Carbon and partners scaling up to produce 1 million swabs a week for COVID-19 testing
Carbon, a 3-D printer manufacturer, has partnered with a medical device manufacturer to help health-care workers get the testing swabs they need as they battle the coronavirus pandemic.
Carbon has partnered with Resolution Medical, an FDA-registered in-vitro diagnostic and medical device manufacturer, to launch the Resolution Medical Lattice Swab, a 3-D printed nasopharyngeal swab for COVID-19 testing.
Carbon and its laboratory and manufacturing partners are scaling up to produce more than 1 million swabs per week using Carbon Digital Light Synthesis technology and KeySplint Soft Clear material on Carbon M2 printers. The printing material is produced by Keystone Industries.
“Resolving the national shortage of nasopharyngeal testing swabs is critical to the global fight against COVID-19,” said Dr. Ramy Arnaout, associate director of the clinical microbiology laboratories at Beth Israel Deaconess Medical Center in Boston.
Patient testing swabs are critically needed. Expanding the availability of testing supplies and thus testing frequency is vital to helping to curb the pandemic’s spread, according to the companies involved in the partnership.
“We have worked together urgently to get this product into the hands of health-care workers to help address immediate needs for increased COVID-19 testing,” said Shawn Patterson, founder and president of Resolution Medical.
The Resolution Medical Lattice Swab is undergoing clinical evaluation at multiple health care sites, including Beth Israel Deaconess Medical center, a teaching hospital affiliated with Harvard Medical School and Stanford Medicine.
Hundreds of the swabs, which are biocompatible and autoclavable, are printed at a time. Each one has a unique serial number to help track it.
The company, with support from athletic gearmaker Adidas, also is moving forward with efforts to provide protective face shield to health-care workers.
According to an April 8 announcement, Carbon is now producing more than 18,000 face shields each week with an additional capacity to produce more than 50,000 face shields per week across its global network of customers and partners. In addition, Carbon has made its face-shield design freely available on the company’s website, so that anyone with access to a Carbon printer and material can create the shields. The company will update the design as needed.
The face shields have headbands made from a material that Adidas and Carbon used when, in 2017, they launched the first shoe with a high-performance midsole 3-D printed with light and oxygen.
“We worked together to create a highly elastic, tear resistant material called Elastomeric Polyurethane (EPU41) for our 3-Dprinted footwear collaboration,” an Adidas spokesman wrote in an email to Plastics Machinery Magazine.“Now we’ve shifted focus and repurposed this material to create 3-Dprinted faceCarbon encourages hospitals and care providers to submit requests for equipment via its website at www.carbon3d.com/covid19. '
Bruce Geiselman, senior staff reporter
For more information
Carbon Inc., Redwood City, Calif., 650-285-6307, www.carbon3d.com
Bruce Geiselman
Senior Staff Reporter Bruce Geiselman covers extrusion, blow molding, additive manufacturing, automation and end markets including automotive and packaging. He also writes features, including In Other Words and Problem Solved, for Plastics Machinery & Manufacturing, Plastics Recycling and The Journal of Blow Molding. He has extensive experience in daily and magazine journalism.
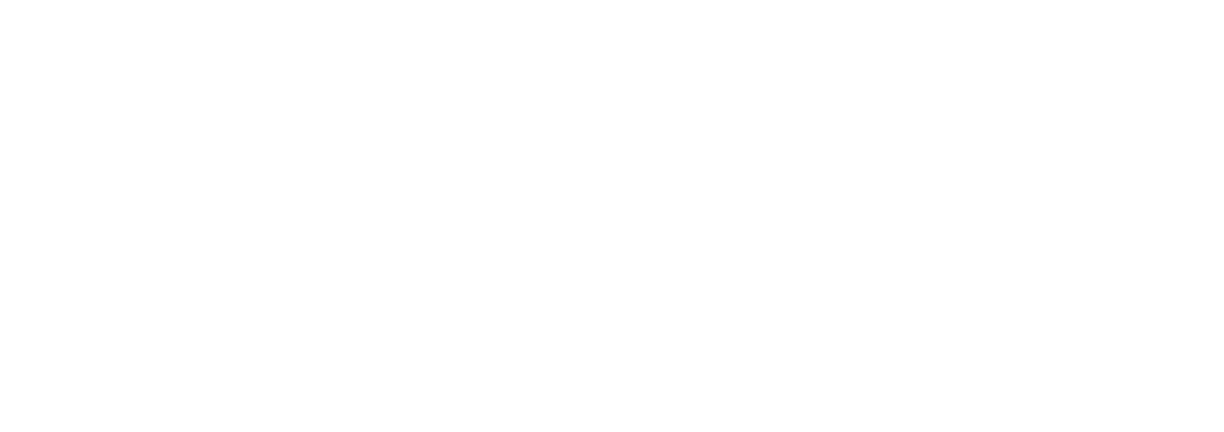