At custom injection molder Ess Tec Inc., Holland, Mich., the staff always is thinking and tinkering to meet customers' needs. Officials recently sat down with Plastics Machinery Magazine to talk about the latest equipment investments and how at one time a sprue picker equipped with end-of-arm-tooling (EOAT) was the fanciest "robot" in the plant.
The company is known for its prowess in high-quality molding mainly for automotive parts. It operates in a region populated with larger companies focused on automotive parts. A key strength of Holland and nearby Zeeland is the entrepreneurial atmosphere.
"That is a huge part of West Michigan that has made West Michigan what it is," says Ess Tec VP Jim Davis. Ess Tec was founded in 1992 by husband-wife team Larry Essenburg, who remains president, and Connie Essenburg, its CFO. Their son, engineering coordinator Elliot Essenburg, represents the second generation.
During the past year, it has expanded its facility by 12,000 square feet for a total of 58,000 square feet. The company moved to the site in 2010 after spending all those years in an old boat plant that had been converted into an industrial park. There, Ess Tec was able to lease one bay of space and then add on as needed.
"As we grew, we could lease another bay of space," explains Elliot Essenburg. "Then we started leasing office space. That enabled us to grow sequentially. The downside there is when you add one bay of space, put two machines in there, lease another bay, equip that, you don't always end up with the nicest flow."
But the priority for Ess Tec always has been investing in its process and worrying less about the appearance of a building, especially at the old boat plant.
"You've got to put your money into your process," says Davis. "That has got to be good first. Our building wasn't beautiful. We spent the money on good equipment because the reality is that it doesn't matter how shiny your building is. If you're shipping junk, sooner or later you're going to have a problem."
Ess Tec grabbed the site once it was available because it was a perfect fit. The plant floor is configured so that the smaller tonnage machines are at the front of the plant floor and the larger tonnage machines are at the back. A welding and assembly area is just off the main floor.
"We've definitely been blessed, and we keep being amazed at everything," Elliot Essenburg says.
The company's recent equipment investment includes a two-shot Engel victory 85 (U.S. tons) that has a rotary table and an integrated Engel easix multi-axis robot. This new manufacturing cell is being used to produce backlit control panel buttons. In this process, Ess Tec uses a 6+6 cavity mold where white PC is partially overmolded with black PC-ABS in the second set of cavities. Transfer molding still is used as the primary technique in multi-component injection molding but use of the rotary process just is a matter of time within Ess Tec.
Doing away
with the tie bars
This is one company that is outspoken about its loyalty to tie-bar-less injection molding machines.Once the technology became available, the company purchased only tie-bar-less machines and it plans to maintain that approach. The company's 24 presses now range from 35 to 240 tons. This is based on Larry Essenburg's philosophy. Though small molds on large machines were the industry standard when the business was started, Larry Essenburg saw things differently with a goal of focusing on small-tonnage molding.
So Ess Tec started doing the opposite — putting larger molds into smaller machines. Customers became convinced of the benefits and that is where Ess Tec achieved lower unit costs. As it turned out, the company would become Engel's first customer in the United States to fully support the completely new tie-bar-less design. Remember, Engel first debuted the technology at the K Show in 1989. Ess Tec began business just three years later. The industry philosophy for injection molding machine design was that a clamping unit had to have four tie bars.
Elliot Essenburg explains the philosophy further.
"A large machine can fit a large mold and a small mold in it, but a small machine only can fit small molds in it, so often people decide to only have large machines. However, molds often become large because of tooling requirements such as slides, core action or family tools where the parts don't run together, but the part doesn't require a large shot size or higher tonnage.
"Engel's tie-bar-less technology allows us to avoid the constraint of tie bars to utilize a machine with an appropriate shot size for optimal shot control and tonnage for mold protection. Smaller machines are also less costly to purchase and operate," he says. "We have had numerous times where 'problem jobs' have moved to our facility because other molders failed to match a machine with appropriate capability for the mold's requirements. Our machine capability combined with our commitment to stable processes and high-quality parts make us a perfect fit for these difficult-to-produce jobs."
Elliot Essenburg can cite several examples. A molder was attempting to run a 16-cavity pivot-pin tool in a 120-ton machine. The molder was plagued with quality defects that were difficult to spot and bad parts were being passed to the customer. Shot control problems were causing short shots or overpacking of the parts, causing them to stick on the cover half of the tool. Tool damage was occurring because the machine could not detect parts at mold close and the parting line and vents were becoming damaged. Ess Tec was able to repair the parting line and correct the venting issues and then run the mold in a 60-ton machine at a ppm (parts per million) defect rate of virtually zero.
There also was an automotive retainer plate that was used in the assembly of an overhead console. Another molder was running it in a 250-ton machine. Ess Tec converted it to a 100-ton sans tie bars.
"In this situation, the part design allowed us to use less tonnage than [was] typically required for the amount of projected area this part had," Elliot Essenburg says. "The freedom from tie bars, the lack of platen deflection, and precise shot control enabled us to hold a flash-free parting line. We don't trim flash here at Ess Tec; if the mold is flashing, it is a processing or a tooling problem."
Automation
as its biggest push
There was a time, as previously mentioned, when Ess Tec configured sprue pickers with EOAT because the company did not have the money to invest in a robot. The company is financially conservative and pushes boundaries in innovation to meet its goals.
"We really were quite ingenious with our sprue pickers," says Davis. "We actually had a five-button tool that had two sets of five buttons so we went in with a sprue picker, because at the time we did not have the money for a robot, so we went in and built EOAT for the sprue picker, picked up those buttons. In fact, we're using the same concept today but we're using a robot. We dropped the buttons into 10 tubes to keep them separated and they went into little bottles."
The company did this for years, Elliot Essenburg emphasizes. Davis was part of the design team; Elliot Essenburg was faced with tweaking the concept and ultimately, getting it to work.
"We wore out two sprue pickers doing it, but it worked," says Elliot Essenburg.
"Most people would look at that and say, 'You did what with a sprue picker?' It worked," echoes Davis.
Now, automation and Ess Tec's choice of robotics are a bit fancier. The Engel easix is the first multi-axis robot at Ess Tec. The robot can access the cavities directly from the side so that it can operate safely within a small space, says Engel.
"We are always looking into doing what we can do for our customers. That is what got us into the robotics and other automation things," says Elliot Essenburg. "We have a part that somebody is picking out by hand. You look and you say, you can do that, but it's not consistent. Can we justify automating it?"
downstream services/ finishing
Ess Tec adds other processes as customers demand. The company deals with larger customers but also works with individual inventors. It has been working with an inventor whose product, marketed as FreedomWand, is made up of multi-components. It is partially molded through two-shot molding and then it is assembled and pad printed in Ess Tec's lab.
This product represents one of Ess Tec's growing markets, that of health care. The tongs on the end of the wand can hold toilet paper, a disposable razor or a bath sponge for people who are physically unable to reach far enough to use such items.
Another segment for Ess Tec is light assembly for automotive and nonautomotive applications. An assembly cell built by local automation supplier Extol Inc., Zeeland, is utilized to assemble molded components for multiple backlit push-button assemblies. Extol's InfraStake technology as well as precision screw driving are used to ensure safe and effective assembly.
In 2002, Ess Tec entered pad printing for use in military compasses. Ess Tec molds the lens and dial and then pad prints the coordinates.
A customer that needed vacuum metallizing prompted Ess Tec to offer that service. The company provides it via partnerships with two companies that specialize in it. At the time, a lot of companies that performed the process were making trophies and not automotive-related parts.
HUMAN RESOURCES: People Matter
Ess Tec has a dedicated employee base of 85. The company uses the philosophy of hiring good people and staying out of their way. In one example, the company hired two key journeymen who used to manage apprenticeship programs at General Motors Co. One man now is maintenance manager, and the other is second-in-command to that maintenance manager.
"I can buy a molding machine. I can call somebody and buy a robot. I can call somebody and buy a dryer. You just can't call someone and get one of these people," Elliot Essenburg says of the importance of finding skilled journeymen.
"Yes, there are headhunters out there that can, but people hold on to these guys. And they can pick and choose. This is a nice place to work. That is why they're here. They're both guys that took early retirement and they're young. So they still want to do stuff, they still want to use their skills."
The men put an apprenticeship program into place that has been a huge boon for Ess Tec, says Davis.
"It brought our maintenance capabilities up a ton," he says. Ess Tec now is a federally certified journeymen industrial maintenance facility. Its first journeyman graduated this year and another is on track to graduate next year.
Elliot Essenburg emphasizes that the company cannot cut corners when dealing with these injection molding machines. Doing things the right way requires highly capable maintenance people.
"You don't buy a level at your local hardware store and level a machine with that," he says. "You need a precision level for it or you'll wipe out the entire clamp end of the molding machine as time goes on." The key is to keep your eye on the ball and hire people who know what they are doing.
"There are a lot of those types of things that, if you pay attention, you talk to Engel and your guys do what they're supposed to do, these are fantastic machines and they will last a really long time."
Angie DeRosa, managing editor
Contact:
Ess Tec Inc., 616-394-0230, www.ess-tec.com
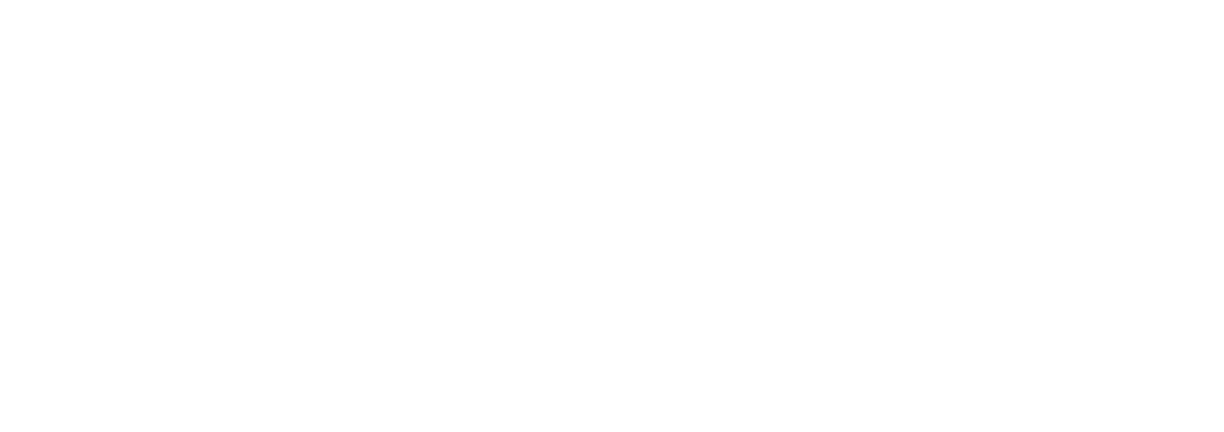