By Karen Hanna
A vessel holding enough water to fill about a dozen waterbeds could be buried beneath the parking lot outside your local strip mall. Gargantuan injection molding machines (IMMs) bigger than the ones that might have made it have begun turning out more.
In February, Engel announced it had shipped two 8,200-ton IMMs — the biggest it’s ever built at its St. Valentin, Austria, plant — to Advanced Drainage Systems (ADS) Inc. subsidiary Infiltrator Water Technologies, Winchester, Ky., to manufacture huge half-pipes, called StormTech chambers, used to encircle underground reservoirs.
An injection molding and extrusion processor, ADS manufactures products that are involved in the entire water cycle, including products for stormwater and septic systems.
“If you've looked at the environment and the weather lately, things are changing,” King said. “And, so, making sure that you manage stormwater, to make sure that your quality of life where you live, work and play is good, we think we do good work in that space.”
ADS’ portfolio includes seven sizes of StormTech chambers. At 83.4 inches by 100 inches by 60 inches, or almost 290 cubic feet, the StormTech MC-7200 is the biggest. It has a minimum installed storage capacity of 267 cubic feet — about 2,000 gallons of water.
A queen-sized waterbed can hold around 200 gallons. Meanwhile, an OlympiThe chambers look like giant Pringles potato chips, King said. Installed in the ground arch facing up, they’re similar in structure to the famous catacombs of Paris.
Beneath the chambers, builders install a geotextile to keep water from seeping into the ground; the chambers are bookended by end caps, also made by ADS. The water then is pumped to a treatment center, so that it can be reused.
Builders involved with commercial and infrastructure projects, such as work at shopping malls, college campuses, airports and distribution centers, use the chambers to manage water runoff without devoting space to above-ground water features.
“When you're operating in an area of the country where land values are quite high, the last thing you want to do is have to lose 3 or 4 acres of your couple-hundred-thousand or half-million-square-foot warehouse to a retention pond,” King said. “And, so, you put our product underneath the parking lot.”
Making the chambers requires huge machines. The new IMMs are two-shot duo 130000/130000H/8200 combi machines that measure 96 feet by 37 feet. Each is capable of a total shot weight of 270 pounds.
They can complete a dry cycle in 16,7 seconds, according to Engel,.
The IMMs are bigger than the three machines that previously made the massive StormTech chambers, which themselves had clamping forces in excess of 6,000 tons, King said. Built in-house by ADS, the earlier machines still are in operation.
“It is the new capabilities and opportunities for continued product development that is truly exciting. This new equipment will allow us to continue to bring new and innovative products to market and meet and exceed our customers’ needs,” said Bryan Coppes, VP of engineering and R&D at Infiltrator.
The new machines are more efficient and boast faster cycle times than their smaller predecessors, King said.
Purchased in November 2020, the first of the new presses arrived in February 2022; parts of the second IMM began arriving in November 2022.
For Engel and ADS, moving and installing the equipment was a big undertaking.
“You can imagine the special shipping and ground transportation arrangements needed to move the machine from Austria to the U.S.,” said Jim Moran, business development manager at Engel North America. “The platens were transported to and from the St. Valentin manufacturing facility along the Danube River on barges. Each machine was fully assembled and tested prior to shipping and then disassembled to be shipped to the U.S.”
The process took two months, as 29 truckloads of parts trekked the nearly 5,000 miles from St. Valentin to Winchester, where ADS had built a new 59,000-square-foot facility with a roof towering more than 66 feet above the ground., to accommodate overhead gantries and cranes.
The plant also has custom robots to handle the vessels it makes.
“Obviously, safety is key when you're making parts this size, and so we use a lot of automation to get [the parts] out of the actual press,” King said.
With double-digit growth over the past few years, ADS is banking on continued investment in the residential, commercial and public infrastructure sectors.
“If you look at our sales over the last few years only, we're now over $3 billion. A couple years ago, we were just under 2,” King said.
King noted the country has undergone a recent building boom, and, while rising interest rates and concerns over the economy could slow residential and commercial investment, the federal government’s $1 billion 2021 infrastructure law likely will spur construction.
The law still is rolling out, so its effects largely have yet to reverberate.
“Obviously, the infrastructure bill that's been passed, we expect that there's going to be more investment in infrastructure, and most infrastructure at some level requires you to manage your stormwater,” King said.
ADS also sees potential in the gradual acceptance of the incorporation of plastic in products traditionally made from other materials, such as metal and concrete. Currently, the company, has a 30 percent market share in the stormwater pipe market.
Skepticism over plastics’ use in infrastructure products means material conversion is slow. In applications in which plastic has been accepted, such as the StormTech chambers, which are made from PP, building codes specify only virgin resin is allowed, King said.
Even so, along with being the largest manufacturer of corrugated plastic pipes in the U.S., ADS is the country’s largest recycler, reprocessing more than 600 million pounds of material in its products in the 2022 fiscal year.
Because many of its products are large and costly to transport, the company operates facilities across the country, to be close to centers of demand. It has about 3,000 employees and 70 manufacturing plants across the U.S.
“A lot of the products that we make, including what we bought those presses to make, those big chambers, they don't ship that efficiently, and, so, you have to make sure that your product is close to where it's going to be used,” King said.
The StormTech chambers, though, aren’t the only mega parts Engel’s prepared to tackle. The company has more than three decades of experience in supplying humungous machines.
With demand for huge machines growing, the company said in a press release it can supply IMMs with clamping forces that top 10,000 tons. They can process about 2.2 tons of material an hour and have injection units capable of producing individual shots weighing several hundred pounds each.
Karen Hanna, senior staff reporter
Contact:
Engel Machinery Inc., York, Pa., 717-764-6818, www.engelglobal.com
Karen Hanna | Senior Staff Reporter
Senior Staff Reporter Karen Hanna covers injection molding, molds and tooling, processors, workforce and other topics, and writes features including In Other Words and Problem Solved for Plastics Machinery & Manufacturing, Plastics Recycling and The Journal of Blow Molding. She has more than 15 years of experience in daily and magazine journalism.
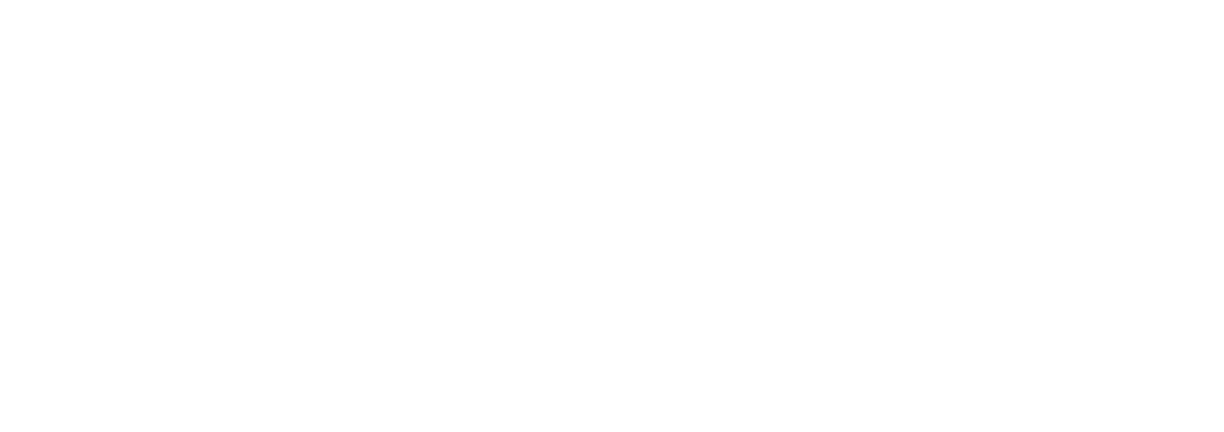