By Karen Hanna
“This seems to be further extended and has got more extenuating circumstances than Katrina did,” said Todd Poteat, the VP of manufacturing at Bright Plastics in Greensboro, N.C., which has experienced difficulties sourcing resins since a massive winter storm blasted Texas in February.
The resin supply chain has suffered problems that could be compared with recovery from a hurricane like Katrina — only they’re more widespread, and probably longer-lasting, said Esteban Sagel, a principal at Chemical and Polymer Market Consultants, which tracks the materials market.
“What we have is a massive constraint in supply,” Sagel said.
Sagel said the resin supply chain first became stretched when demand for goods soared after initially bottoming out in the beginning stages of the COVID-19 pandemic. This sudden spike in demand, coupled with labor shortages due to the pandemic, has created bottlenecks at ports and a lack of empty containers for shipping. Then, in February, the storm crippled the power supply across Texas.
Prices for some resins have nearly tripled in a year, Sagel said.
"Because we don’t have enough people, we’re able to reassign them, but occasionally we’ve had to send people home,” Poteat said.
The situation is even more pronounced at Confer Plastics Inc. in North Tonawanda, N.Y. For the first time in its 48-year history, the maker of pool and spa products has had to declare force majeure.
“Our allotments of material have been cut back to 30 percent of what they normally might be each week,” company President Bob Confer said in early March. Having survived the oil embargoes of the 1970s, the blizzard of 1977, the Great Recession and the pandemic, Confer Plastics has taken a historic step — the company, which employs 210 people and runs 20 blow molding machines, was forced to temporarily lay off 40 people.
“We’ve shut down some of our machines to ration material, and we’ve told our customers that our lead times have increased dramatically,” Confer said.
While plastics processors take a hit, one company is experiencing a surge. iD Additives supplies fillers and foaming agents that can make resins stretch a bit further in each shot.
“I usually tell guys, ‘Look, I can save you money when it’s priced at 50 [cents per pound]. Imagine what I can do for you when resin goes up to 90, which invariably it does once a year at least. This isn’t the first time,” said Nick Sotos, president of iD Additives. “This is the largest spike we’ve ever seen.”
By using filler, foamers or both, processors can save 8 to 10 cents a pound onSotos said plastics processors have been turning to his company for help. “You know, it’s very hard to just take these increases and just pass them on. … We’re getting calls from guys who are looking at ways to mitigate some of this,” Sotos said.
Companies that deal with a variety of resins are feeling the pinch. Confer Plastics uses a lot of HDPE, but that’s not the only material being affected.
ID Additives recently worked with a processor in Chicago trying to cut its need for flexible PVC.
“Engineering grades are all up. Polystyrene is up. Polypropylene is up. Polypropylene is probably the biggest right now. Polyethylene is up,” Sotos said. “There is not a resin right now that that isn’t up that we’re not getting calls on. I got a guy who was saying, ‘I use ABS, what can you do?’ ”
Poteat and Confer said the issues could plague the industry for a while.
“It’s difficult to tell when this ends. Suppliers and brokers tell us that by month’s end, most of the producers should be back to full strength, but then there’s their backlog to contend with. It’s four to seven weeks of lost production that will haunt the entire industry all year,” Confer said. “How do we as an industry ever catch up?”
Poteat sounded an even less-optimistic note. He thinks PP and PE prices and availability might improve by the end of the year. Other grades might take longer.
“ABS is probably the worst at this point. Then, nylons, PPEs [polyphenylene ethers], PEs, the pricing is going up so rapidly. It’s amazing, the cost difference in just two months,” Poteat said.
Recovery from Katrina took about a year, providing one roadmap to anticipate what’s next, as the industry copes with shortages and price increases.
“Everybody’s suffering from that,” Poteat said. “You know, even if you got the order, you can’t get what you need to run it with. It’s a difficult time.”
Karen Hanna, associate editor
Contact:
Chemical and Polymer Market Consultants, Houston, [email protected], www.chempmc.com
iD Additives Inc., La Grange, Ill., 708-588-0081, www.idadditives.com
Karen Hanna | Senior Staff Reporter
Senior Staff Reporter Karen Hanna covers injection molding, molds and tooling, processors, workforce and other topics, and writes features including In Other Words and Problem Solved for Plastics Machinery & Manufacturing, Plastics Recycling and The Journal of Blow Molding. She has more than 15 years of experience in daily and magazine journalism.
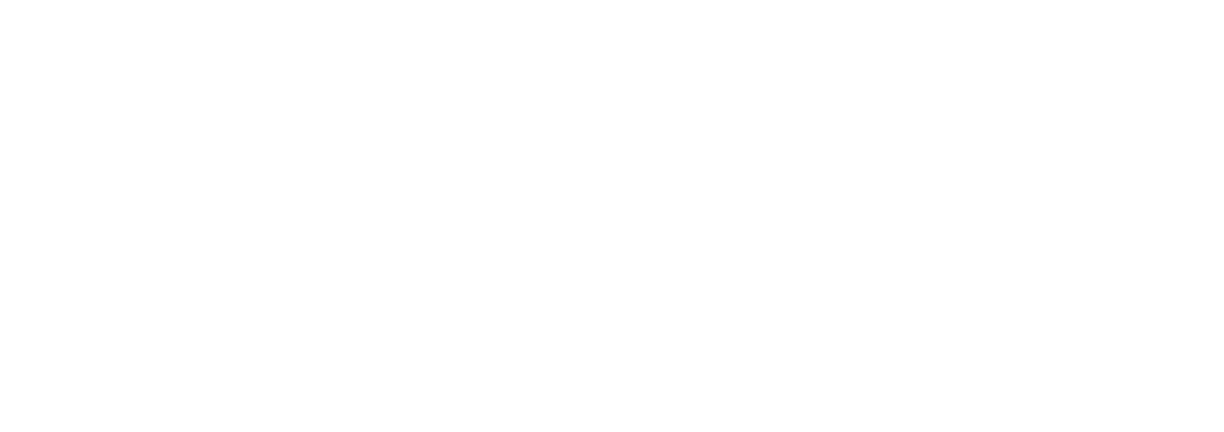