Conair creates the Rosetta stone for its dryers
By Karen Hanna
Ease of use is among the top expectations for operators of dryers, according to an executive for a company that makes the equipment.
“I’ve visited hundreds of customers, and people who are generally happy with their systems and their equipment all say similar things. This is something like, ‘We barely know what's there. We haven't had to touch it since we turned it on. It doesn't give us any trouble.’ And this tells me that there are two things that people value the most: consistency and simplicity,” said A.J. Zambanini, drying product manager for Conair, during the recent Conair Summit.
Not all equipment speaks the same language.
But, in a rollout scheduled to begin this fall, Conair’s dryers, blenders and other auxiliary equipment will have a lingua franca — thanks to the company's new common control.
The common control delivers a uniform user experience across different kinds of equipment. No matter the equipment, the controls use the same buttons, colors and nomenclature; options all are in the same places, allowing operators to quickly adjust from one machine to the next.
“We wanted to make it more intuitive for our users across all the product lines. We wanted to have a common user experience to help our customers reduce training time and increase operator efficiency. And we wanted to provide the most important information and settings immediately when the user walks up to a machine,” said Matt Shope, director of engineering, at the Conair Summit.
Several versions of the common control are available for Conair’s Carousel Plus line of continually rotating wheel dryers, which include the D-series and dX-series dryers.
They’re now easier to use, Zambanini confirmed.
“This will help to shorten the learning curve and allow you to spend more time doing what it is that you need to do on the shop floor, not trying to figure out how to utilize the dryer control,” he said.
The smallest D-series portable dryers and dX-series mobile dryers, with capacities of 15 pounds per hour to 400 pounds per hour, can be outfitted with a Plus or Premium version of the controls. Designed for simplicity, the Plus controller has a 4-inch color touch screen and comes with a dew-point monitor, dew-point control and weekly start/stop times. Operators can make selections for start/stop, and dew point and temperature settings all from one screen.
The Premium control, available as an option for the smallest dryers and standard with larger D-series dryers, comes with a 7-inch touch screen and offers more features. Dryer setup and status information appear graphically on a diagram, giving users a clear picture of the performance of all their dryers. As an option ideal for PET processors, users can specify the addition of an energy-saving Optimizer package — including a variable-frequency blower drive, Drying Monitor probe, return-air dew-point monitor, trap for volatiles and process-filter monitor.
According to Conair, compared with a traditional approach using conventional desiccant beads, the Carousel dryers’ continually rotating desiccant wheel exposes more desiccant surface area to processing air. It also requires less maintenance and eliminates the contamination problems commonly associated with desiccant beads. As a result, the dryers are more reliable, easier to operate and maintain, more energy-efficient and more cost-effective than other dryers, Conair said.
Karen Hanna, senior staff reporter
Contact:
Conair Group, Cranberry Township, Pa., 724-584-5500, www.conairgroup.com
Karen Hanna | Senior Staff Reporter
Senior Staff Reporter Karen Hanna covers injection molding, molds and tooling, processors, workforce and other topics, and writes features including In Other Words and Problem Solved for Plastics Machinery & Manufacturing, Plastics Recycling and The Journal of Blow Molding. She has more than 15 years of experience in daily and magazine journalism.
Request More Information
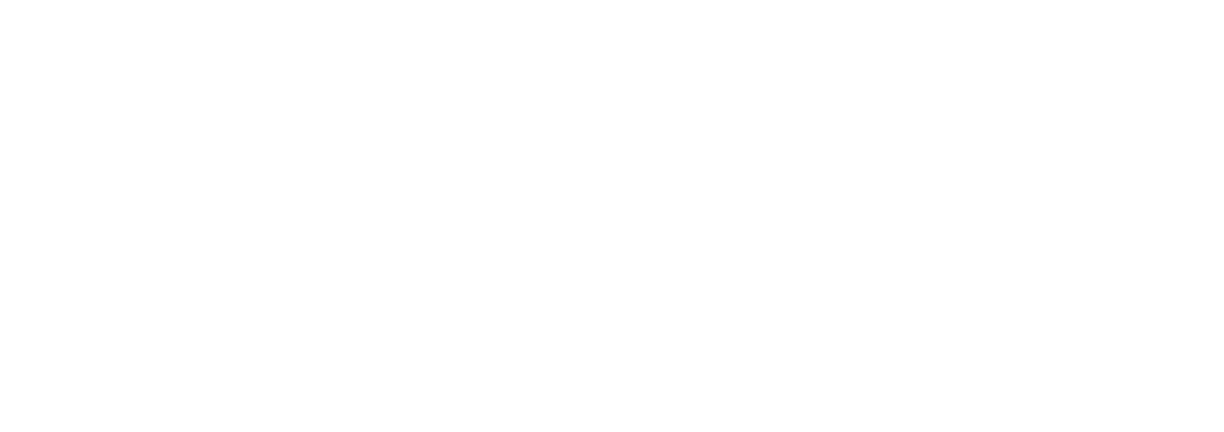