By Karen Hanna
At the automotive factory behind Key Manufacturing LLC in Madison, Ind., workers with attendance issues are fired one day, hired back the next.
At least that’s the impression of Key GM Anthony Neeley. The 34-year manufacturing veteran says the labor market has never been tighter — it is one of the reasons why the company has gone from one robot to seven over his four-year tenure.
"We’re picking the parts out of the press with the robot, laying them on conveyors, indexing the conveyor. … We’ve taken processes that used to go through a WIP process, which is work-in-progress. We would load it, send it to WIP, bring it back, put it in an assembly. ... We’ve automated some jobs like that, where we took the WIP completely out, freed up warehouse space. … It’s all about getting lean,” Neeley said.
Key’s automation investment mirrors the binge taking place throughout the plastics industry. Representatives of robot makers and integrators draw from lists of superlatives to describe demand, with words like “fantastic,” “unimaginable” and “crazy.”
Just how good are things for robot sellers?
For the first time, Robbie Devlin, president of robot and automation integrator DevLinks, said robot users are stocking up, hedging their bets amid long lead times as supply chain problems drag on.
“We’ve actually had customers who ordered robots, have put deposits on robots, and they don’t know what projects they are going to use them on ... just so we can get robots on order and get them in the pipeline,” he said. “... I believe that the demand for robotics has gone up 200 percent or maybe more during the pandemic.”
Automation prioritization
According to robot suppliers, processors are adopting more automation, with more advanced technologies. Some are catching up; others are probing the frontiers of automation, moving into automating applications that, until recently, most plants were tackling by hand. In other instances, ever-more-sophisticated parts have required investment in automation to match.
“We see that the classical injection molding process is being pushed into the background, and that the [work] cell automation itself is becoming more and more important, because customers need ... to optimize more and more process steps in their production,” said Deborah Lidauer, product manager for automation for Engel.
Automation has become top of mind for blow molders planning a cell, said Siva Krish, VP of sales for Proco Machinery Inc.
“Whenever a project comes into the picture, the first thing they think about it is automation.”
For Mike Ingles, a consultant who works with automation integrator Applied Manufacturing Technologies (AMT), the technologies’ appeal is obvious.
While AMT is an integrator of Fanuc robots, Ingles said he is not tied to any robot or particular solution. Having worked with automation since 1985, he has been around long enough to help open his clients’ eyes to the growing possibilities.
“It’s so sophisticated, even the horrible robots are still wonderful. It’s what you put on the robot, and the secondary processes, the welding, the material handling, the dispensing, those type of things are what really make or break the system, not the robot itself,” Ingles said.
“The key point is [it is] easier to use, easier to program, easier to install, easier to connect different parts of the machine and the automation together,” said Nigel Smith, president of TM Robotics (Americas), an integrator of Shibaura injection molding machines (IMMs) and robots formerly branded for decades under the name Toshiba.
Help wanted
With 856,000 job openings in the manufacturing industry in December, plastics processors have had plenty of room on the line for robots.
“If you talk to any injection molder or any plastics processor, and you say, ‘What are your plans for capital investment, or what are you going to do for continuous improvement?’ The first thing they say is, ‘Automation,’ ” said Chris Parrillo, national sales manager for Yushin America.
Robot maker and integrator Absolute Robot Inc. (ARI) used to supply 60 or 70 robots a year; it is now up to 150 or 200, business unit manager Tim Lavigne said.
“If you’ve only got one person showing up to work every day, rather than having that one person stuck at one mold, or one press, pulling parts from one mold, if you’ve got robots on all six of your machines, that one person can monitor as all six of them run,” he said.
Persuaded by improving technologies, easy-to-use interfaces and relatively attractive prices, plastics processors that initially countered the labor shortage by “dipping their toes in the water,” have moved from tepid adoption to taking the full plunge, Lavigne said.
“ ‘We’ll try one [robot],’ turned into two, turned into, ‘We need eight of them as quick as you can get them because we want to put one on every machine now.’ ”
Supply chain woes
High demand comes amid festering problems along the supply chain. Most OEMs reported that they are able to supply robots at the same time they install IMMs — but the IMMs themselves are delayed.
“For some robot types, it is prolonged, indeed … but it still matches the delivery time of the machine,” Engel’s Lidauer said.
One culprit is the limited availability of computer chips, which has locked up the delivery of many kinds of products with electronic innards, Proco’s Krish said. The company works as a robot integrator for packing line automation, including Yaskawa Motoman robots and cobots, to bottle makers.
“There’s a shortage on the customer side, on the manpower; there’s a shortage on supplier side, too. So, the electronic shortage is kind of hitting a little bit on every supply chain,” he said.
Sometimes, customers themselves end up shelving projects because their orders or material availability have been affected, said TM Robotics’ Smith.
Because multiple projects can come to a head at once, Krish said lead times “are always a bit challenging.”
To keep up, Lavigne said he is looking over ARI’s robot inventory about every month, rather than the three-month cycle he used to maintain.
For Boy Machines, pre-pandemic delivery times were three or four months, company President Marko Koorneef said.
“It’s a struggle every day. Every day, it’s a struggle to try to get the parts in, to get the machines finished, to get them out the door. So, it’s really hard.”
First impressions
For processors like Key, a part of MANAR Inc., Edinburgh, Ind., finding labor has been a pressing challenge. As of late February, the plant, which has about 70 employees, had a couple of open positions.
But when he started at Key, Neeley was taking on other concerns.
In an effort to make a better impression on customers and prospective customers, Neeley’s overseen the robot acquisitions — as well as projects to renovate the company’s lobby and repave its parking lot, which was in rough shape.
The plant runs one three-axis robot and five five-axis robots on a collection of 14 IMMs with clamping forces ranging from about 55 tons to 1,100 tons; in addition, it has a Universal Robots cobot that performs post-processing functions, such as drilling and trimming parts.
New on the job
Like Key, many manufacturers are just getting started; others are moving to automate applications further downstream.
“We’re seeing a bigger uptake for customers that used to not use robots at all,” said Jason Long, Wittmann’s national sales manager for robots and automation.
Before the current boom, about half of Wittmann’s sales of new injection molding machines also involved automation, including assembly stations, bowl feeders, robots for insert molding and conveyors, Long said. Now, customers are marrying up IMMs with those systems about 75 to 80 percent of the time.
Processors also are making upgrades.
“We find that the folks that maybe had the pneumatic sprue pickers, very entry-level pneumatic robots or hybrid robots that were somewhat limited, those folks seem to be upgrading now to servo robots and three-axis Cartesian robots with a [numerical-control]-servo wrist added on to give the robot higher degrees of motion, more flexibility,” Yushin’s Parrillo said.
Those technologies allow them to complete tasks at the machine that previously happened downstream, he said. Instead of a robot placing parts on a conveyor that carried them to a separate, downstream area for packaging, palletizing or assembly, all those applications are taking place in the same cell.
“Phenomenal” strides in vision systems have made possible the consolidation of some tasks, Lavigne observed.
He cited an insert-molding process performed by robots set up by ARI.
“The inserts are on the insert table. We’re making sure that from the insert table to the mold, they’ve been placed in properly, they’re all still there. And then even when you come out and do your part inspection, you’re still able to have enough time to look at the finished part and say, ‘Yep, they’re all seated properly, they’re not sticking up weird or anything like that.”
Muller Technology also is experiencing surging demand.
According to Taras Konowal, director of sales, the company’s equipment can eliminate hours of work on batches of products as they can be packed and stacked with no human involvement.
“Probably 90 percent of what’s going through our shop is automated case packing,” he said — a big increase over levels before the pandemic.
But demand for other automation hasn’t come down. The company’s M-line take-out robots, for example, also are a very hot item. Introduced shortly before the pandemic began, the robots can be paired with IMMs with clamping forces ranging from 300 to 1,200 tons and single-face, three-level, four-level and stack molds with any number of cavities.
Meeting the skills gap
With robots taking over the workplace, the need for people remains — though the skills they will employ are changing. The automation that companies can adopt is limited to the equipment its staff can manage, operate and maintain, integrators say. But an emphasis on ease of use should make the transition smoother.
Automation could even provide opportunities for workers to expand beyond tasks that might be tedious, tiring or dangerous.
“The more robots and automation they put in and they do, they are going to need a higher skill set of people, whether it’s engineers or technicians to program that equipment and keep it up and running,” Parrillo said.
With workers exposed to new technology, some will have opportunities to move out of their current roles, said Marc Sansour, robotic sales specialist for the eastern Canada territory for Omron. He believes an understanding of safety, programming and proper operation is paramount.
Because of burgeoning demand, companies might even hire based on attitude and interest, rather than experience, with the offer to teach newbies what they need to know. Sansour believes those kinds of opportunities just might be enough to stanch some of the flow of workers who take jobs, then leave them only a short while later.
“They’re going to say, ‘Oh, I’m going into that company. I don’t necessarily have the skill sets. I have the attitude that’s needed. And they’re willing to invest in training for me,’ ” he said. “What you’re doing now is, instead of hiring someone to do a tedious, repeatable task that they’re going to end up leaving after three months, you’re creating loyalty with your employees.”
Return on investment
As the labor shortage dragged on, in a Feb. 14 interview, DevLinks integrator Devlin quipped that demand for his services is so high, customers “are kind of reserving us — like you would a restaurant for Valentine’s Day.”
With labor so scarce, return-on-investment calculations about automation have changed, he and others said. The true cost isn’t for labor or technology — it is lost opportunity, he said.
“It’s almost like regardless of how much it costs ... robots, automation has to happen for them to stay competitive,” said Wittmann’s Long.
That mindset, coupled with the need to make better use of smaller staffs, can help explain the growing popularity of technologies that aren’t even directly related to production. An autonomous mobile robot, for example, can’t make parts — but it might be able to free up time and energy for the people who tend the machines that do.
Over about the past six years, Sansour said customers’ notions of what automation can do for them is changing.
“The AMR is not going to generate that 1,000 parts per hour, but it’s going to help you get there faster.” he said.
That need makes it a good time for selling robots, experts said.
But the future burns even brighter, said Lavigne, of ARI, which has been around about nine years.
“Whatever is going to be the big hurdle nine years from now, I’m sure what’s a big hurdle to me now is going to seem easier. Now, it’s the sort of thing that I can’t wrap my mind around it, but it will be impressive.”
Karen Hanna, senior staff reporter
Contact:
Absolute Robot Inc., Worcester, Mass., 508-792-4305, www.absoluterobot.com
Applied Manufacturing Technologies, Orion Township, Mich., 248-409-2000, www.appliedmfg.com
Boy Machines Inc., Exton, Pa., 610-363- 9121, www.boymachines.com
DevLinks Ltd., Arlington Heights, Ill., 847-749-0429, www.devlinksltd.com
Engel Machinery Inc., York, Pa., 717-764-6818, www.engelglobal.com
Muller Technology CO Inc., Fort Collins, Colo., 970-229-9500, www.muller-technology.com
Omron Automation Americas, Hoffman Estates, Ill., 800-556-6766, automation.omron.com
Proco Machinery Inc., Mississauga, Ontario, 905-602-6066, www.procomachinery.com
TM Robotics (Americas) Inc., Elk Grove Village, Ill., 847-709-7308, www.tmrobotics.com
Wittmann Battenfeld Inc., Torrington, Conn., 860-496-9603, www.wittmann-group.com
Yushin America Inc., Cranston R.I., 401-463-1800, www.yushinamerica.com
More on automation
Automation is on every manufacturer’s mind these days, or it should be. There’s more to our Cover Story:
• Worker shortage, advancements in technology fuel cobot sales. https://plasticsmachinerymanufacturing.com/21257916
• Veteran manufacturer of EAOT says automation is now accessible to anyone. https://plasticsmachinerymanufacturing.com/21256653
• A project manager or integrator can help make your robot installation a success. https://plasticsmachinerymanufacturing.com/21258310
• The future is automated, according to Jeff Burnstein, president of the Association for Advancing Automation. https://plasticsmachinerymanufacturing.com/21256667
• Robots don’t kill jobs; they free humans to move into better ones, experts say. https://plasticsmachinerymanufacturing.com/21258504
• A cobot industry analyst predicts strong growth will continue. https://plasticsmachinerymanufacturing.com/21258134
• Rapid Robotics’ subscriptions offer an affordable way to start automating your plant. https://plasticsmachinerymanufacturing.com/21258285
• Yaskawa enhances features on two new products. https://plasticsmachinerymanufacturing.com/21256712
• Epson’s easy programming lowers the barrier to entry. https://plasticsmachinerymanufacturing.com/21258503
• Three case studies show cobots’ versatility. https://plasticsmachinerymanufacturing.com/21258453
Karen Hanna | Senior Staff Reporter
Senior Staff Reporter Karen Hanna covers injection molding, molds and tooling, processors, workforce and other topics, and writes features including In Other Words and Problem Solved for Plastics Machinery & Manufacturing, Plastics Recycling and The Journal of Blow Molding. She has more than 15 years of experience in daily and magazine journalism.
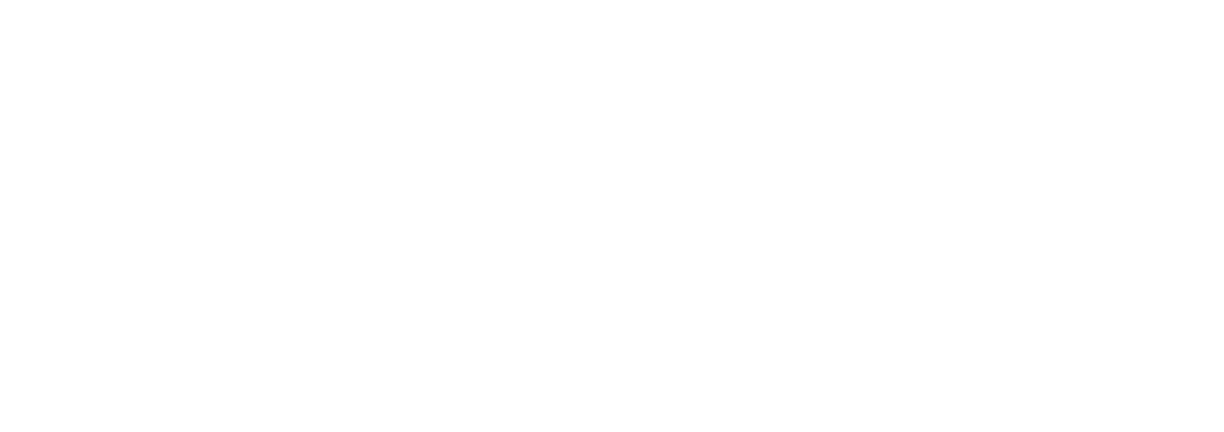