By Karen Hanna
Looking to change from manufacturing blue parts to yellow parts, a processor was upset at the results of a long-delayed machine purge. The colors that were coming out exposed the story of long-neglected contamination — a situation purging compound makers advise others to avoid.
“For the record, they were interested to purge because they never cleaned their machine,” said Mathieu Rioult, global marketing and communication manager for Polytechs, which makes Clean Xpress. “They tested our product and started to complain it was not working, and they sent a video where purple, gold, red, green colors were being purged.”
As health experts have stated repeatedly over the last six months, frequent, proper hand-washing is fundamental. Machines should be treated no differently, say representatives of companies that make purging compounds for extrusion processors and injection molders.
Scholl and others emphasized the importance of regularly using purging compounds to flush machines of material — even in machines used to process only one type of resin or color. They emphasized users need to be sure they’re employing products and purging carriers that are well-matched to the resins they’ve run through their machines. And, they said, users need to read and follow directions.
It’s advice that pays off, according to a colleague of Scholl’s. “When the right product is used in the right moment, it generates really substantial savings,” said Laurent Saleur, global technical support manager, thermoplastics, at Chem-Trend.
Bill Duff, GM of sales and marketing for Yizumi-HPM, said too many processors ignore problems, including buildup, as well as wear and tear, involving their screw and barrel. “What happens is, you’ll start to see wear and you'll start to see slippage, and, in some instances, customers may relate that into there’s something wrong with the machine,” he said.
“No matter how much they’re purging right now, they should purge a little more often,” he said.
Slide Products is among companies that have recently announced new purging compounds. They include several for high-temperature, engineering-grade resins like PEEK and Ultem, which previously had to be purged with regrind or were eliminated from machines via complete tear-down. Some of the newest purging compounds include: Slide Products’ HT Purge, for temperatures of up to 752 degrees Fahrenheit; and Polytechs’ Clean VHR, for use with hot runners and temperatures of up to 608 degrees Fahrenheit. Chem-Trend also recently released purging compounds for extrusion blown film, as well as a food-compliant formulation for engineering resins.
Representatives of purging compound makers said too many processors purge only when the parts they’re making are off-color, due to the buildup of different-colored resins in their machines’ barrels. However, color isn’t the only problem — whatever resin is built up in the machinery is subject to so much heat history that it will degrade the characteristics of any parts with which it becomes enmeshed.
“Purging is essential to increasing efficiencies and profitability in any plastic processing facility,” said Dave Denzel, technical manager at iD Additives. “Whether experiencing black specks caused from resin degradation or color contamination from a previous production run, most part aesthetic issues are related to the lack of a purging program.”
“If you do not remove those from your screw and barrel when your equipment is down, they’re going to start to accelerate the process of the wear on the screw and barrel itself,” he said.
Buildup in the machine also can affect the cushion of material in front of the screw tip, leading to inconsistences, he said.
He echoed many of his competitors when he emphasized the importance of making purging part of the routine. Freestyling,“I’ve got guys that I’ve heard of have used things like Coca-Cola, they’ve used Tide … old garden hose because those are PVC,” said Grzegorek, who’s been in the business more than 35 years. He’s even heard of people dumping hand soap into machines. “Everybody’s tried a lot of different things to get away from purging compounds.”
While he acknowledged there’s no magic elixir, these home brews aren’t as effective as purging compounds. Though the initial cost seems a bargain, Grzegorek said processors end up paying more, when they take into account the cost of downtime and scrap.
As an example, he cited one molder that took a $480 hit every color change. The purging compound the molder eventually used was more expensive than its home remedy — but, with the savings in downtime and wasted material, Dyna-Purge presented a net benefit of $400.
Responding to crisis
Both regular shutdowns and emergency shutdowns provide an opportunity to clean out machines.
“Preventative purging is also crucial when expected downtime is to be out of the norm,” said Matthew Silva, a sales representative for Intro-Tec, which distributes Coratex. The last six months prove instructive. “For example, when the pandemic started in March, what we found was many customers shutting down lines prematurely, without taking the steps to purge out product and contaminates, only to return weeks and, in some cases, months later to unusable equipment. This leads to material oxidization and the need to manually strip down and clean components such as the barrel, screw, nozzle and dies.”
When faced with a shutdown, Grzegorek advised that processors should fill their machines completely with purging compound.
“That seals the system and keeps that oxygen out,” he said. This prevents material in the machine from oxidizing and turning into carbon.
Like her competitors, Kathleen Jarvis, national sales director for Neutrex, which sells its products under the Purgex name, recommends that processors plan ahead.
Recently, she spent some time on the phone dealing with a panicked processor. “They told me they literally had trucks outside waiting to pick up parts that they hadn’t molded yet,” she said. The molder was trying to make white parts — unfortunately, it most recently had made blue parts, and the color was still caked inside.
For Jarvis and others, the problem is avoidable. ““The idea is to purge more often when molders can control it instead of when they get into a putting-out-a-fire situation,” she said.
And, at a certain point, it’s too late to do anything about it — except tear down the machine or hot runner completely.
Simply creating a routine and following it can head off trouble.
“I think all of us face it as a constant basis and probably always will, and that’s, whenever there’s a problem, you go back to, ’Are your following procedures,’ and nine times out of 10, maybe 10 times out of 10, the answer is no,” Jarvis said.
Karen Hanna, associate editor
Contact:
Chem-Trend LP, Howell, Mich., 517-545-7980, https://chemtrend.com
Dyna–Purge Division Shuman Plastics Inc., Depew, N.Y., 716-685-2121, www.dynapurge.com
iD Additives Inc., La Grange, Ill., 708-588-0081, www.idadditives.com
Intro-Tec LLC, Miramar, Fla., 954-704-9461, https://intro-tec.com
Neutrex Inc., Houston, Texas, 281-807-9449, https://purgexonline.com
Polytechs SAS, Cany-Barville, France, 33-620-953-324, www.polytechs.fr
Slide Products, Wheeling, Ill., 847-541-7220, www.slideproducts.com
Karen Hanna | Senior Staff Reporter
Senior Staff Reporter Karen Hanna covers injection molding, molds and tooling, processors, workforce and other topics, and writes features including In Other Words and Problem Solved for Plastics Machinery & Manufacturing, Plastics Recycling and The Journal of Blow Molding. She has more than 15 years of experience in daily and magazine journalism.
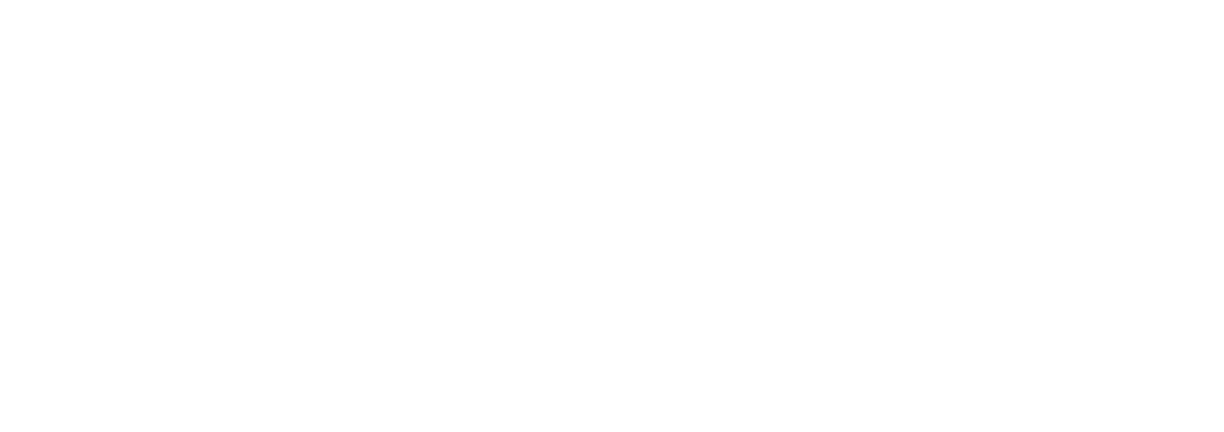