Conair's AutoWave feature adds more control, safety for conveying
By Karen Hanna
Corvettes are designed for speed, but when things go wrong, they have technologies to cushion a sudden stop — seat belts, air bags, crumple zones.
Conveying systems don’t go quite as fast, but they can carry their passengers — resins — at speeds exceeding 130 mph. Unfortunately, they’re not as tricked out for safety.
For plastics processors, the potential risks to resins and equipment mean speed isn’t everything. Conair is one company looking to make the journey smoother, with a new AutoWave feature for its Wave Conveying system, designed as a slower alternative to traditional dilute-phase conveying systems. It’s also upgraded its SmartFLX control, which can control both AutoWave, as well as the company’s updated Silo Truck-Fill Line Proofing technology, used for emptying large volumes of resin from trucks.
“AutoWave is truly going to keep your system optimized ... so you’re conveying the most amount of material possible to the material consumer at the slowest amount of speed,” said Nick Paradiso, conveying product manager for Conair.
AutoWave allows the Wave Conveying system to automatically modulate the speeds and methods for conveying resins, based on the resins’ particular characteristics. The technology represents an advance for the Wave Conveying system, which itself is unique because it offers multiple conveying modes.
As any race car driver knows, it’s not just how fast you can go, it’s about handling the turns well and getting there in one piece.
Paradiso discussed the potential hazards of dilute-phase conveying during the virtual Conair Summit.
“Your terminal velocity — the resin velocity before it enters the receiver or right as it enters the receiver — could be in excess of 5,000/6,000 feet per minute in a non-purge system, or in excess of 10 [thousand], maybe 12,000, feet per minute in a purge system, as those last pellets are streaming by to clean out that conveying cycle,” he said.
Dilute-phase speeds can be especially harmful when moving abrasive, filled or reinforced resins.
At high speeds, resins, like colliding cars, can suffer damage, including angel hair and fines. Resin also can cause damage by clogging or scraping equipment, including blenders, tubing elbows, receiver parts and valves. In addition, resin lost to production as dust can force the need for constant gaylord cleanouts — slowing production at a time when resin prices are especially high.
“If you're [conveying] glass-filled nylon and you're blowing through elbows every three months and you're scratching your head why, the reason for that is that that resin is just screaming down the line,” Paradiso said.
To prevent these problems, Wave Conveying offers two phases in addition to conventional dilute-phase conveying: Its wave-pulse phase moves resin in dense material pulses, while its wave-stream phase moves resin in rolling streams. The system offers slower, safer speeds of 300 to 2,800 feet per minute, and with its variable frequency drive, it also modulates the energy that it consumes, running only at the capacity the application requires. While slower than dilute-phase conveying systems, the Wave Conveying systems’ non-dilute-phase modes handle much more concentrated volumes of resins, so they’re able to match conventional systems’ throughputs.
With the AutoWave feature, users can reduce the problems and potential errors inherent in manual programming, as the system automatically optimizes resin’s route through conveying tubes, using information from system sensors and components to make real-time adjustments.
“The AutoWave feature eliminates virtually all of that manual programming effort,” Paradiso said in a press release. “Now, to convey a particular resin, a user needs only to use the new Conair SmartFLX HMI to select a source and destination, then open up a new, simplified receiver control screen and select a desired conveying phase — Wave Pulse, Wave Stream or Dilute. The AutoWave feature coordinates with the SmartFLX control and Wave Conveying components to complete the job.”
The SmartFLX control — the only control available to handle the AutoWave features — is 1,000 times faster than Conair’s previous-generation control, the FLX-128 Plus. The company says it’s designed for ease of installation, configuration and use. Equipped with a large color touch screen with descriptive graphics, enhanced diagnostics and advanced help screens, it is expandable, with the ability to control as many as 500-plus receivers, 80 pumps and 500-plus source valves. Users can easily add groups of receivers, pumps and valves; with each addition, they have access to an up-to-date wiring diagram.
Paradiso compared the automated conveying capabilities provided by AutoWave with the adaptive functions of an automobile engine computer, since both continually monitor and manage current performance settings, using each experience to inform reactions to later, similar experiences. Unlike an engine computer, which is factory-programmed, the AutoWave PLC can also be tweaked manually; operators can even add new, custom programs.
“This is the closest thing there is to plug-and-play variable-speed conveying,” Paradiso said.
The system protects both resin and conveying components.
“With wave conveying, we're able to achieve much longer life of your system components. We're able to virtually eliminate or minimize the amount of dust that's generated in your system or eliminate the angel-hair generation,” he said.
Conair updates Silo Truck-Fill Line Proofing
The SmartFLX is also the control for Conair’s updated Silo Truck-Fill Line Proofing system.
Designed to help ensure that resin goes to the correct silo when being offloaded from a truck or train, the Silo Truck-Fill Line Proofing system employs an electronically locked coupling to prevent the movement of resin without authorization. The system has been updated to use bar codes to communicate the information from shippers’ bills of lading to processors’ conveying systems.
With the Silo Truck-Fill Line Proofing system, plastics processors can avoid the types of mishaps Paradiso said some have recounted to him: “ ‘You know, we handed the key to one guy and it turned into a phone game where they handed it to the next operator who handed it to the truck driver and they opened the wrong lock somehow or the wrong silo was filled.’ ”
Such mistakes can mean processors must dump resin or drain and refill silos.
“Our control will decode that bar code and then automatically unlock the correct silo for the truck, the truck driver, to hook up to,” Paradiso said.
Karen Hanna, senior staff reporter
Contact:
Conair Group, Cranberry Township, Pa., 724-584-5500, www.conairgroup.com
Karen Hanna | Senior Staff Reporter
Senior Staff Reporter Karen Hanna covers injection molding, molds and tooling, processors, workforce and other topics, and writes features including In Other Words and Problem Solved for Plastics Machinery & Manufacturing, Plastics Recycling and The Journal of Blow Molding. She has more than 15 years of experience in daily and magazine journalism.
Request More Information
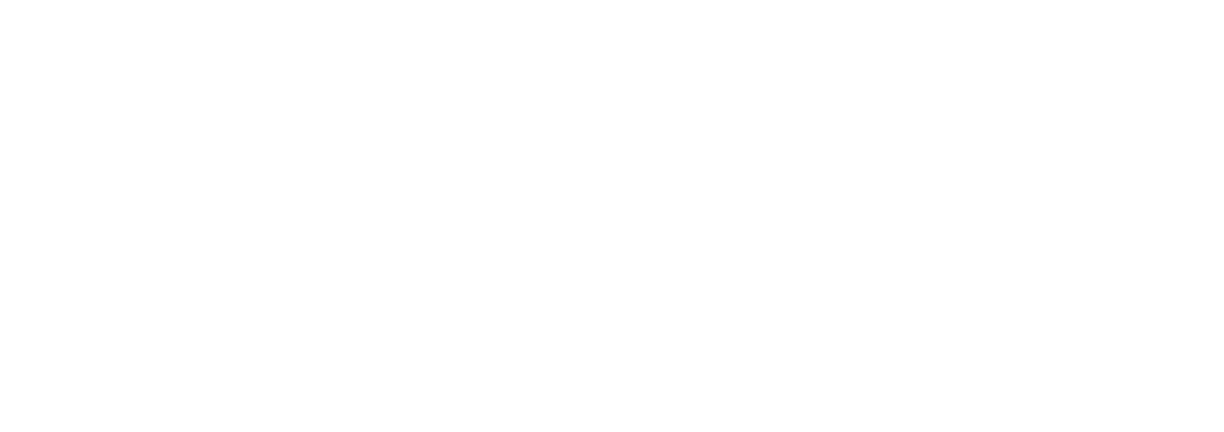