end users, the key stakeholders out there that are decision makers, because at the end of the day — and I’m biased obviously — but I believe we’ve got a better product, cost-effective, lower-cost throughout the [value] chain, and something that’s going to last with very little maintenance. So why wouldn’t you take a look at the plastic materials?”
Contact:
John Burns Real Estate Consulting LLC, www.realestateconsulting.com
Plastics Pipe Institute, Irving, Texas, 469-499-1044, www.plasticpipe.org
Vinyl Siding Institute Inc., Alexandria, Va., www.vinylsiding.org
Karen Hanna, senior staff reporter
Karen Hanna | Senior Staff Reporter
Senior Staff Reporter Karen Hanna covers injection molding, molds and tooling, processors, workforce and other topics, and writes features including In Other Words and Problem Solved for Plastics Machinery & Manufacturing, Plastics Recycling and The Journal of Blow Molding. She has more than 15 years of experience in daily and magazine journalism.
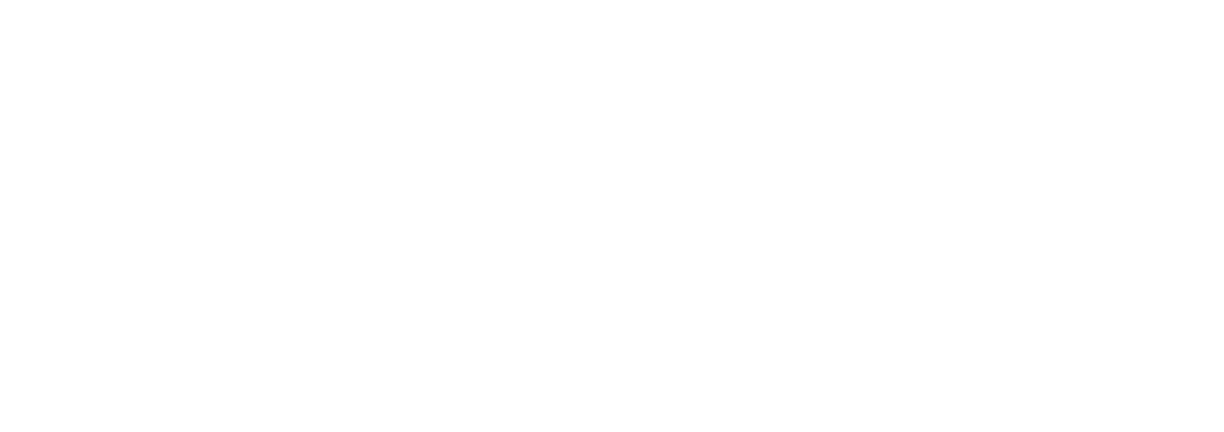