The KHS90EE-39D extruder, with a 90mm screw diameter and a 39:1 L:D ratio, is the latest addition to Kuhne’s family of high-speed Smart Sheets extruders.
It offers greater output and the ability to produce wider sheet than the company’s 70mm and 60mm versions.
The 90mm machine, like the other KHS extruders, features a direct-torque drive and water cooling, and has no gearbox or belt. These design characteristics save energy, and reduce noise and the need for spare parts and maintenance, according to the company.
The machine also has a relatively small footprint.
The KHS90EE-39D extruder is equipped with a 664-horsepower drive and can extrude 5,730 pounds of PS sheet per hour or 4,850 pounds of PP sheet per hour. It also can process ABS.
With its direct-torque drive, the KHS90EE-39D carries a lower price while offering output comparable to the Kuhne K180 extruder, which has a conventional, significantly more expensive drive, according to the company.
“Utilization is much higher as the extruder is much smaller compared to conventional extruders supplying this amount of raw material,” said Thorsten Bung, Kuhne’s director of sales in the U.S., Canada and Mexico.
In addition, color and material changes are faster because the screw turns more quickly than on conventional models, he said.
The KHS90EE-39D extruder, with its larger screw and output, meets a demand from plastics processors who want to produce wider ABS sheets for markets that include the automotive sector and PP or PS food packaging, Bung said.
For example, many ABS sheet manufacturers, such as those making thick sheets for the automotive industry, want to increase their throughput, he said. Because thick sheets require a long cooling section, it often makes sense for manufacturers to increase the width of the product to boost production.
“Let’s say they manufactured sheets with a width of 6.5 feet and a length of 13 feet,” Bung said. “Today, they would look for a width of 13 feet and do a crosscut every 6.5 feet. They change product length into width as length limits line throughput due to cooling time required.” This increases throughput without creating the need for a longer cooling section.
In addition, manufacturers of food packaging may want to go wider to increase throughput, he said.
Bruce Geiselman, senior staff reporter
Contact:
Kuhne Group Sankt Augustin, Germany, 49-2241-902-147,
Bruce Geiselman
Senior Staff Reporter Bruce Geiselman covers extrusion, blow molding, additive manufacturing, automation and end markets including automotive and packaging. He also writes features, including In Other Words and Problem Solved, for Plastics Machinery & Manufacturing, Plastics Recycling and The Journal of Blow Molding. He has extensive experience in daily and magazine journalism.
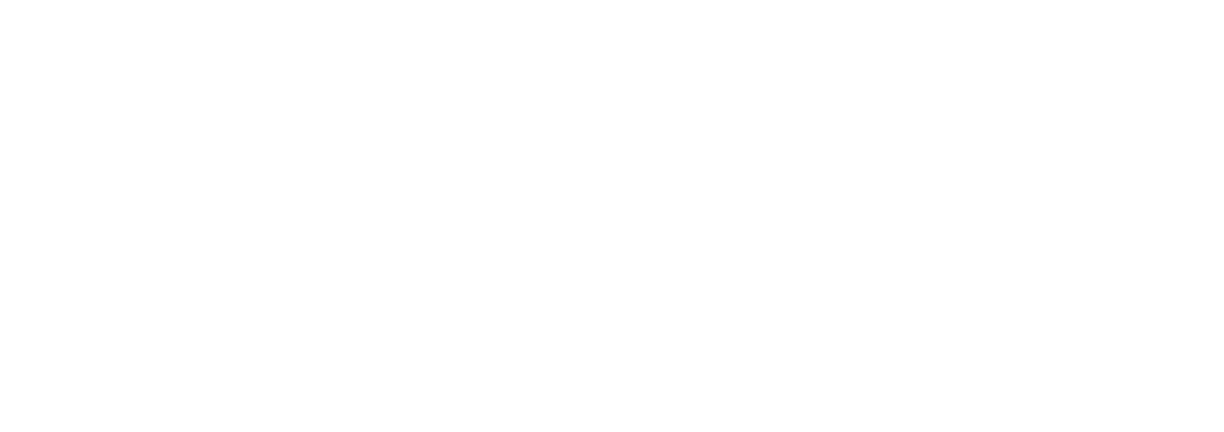