By Karen Hanna
As the world’s population grows, the Jetsons’ flying cars and electric vehicles will still find competition from an old standby — the bicycle.
Just as with other modes of transportation, the hallmark of the bicycle of the future could be lighter-weight or more-sustainable materials.
“While we’ve been [developing] game-changing technology [in] water systems injection molding, we will have now the opportunities ... for the engineering design and production of the bicycle of [the] future in thermoplastics,” predicted Umat Çakmak, managing director of Plastics Innovation GmbH, a spin-off company of Johannes Kepler University Linz in Austria.
Along with Michaël Callens, CEO and co-founder of Rein4ced, a Belgian manufacturer that has developed an automated process for adding steel fibers to composite bike frames, Çakmak was one of two speakers at Engel Lightweight Future Day in May with a focus on two wheels. Presenters looked at a variety of transportation modes — air travel, automobiles, even surfboards.
Produced using Engel technologies, electric bikes with hollow, injection molded, advanced thermoplastic composites — considered the first in the market — hit the streets in January.
“It’s mainly done in low-wage countries, [with] long lead times around two days until [one frame] is finished. With our injection molding technology, we can do that fully automated. So, right now, for our current bike, the cycle times are around 110 seconds, and we have production in Europe,” Çakmak said during his presentation, “E-Bikes — Sustainable High Volume Bike Frame Production with Fluidinjection.”
The e-bikes were made possible, thanks to the efforts of Engel, Plastics Innovation, Johannes Kepler University Linz and the V-Frames bicycle company in Schmiedefeld, Germany. Water — injected as part of Engel’s watermelt fluid injection technology — makes the process go.
“Once … the cavity is fully filled with polymer, we can open it up and inject water to push out the material, which is still in melt state, into an overflow cavity and, with that … we can produce hollow structures,” Çakmak said.
Full-series production awaits for the e-bikes, with mountain e-bikes set to roll out next year.
“With this, now, we have the material in the overflow cavity so post-processing and finishing is necessary, and you have increased material consumption. When you go into high-volume production, there is an option to put … the water injector opposite to … the injection point. So, here in this process the cavity would be filled and then water is injected, the screw is decompressed and, so, the material can be put back into the barrel and used for next shot,” Çakmak said.
Water washes through the hollow frames, ensuring no resin gums up the works. In full-series production, this process would allow unused resin in the hollow areas of the frame to be reused in the next shot.
Unlike alloy-frame bikes, the plastic e-bikes can be recycled to create new bikes, Çakmak said.
“We use the material for city bikes and can use it further in a subsequent stage for a kid’s bike or push bike,” he said.
Contact:
Engel Machinery Inc., York, Pa., 717-764-6818, www.engelglobal.com
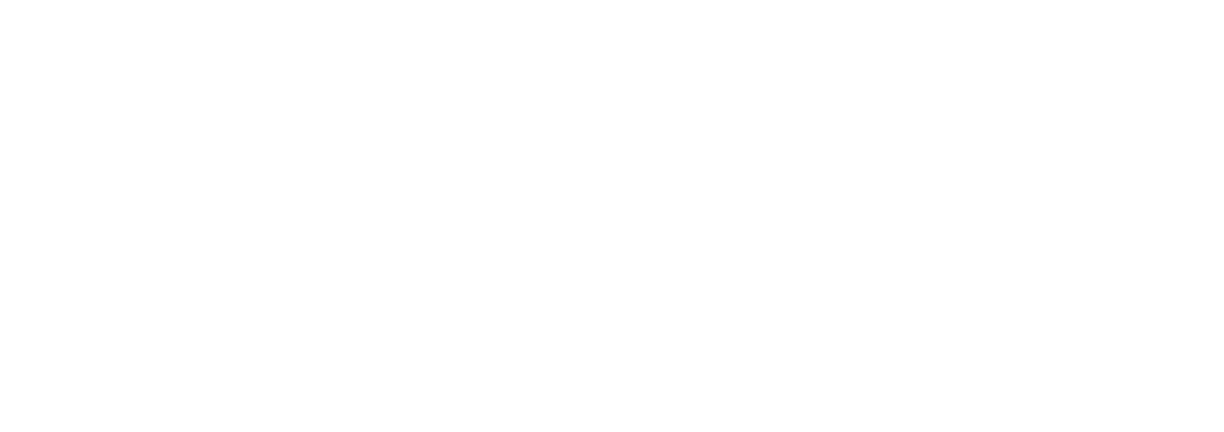