By Reed Dailey and Jim Maurer
CohnReznick
As they navigate the current supply chain shortages, labor constraints, geopolitical issues, and rising material costs, companies in the plastics sector are also managing extremely high demand for their products. To deal with the related capacity issues, improve forecasting, and reduce machine downtime, many of them are using predictive analytics to not only help them manage their shop floors, but also their end-to-end supply chains.
Using statistical modeling to make forecasts about future outcomes and performance, predictive analytics factors in both current and historical data patterns. It determines whether those patterns are likely to re-emerge, thus allowing manufacturers to adjust their resources in order to take advantage of possible future events, improve operational efficiencies, and avoid risk.
With CohnReznick’s recent Manufacturing Checkup survey revealing that two-thirds of manufacturers import more than 25 percent of their components and materials — a number that’s expected to remain steady over the next two years — the need for better analytics is clear.
Managing in a perfect storm
In 2022, many operators are still using paper, spreadsheets, and phone calls to share information on the plant floor, with other departments, and outside suppliers. These manual processes require more significant effort and consume more time to complete.
Furthermore, iInconsistency and blunders are more likely due to user error, not to mention that recognizing trends and pinpointing issues are subject to the individual operator.
To make matters worse, many manufacturers don’t have backup or redundant suppliers for a high percentage of their primary suppliers. This forces companies into a reactionary position, increases risk, and impedes continuous improvement right at a time when plastics manufacturers are grappling with a “perfect storm” of business challenges.
Developing a roadmap for success
Plastics companies that want to shift away from operating in a reactionary mode, and start operating more strategically and proactively, can use predictive analytics to transition their approach by putting data and analytics programs in place to make decisions. Once in place, the technology helps companies improve their processes, enhance real-time decision-making, manage capacity issues and do more with less.
Already tried and tested across many industry sectors, predictive analytics drives efficiency on the plant floor and allows companies to convert collected data into tangible, relevant actions.
Adopting predictive analytics can be daunting for the manufacturer that’s using older machinery, software and hardware that don’t “talk” to each other, but there are some key steps that companies can take to get started down the right path.
Here are five strategies that all manufacturers can use to begin leveraging predictive analytics to optimize plant floor performance:
Step 1: Assess your current status. Start by taking stock of your current operations, capabilities, resources, and technology. Identify the current or potential gaps, including any existing equipment that doesn’t support activities like automated data capture (ADC). This is the delineation for most equipment in use on the plant floor, where machines that can’t capture data also can’t share information with one another (and, with key stakeholders). When operational information isn’t readily available, companies are forced to base any plant floor optimization decisions on weekly or monthly reports — neither of which are fast enough in today’s business environment. This reality came to light during the early stages of the pandemic, when companies’ historical demand sensing and forecasting quickly led to major supply chain shortages.
Step 2: Make the necessary equipment changes. Once you’ve assessed your company’s position on the technology maturity curve and mapped out any weak areas, you can then add the appropriate processes or equipment needed to manage data capture. How you approach this step will largely depend on your current plant floor setup, data gaps, and requirements. In some cases, you may be able to go back to the OEMs and purchase add-ons that will allow you to capture different activities and then present those outputs. In other situations, a third-party manufacturer may supply “bolt-on” equipment that allows your existing machines to generate data. The latter may require an employee to use a device like a scan gun to capture the information, but the outputs will still provide valuable insights that you can use to optimize plant floor performance.
Step 3: Build out your own analytics and reporting capabilities. The best way to turn your data into action is by building out your own analytics and reporting capabilities. You can start small with a subset of data that’s most relevant to your shop floor (e.g., product quality, labor efficiency, energy consumption, machine utilization, etc.) and then build out from there. For most companies, the data will be generated by the equipment itself using ADC, and then it will flow directly into the enterprise resource planning (ERP) platform or other primary source of record. You’ll probably also have other points of record, such as human resources data that you can pull from a time clock or human resource information system (HRIS). From there, you’ll take data and feed it into a unified dashboard/enterprise visualization solution. In most cases, 75 percent of the data that you need will come right out of the ERP, with the remainder likely coming from your human capital management solution, sales engine, and any ancillary data outputs from facility monitoring equipment.
Step 4: Make business decisions based on analytics. You’ve probably already heard that “data is the new oil,” and nowhere is this more relevant than on a busy plant floor. The problem is that companies tend to fixate on single data points for six to 12 months at a time without looking at the bigger picture. They’ll continue to review the key data points, prove or disprove their hypothesis, and take corrective action within a certain time frame. This is an expensive approach, and particularly when it comes to adjusting either from a process or equipment perspective. By the time you get to the report, you’re worn out from project fatigue and cost. A better approach is to start small with a few dashboards, look at the leading indicators, and then adjust accordingly.
Step 5: Commit to continuous improvement. A model rooted in the idea that companies must make incremental improvements to processes to achieve their overall goals, continuous improvement helps manufacturers to break out of a “set it and forget it” mode. It also helps them fully leverage predictive analytics to optimize their plant floors. When asked about operational programs at an organization, only 44 percent of respondents to CohnReznick’s survey stated they have a continuous improvement program. Companies that adopt a back-to-basics approach are coming out ahead of the pack. By assessing where they are, making the necessary equipment changes, building out their analytics and reporting, making good decisions, and then repeating the process, companies that continually reassess and readjust can position themselves as more versatile, agile and risk averse than their competitors are. The key is to focus on incremental, ongoing changes versus a massive, transformative approach to predictive analytics. When you can test out new theories, systems, and hypotheses over a period of time, and then make the tweaks and adjustments, the incremental improvements will begin to add up quickly.
Ready, set, go
Predicting future risks, finding new ways to improve operations, and increasing profitability have all become more difficult over the last few years. Manufacturers throttled by manual systems and spreadsheets are realizing the power of predictive analytics on their plant floors, where simply adding more labor to the problem is no longer an option.
The labor market isn’t returning to pre-pandemic levels anytime soon (if ever). This reality is pushing companies to use their data to better understand and evaluate complex plant floor systems and processes, anticipate what will happen next, and make good decisions based on all that information.
By merging historical data with artificial intelligence, machine learning and the Internet of Things, predictive analytics helps manufacturers better understand, monitor, and optimize their plant floor processes. By following the roadmap outlined in this article, companies can begin analyzing real-time process data, predict potential issues and get recommendations that they can turn around and use to prevent problems, improve processes, and maximize performance.
Reed Dailey is a director in CohnReznick’s Technology+ group, where he advises clients on how to leverage digital technology to maximize operational effectiveness, reduce time to market and achieve organizational goals. He has assisted organizations across manufacturing, distribution, and field services in their digital transformation “go-digital.”
About CohnReznick
As a leading advisory, assurance and tax firm, CohnReznick helps forward-thinking organizations achieve their vision by optimizing performance, maximizing value, and managing risk. Our manufacturing and distribution clients benefit from the right team with the right capabilities; proven processes customized to their individual needs; and leaders with vital industry knowledge and relationships. Headquartered in New York, N.Y., with offices nationwide, the firm serves organizations around the world through its global subsidiaries and membership in Nexia International. For more information, visit www.cohnreznick.com.
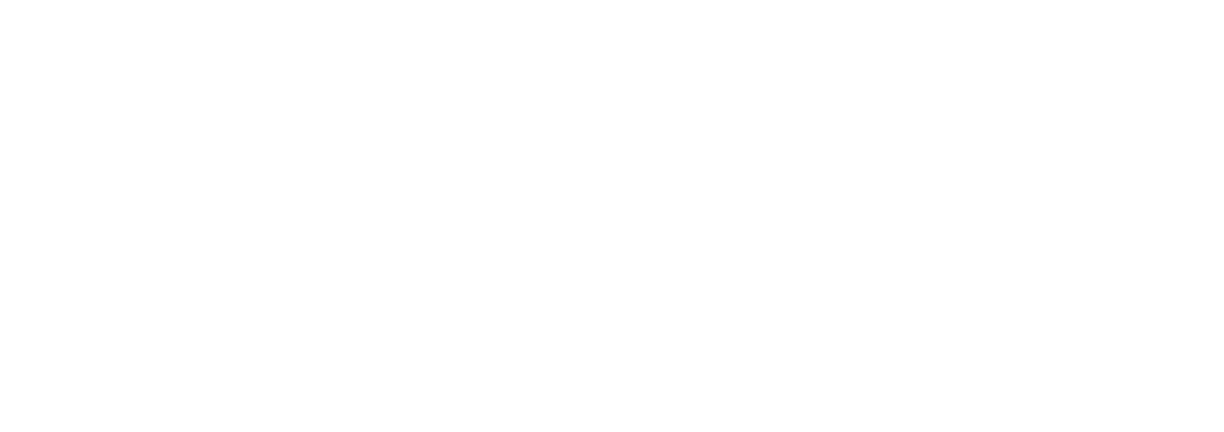