Stan Glover’s early fascination with the world beyond his hometown in the Finger Lakes region of New York led him on a path that is benefiting plastics machinery manufacturers and processors in ways they do not realize. He is chairman of the Plastics Industry Association (PLASTICS) Equipment Council and chairman of the U.S. Technical Advisory Group (TAG) of ISO Technical Committee 270 (ISO/TC 270), which oversees standardization of machines used to prepare and process plastics and rubber. This work, which includes developing safety standards for injection molding and extrusion machines, as well as magnetic platens, gives Glover an important voice in standardizing safety requirements and practices for processing machinery around the world.
He graduated from Hiram College in Ohio with a degree in Middle Eastern Studies, and along the way spent a year in Egypt at the American University in Cairo and a year in France learning the language. After a couple of jobs selling industrial components and tool steel, he joined Zeiger Industries in Canton, Ohio, and attended his first meeting of the Society of the Plastics Industry — as PLASTICS was known then — in 1992. He was soon involved with SPI’s Global Business Council and Equipment Council and five years later was drafted to work on the equipment safety standards committee.
The early safety effort was mostly writing standards to bring older processing machinery up to a safe operating condition. But eventually he played a key role in the international effort to harmonize U.S. standards with those of other countries, a significant benefit for machinery manufacturers who want to sell equipment around the world.
Today he is active as the PLASTICS representative in worldwide safety standards and is also recognized as an expert on wear and corrosion technologies in injection molding equipment. Glover recently talked with Plastics Machinery Magazine editor Ron Shinn about his career and involvement with safety standards.
How did you go from a college graduate with a Middle Eastern Studies degree to Zeiger Industries?
Glover: I knew before college that I wanted to work in the international arena. My mother’s father traveled internationally for Eastman Kodak and my grandmother was the founding president of the Rochester (N.Y.) Sister Cities program. They took me when I was 15 on my first international trip to Spain and France and Switzerland. I fell in love with the language and culture, and that sent me into Middle Eastern studies in college.
My first job after college was with a company headquartered in Quebec. I sold industrial springs in the U.S. My French language abilities were important.
My next job was with Buell Specialty Steel Co. Inc. in Rochester, where I started calling on mold-making companies. I fell in love with plastics and knew I wanted to be in technical sales in this industry. My next job was in the Cleveland sales office of Crucible Specialty Metals.
What was your plastics industry education like?
Glover: The first molding plant I visited was the old Harrison Radiator plant in Lockport, N.Y., when I was with Buell. They were molding big radiator components for General Motors. When I moved to Cleveland, I called on a lot of the largest processing facilities, such as Hoover and other big mold manufacturers. So, I would go in and sell our mold steel, but at the same time I was being introduced to the technical side of processing.
How did you end up at Zeiger Industries?
Glover: When I visited Hoover, I met Don Zeiger, their production and process engineering manager. I worked with his engineers. When Don retired to start up Mallard Machine, which was the predecessor to Zeiger Industries, he asked me to work for him. I started there in April 1990, and from that point my focus was directly on injection molding. It was no longer just the tooling side, but my tool steel knowledge played heavily into my involvement with Don.
I started as director of sales but later became director of technical sales. More of my day-to-day job is technically based than selling. At the global level, the OEM market in particular, and to a lesser extent the processors, are looking to have technical discussions about any given product, and they will frequently request technical support and management to be involved in developing new applications or solving existing challenges.
How did you get involved with PLASTICS, or SPI as it was then known?
Glover: My first meeting was in 1992 in Arizona with the components division. I met a bunch of other manufacturers of plasticizing components and front-end materials. Today, the components division is part of PLASTICS’ Equipment Council.
I got involved with the Global Business Council because of my international background.
Fast-forward to 1997 when someone said they needed expertise on safety standards, so I worked with the late Bill Carteaux, who was then chairman of the vertical injection molding safety standards committee.
What was the challenge for a horizontal molding machine safety standard?
Glover: Before the turn of the century, but especially after 2000, we were getting a lot of pressure from Europe to remove our requirement for the mechanical safety device known as the jam bar. The state-of-the-art had developed to the point that a mechanical device was seen as obsolete and redundant. To be really honest, it took us until 2017 before we developed the standard that made the mechanical device a redundancy.
The mechanical jam bar is still required on vertical molding machines due to the effect of gravity. But now that the jam bar has been put aside on horizontal molding presses, that allows a machine made in China or Germany or Austria or Italy or Japan to be sold in the United States market without those devices. That means machinery manufacturers are able to reduce their inventory requirement because oftentimes U.S. suppliers were carrying inventory that was mandated to have the mechanical device whereas the rest of the world did not.
What happens when the worldwide standard is approved?
Glover: The ISO published ISO 20430 on April 24. The United States voted in favor of the proposed global injection molding standard, and now on a national level we will have to make sure everything meets the requirements of our other domestic safety standards. The standards in the U.S. take precedence over global safety standards. So, we still have some work to do. It took eight years, but we finally got ISO 20430 done. Now we’ve got a global safety standard for the United States to review and adapt in whatever form makes the most sense for us.
Does that mean there are no more jam bars required anywhere in the world?
Glover: No. The state of Michigan still requires it, but we are working actively through PLASTICS to make the Michigan standard the same as the rest of the world. They had reopened a review of the mechanical device requirement, but the review was put on hold when COVID-19 hit.
What other safety standards have you worked on in the last 23 years?
Glover: Back in 2004-2006, I was chairman of the magnetic clamping guideline committee when we developed the first magnetic mold clamping guideline in the United States. We developed certain protocols to address the risk associated with using a magnetic platen when hanging a mold into a molding machine. ... In 2017 an International Organization of Standardization subcommittee on machine safety created a working group called WG 3 to develop a global safety standard for mold clamping systems with an original focus on magnetic clamping devices. The work we did back in the mid-2000s has largely been used as the template for the new ISO effort. The working group was supposed to meet in Milan, Italy, in July but the COVID-19 situation put that on hold.
The Plastics Industry Association will serve as the convenor of ISO/TC 270 WG 2, Safety of Plastics Extrusion Machines when it starts work soon.
How do you juggle the time it takes to do PLASTICS’ work and your regular job?
Glover: The Zeiger Industries team has allowed me to pursue this. Don Zeiger always said that he expected us to be fully engaged with SPI and PLASTICS, and when he sold the business to his two sons, Tom and Steve, they’ve supported my efforts internationally. They see the merit of what we are doing at PLASTICS on the safety standard side of things.
I said early on that my focus was on international business and today I can say that I met one of my personal career objectives, and that was to move up through the international community and deliver something back to the United States that made our machinery industry and our processors safer. This was something I recognized back in 1997 when I first started.
How would you like to be remembered?
Glover: As making the injection molding industry and processing community safer. On a more personal level, there is nothing I would like to see more than to have one of my three kids follow me into technical sales in the plastics industry.
Just the facts
Who is he: Stan Glover
Title: Director of Technical Sales, Zeiger Industries
Location: Canton, Ohio
Age: 59
College: Hiram (Ohio) College, BA in Middle Eastern Studies.
Ron Shinn | Editor
Editor Ron Shinn is a co-founder of Plastics Machinery & Manufacturing and has been covering the plastics industry for more than 35 years. He leads the editorial team, directs coverage and sets the editorial calendar. He also writes features, including the Talking Points column and On the Factory Floor, and covers recycling and sustainability for PMM and Plastics Recycling.
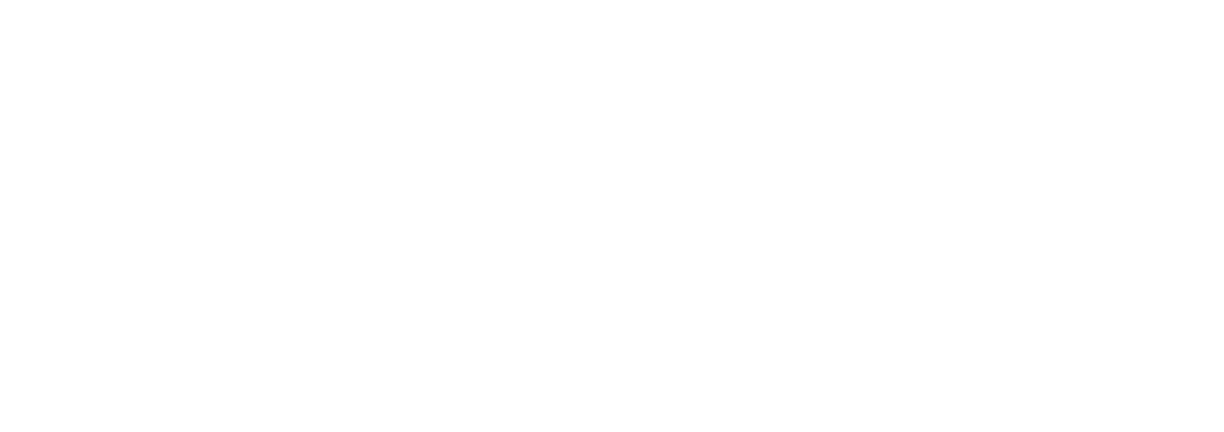