Standardization, falling costs make smart factory technology more accessible
By Bruce Geiselman
Smart manufacturing isn’t a new concept. It’s been around for decades, but recent developments are making it more feasible for small and medium-sized plastics processors.
Declining technology costs, coupled with the adoption of standardized communications protocols are making smart factory technology more accessible, said Stephen Laaper, a principal at Deloitte Consulting LLP, which provides consulting services to businesses in a variety of industries, including plastics. Laaper is a manufacturing strategy and smart operations leader in his company’s Supply Chain & Network Operations practice.
While newer equipment often is Industry 4.0-ready, older equipment might not be compatible. In those cases, adding sensors might allow processors to adopt at least some smart manufacturing strategies without huge investments. And when buying new equipment, processors should ensure that OEMs allow access to machine data.
Deloitte is helping smaller manufacturers develop smart factory capabilities.
In an email interview, Laaper discussed those efforts and the status of smart manufacturing.
For years, there has been a lot of buzz about smart factory technology, but it has seemed to be more a concept than a reality. What is smart factory technology, and where do you think it is headed?
Laaper: It’s really an evolution that started decades ago through the application of technology and automation to control and optimize manufacturing processes. For example, IoT [internet of things] is not new. We’ve been using data from assets and processes to drive decision making for a very long time.
Importantly, cloud [computing] continues to play a bigger and bigger role in smart factory with edge-to-cloud architectures rapidly being adopted.
Edge-to-cloud is a technology architecture that leverages the advantage of on-premises computing, which has been done for decades (on-site servers, for example), with the advantages offered by cloud computing. Edge-to-cloud enables computing close to where decisions are made with a recognition that not all data needs to be pushed to the cloud. A proper edge-to-cloud architecture adds resilience in the sense that production can continue with processing at the “edge” in the unfortunate situation that connectivity is lost between the manufacturing site and the cloud service provider.
How can plastics processors benefit from smart factory technology?
Laaper: Manufacturers producing plastic products have numerous opportunities to use smart factory capabilities to improve productivity.
Manufacturers can start small with a particular use case, say blend control, to ensure that the amount of virgin-to-regrind consumption is optimal to yield increased throughput and reduced raw material costs.
Another significant opportunity is mobility, which allows material handlers, operators, supervisors and maintenance technicians to have greatly enhanced visibility into the operations without being tethered to their desks, resulting in increased spans of control.
Is smart factory technology available today to plastics processors? Are OEMs making their equipment compatible?
Laaper: Given the age of many assets, there are myriad challenges and opportunities to make these assets smarter.
For older assets, the most likely solution is to use secondary sensors to address a particular use case — say vibration or temperature monitoring. Otherwise, the controller, often proprietary, must be replaced at considerable expense.
There have been challenges with OEMs not allowing data to be extracted from the assets due to concerns about impacts to production, or the OEM’s desire to potentially monetize the data. Manufacturers need to ensure when ordering new equipment that access to data is permitted, or work with their OEMs to provide access.
Smart factory, smart manufacturing, Industry 4.0 are frequently used terms — are they the same thing?
Laaper: Many of the terms, such as smart factory and Industry 4.0, have emanated from specific regions of the world or even industries. For example, Industry 4.0 emanated from Europe to highlight that we are in the fourth industrial revolution. Smart factory, smart plant, smart operations, advanced manufacturing, etc., are generally synonymous.
A lot of plastics processors are relatively small. Is smart factory technology available only for large-scale manufacturers or is it suitable for small manufacturers, too?
Laaper: Early adopters in this industry have traditionally been the larger manufacturers as they tended to have older and “less intelligent” assets along with more resources to invest.
However, with continuing advances in technology, along with decreasing costs, the opportunities for smart factory in smaller manufacturers [are] much more achievable. For example, using subscription-based consumption models for smart factory software (such as Deloitte’s Smart Factory Fabric) greatly reduces the amount of capital required to deploy smart factory capabilities.
Who can smaller manufacturers turn to for help with adopting smart factory technology?
Laaper: The market is very fragmented, and smart factory often requires an ecosystem which can be hard for a smaller manufacturer to navigate.
Many smaller manufacturers already work with “mom-and-pop” system integrators that are evolving their services and capabilities.
At Deloitte, we’re developing smart factory capabilities that can be easily adopted by smaller manufacturers and orchestrating the required ecosystem.
What impact has the pandemic had on the adoption of smart manufacturing?
Laaper: As you can imagine, some companies really cut back on their investments due to the overall uncertainty from the pandemic.
However, many companies have used the opportunity to double down on their smart factory investments, realizing the opportunity to invest for the future.
Other companies have continued to invest in smart factory to respond to dramatic swings in demand, or in industries heavily reliant on manual labor (such as meat processing).
There’s also the move to “reshore” manufacturing, particularly in the pharmaceutical, medical device and PPE markets, which will drive smart factory investments in both new and existing production facilities.
We hear a lot about labor shortages. Can smart manufacturing help companies overcome those shortages?
Laaper: As mentioned previously, smart factory provides opportunities to increase spans of control across a plant through actionable insights delivered to the right person at the right time. This results in needing fewer people to produce the same or greater amounts of products.
The same holds true for the maintenance team. Being able to anticipate or predict maintenance needs prior to failure results in fewer catastrophic events.
There are also automation opportunities for numerous processes across the value stream. For example, end-of-line automated packers can augment or even replace personnel required on the lines performing mundane tasks.
It seems like plastics processors have been slow to adopt smart manufacturing. Is that accurate?
Laaper: Our observation is that most industries feel like they are the slowest adopters of smart factory capabilities when, in reality, there are leaders and laggards in every industry.
This perception could be a lack of awareness of what’s happening organically in plants, but since there’s often not a vision and roadmap across the enterprise, many companies are doing “random acts of digital,” which leads to waste.
Are 3-D printers better suited to smart manufacturing technology, and if so, why?
Laaper: This really depends on the product being produced. Certainly, 3-D printing can produce plastic parts, but if a manufacturer is producing high volumes of the same part, then the economics of 3-D printing often do not work.
For example, a company producing thousands of the same parts every day would be much better suited to using more traditional extrusion and injection molding machines.
However, 3-D printing would be immensely valuable in situations when the investment in tooling can’t be amortized across the number of parts produced or there is a short lead time for a part.
This could be for a part that needs to be fabricated and will be produced in a small lot size (even a lot size of one), or there isn’t sufficient lead time to design, fabricate and install a new tool.
What additional information might help our readers better understand the potential of smart manufacturing?
Laaper: Although there is a tremendous focus on technology with smart factory, manufacturers shouldn’t lose sight of the human component. Transformation of the workforce through new skills and thinking to move from being reactive to proactive shouldn’t be overlooked.
Smart factory capabilities should augment lean thinking and continuous improvement initiatives to drive step-change performance improvements versus more traditional incremental improvements.
Cybersecurity should be a consideration from the beginning of any smart factory transformation.
Manufacturers should start with a common vision for smart factory and align investments and use cases to the vision. Otherwise, random acts of digital could occur and investments [could be] wasted.
Companies should understand that there are numerous federal, state, and local tax incentives to help offset smart factory investments.
Contact:
Deloitte, www.deloitte.com
Bruce Geiselman
Senior Staff Reporter Bruce Geiselman covers extrusion, blow molding, additive manufacturing, automation and end markets including automotive and packaging. He also writes features, including In Other Words and Problem Solved, for Plastics Machinery & Manufacturing, Plastics Recycling and The Journal of Blow Molding. He has extensive experience in daily and magazine journalism.
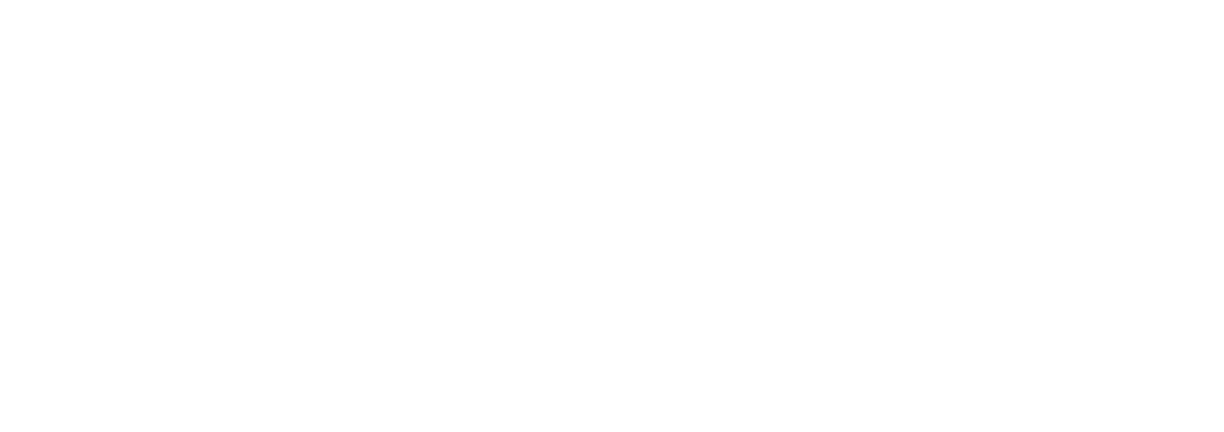