Niigon, StackTeck, Yudo team up to make overmolding more efficient, greener
By Karen Hanna
A work cell devised to slash the amount of expensive light blockers in milk bottles could help molders achieve greater efficiency while producing preforms that are easier to recycle, require fewer additives or contain more recycled content, according to officials at StackTeck and Niigon.
The work cell uses a Niigon Cube injection molding machine (IMM) with two standard molds and dual injection units to produce PET preforms for Ho Chi Minh City, Vietnam-based molder Ngoc Nghia Industry. The first injection unit introduces a layer of carbon black, to shield the milk from light that could cause it to spoil; the molds spin on a rotary table, and the second injection unit shoots a pearlescent-white outer layer, designed for aesthetics.
It's the first time a Cube has produced preforms, and it takes up less space and turns out more preforms than conventional, comparably sized IMMs, said Rob Sicilia, Niigon’s VP for PET technologies, which partnered with mold maker StackTeck and hot-runner manufacturer Yudo on the project.
“To do overmolding is a lot less expensive than to do co-injection, just from a capital perspective … [and] complexity, in terms of operating the system, because with overmolding, the steel dictates where the material goes, so you’re only having to inject on one side and make sure it rotates and then inject on the other,” he said. “Whereas the other processes that are out there, like the multi-layer co-injections, it requires a higher skillset, too.”
“Standard PET resin, you would probably be looking at about 8 bucks a pound for the color additive light-blocker material. It's a huge cost savings that you can save, just by going from the 15, down to the 4 [percent]. It's like more than 30 percent of the overall preform cost just in material,” he said.
The setup also accommodates higher-cavitation molds than conventional IMMs, Sicilia said.
“One of the big advantages is, if you have a center cube and your injection is on the moving platen side, you can take advantage of the real estate of the platen by having more cavitation for a given machine size,” he said.
The StackTeck mold used in the work cell has 32 cavities on each side, running on a 150-ton NPET150 Cube. By comparison, a conventional machine would have to be twice that size to accommodate the same mold, Sicilia said.
“For that same preform, because of the neck finish, it's limited to 32; otherwise, we could do a 48-plus-48,” Sicilia said. “But, if we were to stay with that same format neck finish, if we applied this to a 300-ton machine, then we’d be able to do 72-plus-72.”
Jordan Robertson, VP of business development and marketing of StackTeck, said, along with Yudo, the companies worked to coordinate the movement of the mold and automation to squeeze in as much functionality as possible.
“We have advanced cooling technologies that enable us to cool the material so that you’re ready to open up and start the next cycle in the shortest period of time,” he said.
While the current arrangement was developed to optimize light blockers, Robertson and Sicilia said similar setups could help molders address sustainability issues. For example, bottle makers could optimize the amount of recycled PET they use by molding it over a thin layer of virgin PET.
“With that approach, generally speaking, we’re confident that we could have that preform be 75 percent by weight in the second shot for the recycled material,” Robertson said.
Co-injection approaches can produce layers weighing in at about 30 percent of the final part weight, but cube overmolding can further minimize layers to meet molders' needs, Robertson said.
With “overmolding, because the steel defines the geometry, I could theoretically mold an inner layer of virgin material 20 percent of the overall part weight and overmolded with anything … at 80 percent.”
Contact:
Niigon Machines Ltd., Vaughan, Ontario, 905-265-0277, www.niigonmachines.com
StackTeck Systems Ltd., Brampton, Ontario, 416-749-1698, https://stackteck.com
Yudo Inc., Livonia, Mich., 734-744-8120, www.yudousa.com
Karen Hanna | Senior Staff Reporter
Senior Staff Reporter Karen Hanna covers injection molding, molds and tooling, processors, workforce and other topics, and writes features including In Other Words and Problem Solved for Plastics Machinery & Manufacturing, Plastics Recycling and The Journal of Blow Molding. She has more than 15 years of experience in daily and magazine journalism.
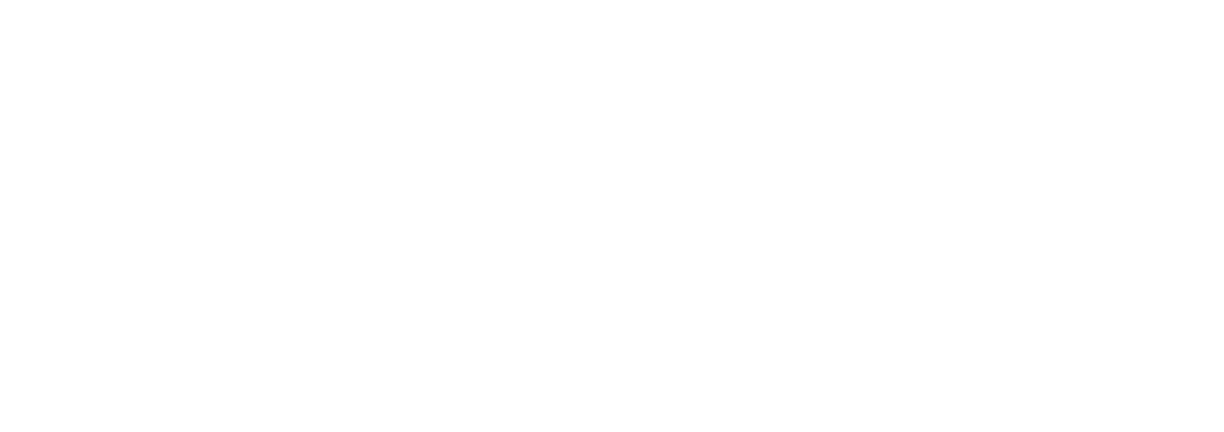