A new injection molding machine design that electrically heats the barrel and screw for improved melt processing capability was a highlight at the Molding 2016 Conference in March in New Orleans.
Extrude To Fill LLC, Loveland, Colo., a 2-year-old manufacturer of injection molding machinery and tooling, developed a new press that does away with the need for the high pressures and resin shearing that generate frictional heat to melt the polymer in the screw and barrel. "The physical mass of traditional machines and their molds increase in order to both generate and contain pressures used within the system, pressure that serves material preparation more than the molded part," said Rick Fitzpatrick, the company's CTO and co-founder.
Instead, Extrude To Fill designed its patent-pending X2F injection molding unit to melt the polymer by employing an extruder screw and barrel that are electrically heated internally, as well as a proprietary sensor-based control system that automatically adjusts all components on the machine. Among its responsibilities, the sensor technology can run heat control loops and sense motor torque load and melt state. It uses unique algorithms to ensure optimal process conditions for the melt.
LOWER MASS FOR SAVINGS
The X2F does not rely on excessive pressures to frictionally melt polymer before forcibly injecting it into the mold. This allows the screw, barrel, platen, mold and other mechanical aspects of the machine to have significantly less mass, Fitzpatrick said. The reduced mass results in a lower price and lower energy and operating costs.
"Our process does not rely on rapid injection of a fixed volume of material from the injection chamber," Fitzpatrick said. With the X2F, many molding decisions are turned over to the machine. "You tell the machine what you want the output to be in terms of mold pack pressure. Then you let the machine run and utilize its algorithms to achieve the desired result," Fitzpatrick said. This "fixed output" approach differs from traditional "fixed input" methods where the molder sets numerous process parameters, molds the part, then has to look into the mold to see what actually happened.
USE ELECTRICITY TO MELT MATERIAL
In the X2F unit, the screw and barrel are electrically heated and conduct that heat to the material, bringing it to a homogenous state without movement. Molten material is pumped by the screw into the mold cavity. This occurs at a lower pressure and temperature than conventional injection molding.
The maximum clamping force required is based on the pack and hold pressure, rather than injection pressure used to push melt into a cavity. The control system provides a continuous controlled flow of material throughout the melting and pumping stages. The pack and hold pressure is built up as material fills the cavity. The increased melt control possible via the sensor technology improves part quality. With the X2F, there is no cold slug in the nozzle. The nozzle features a mechanical valve that allows continuous extrusion of the melt under pressure into the tool.
The design lowers the clamping force requirements for the machine and reduces the strength requirements for the tooling. "Less water is required in the mold and less clamp pressure is required due to the tight control of the pressures and temperatures," Fitzpatrick said. "In many cases, the water circuits in the platen are sufficient for mold cooling because less heat is going into the mold." A commonly used formula for clamping force requirements shows the savings. Traditional molding machines apply 3-5 tons of clamp pressure per square inch of molded part, while the Extrude To Fill machine uses 0.5-1.5 tons of clamp pressure.
In addition, the lower clamping force requirements provide an opportunity for molders to use aluminum molds, which can lower tooling costs compared to steel molds. Aluminum tooling can be bolted directly to the platen and installed and removed in 10-15 minutes using simple tools, Fitzpatrick said.
The X2F machines use thin-walled barrels that are designed to electrically conduct heat. The approach requires just 10 percent of the energy consumed by a conventional injection unit using frictional heat.
NEW TECHNOLOGY
The machine technology is the result of several developments, including the application of new sensor-based methods for achieving control of melt viscosity at a range of injection pressures and injection speeds. The sensors act on flow data — gathered from the extruder and combined with process cycling data — to adjust the heating profile of the injection unit proactively.
The system processes molding data in real time, using algorithms to interpret the sensor data, to achieve the ideal melting state for the material, Fitzpatrick said.
Extrude To Fill offers two versions of the X2F, the E20 and the E50, both of which are available in horizontal (H) and vertical (V) configurations. The E20s have a shot capacity of 30 grams and can handle mold sizes of up to 8 inches by 6 inches. They operate with 110 volts and require about 1 kilowatt (Kw) per hour of energy, Fitzpatrick said. The E50s handle up to a 120-gram shot and require 2.5 to 3 Kw per hour of electricity, Fitzpatrick said. The machines are compact and light, weighing 250-750 pounds, with dimensions similar to lab-sized or tabletop units.
A major benefit of the X2F is that molders can operate it on an on-demand basis. The system is suited to both low- and high-volume production runs. "Low part costs are achieved with four- and eight-cavity molds," Fitzpatrick said. Extrude To Fill also offers a multiport array configuration, which allows a cluster of injection units to feed a cluster of mold cavities through a single mold plate, to produce a range or multitude of parts.
Due to the design of the screw and barrel, changing materials or colors is quick and easy with minimal purging. The screw and process are robust enough to process any commercially available resin, including highly filled resins, colored PP, clear PC and recycled materials. It also can be used with metal injection molding. "This technology allows a molder to easily switch between plastic injection molding and metal injection molding on the same day," said Fitzpatrick.
Mikell Knights, senior correspondent
Contact:
Extrude To Fill LLC, 877-572-2662, www.Xtrude2fill.com
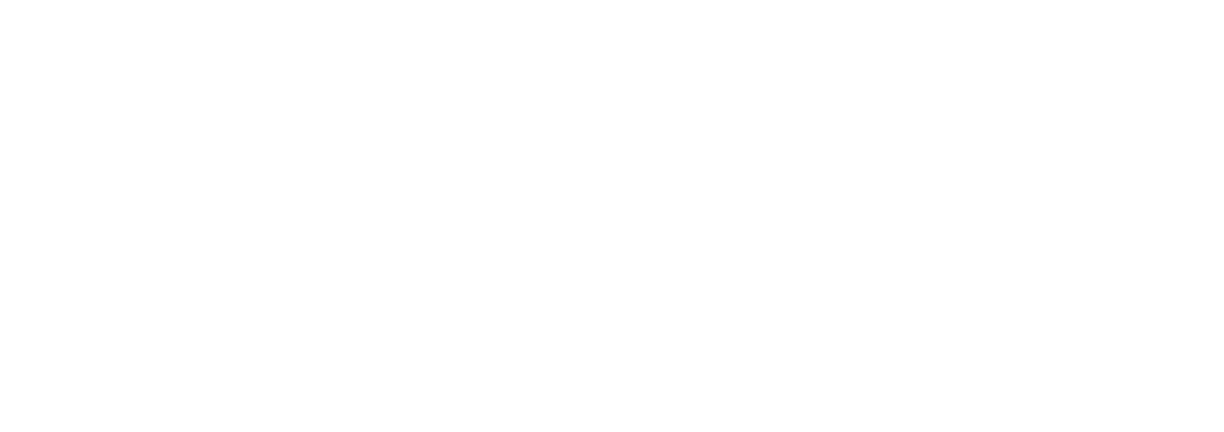