Equipment makers displayed big innovations at a small scale at K 2019, with the latest diminutive equipment including a blown film line from Labtech and a blown film take-off unit from Brabender.
Labtech
The Compact LCF-400 Co-Ex system from Labtech Engineering Co. Ltd., Praksa, Thailand, comes in a five-extruder version for five-layer film, as well as a three-extruder version capable of producing three-layer film.
The bigger line has a maximum output of about 55 pounds per hour, while the smaller line can churn out about 22 pounds per hour. They can produce a 15.7-inch-wide roll with a 13.8-inch lay-flat width.
“All film producers have a small line in their lab where they can run a lot of experiments without having to use their large production lines,” said Labtech President and founder Peter Jurgensen. “It can also be used by companies producing additives, masterbatches, etc., as well as learning institutes.”
The lines include modular, low-boy-type extruders connected to a pancake-type blown film die.
Three of the extruders in the five-extruder setup have 20mm-diameter screws, and two have 25mm extruders. The three-layer setup has 20mm screws; all the extruders, regardless of the version of the line, have a 30:1 L:D ratio. Labtech designs the dies according to customer specifications, including the types of resins that will be used in the line.
A standard line is equipped with a stabilizer cage with Teflon rolls, hard-chromed and rubber haul-off rolls, rubber pull rolls and a surface winder, all of which are mounted over the die assembly on a 360-degree oscillating tower frame.
The lines have a 3-horsepower turbo blower, as well as a dual-channel air-cooling ring that enables high-speed film production.
Polished teak-wood slats guide the film along the collapsing frame.
The tower assembly provides easy access to the die and air ring, and allows motorized adjustments of the tower nip gap, from 8.5 feet to 11.8 feet.
The lines are mounted on a sturdy steel foundation equipped with casters and leveling bolts for easy positioning. The foundation covers most of the system’s electrical cables, hoses and air conduits.
A 15-inch touch-screen control panel also is included.
In the U.S., Labtech has several regional representatives, including Milabtech LLC.
Brabender
A new blown film take-off unit from Brabender designed for laboratory use represents several improvements over a previously introduced model. Used in combination with a Brabender lab extruder and blown film die head, it can perform simultaneous inflation, cooling, flattening, take-off and winding of an extruded film tube. Unlike an earlier model, it can be used with coextruders.
Polymer exits the extruder through an annular die and is blown into a bubble. The bubble is guided upward by the film-width control unit, then flattened by collapsing frames and taken off by nip rolls. This film is guided over the pulley and the guide rollers to the winder, which produces the finished film rolls.
“It’s used for sample testing material to make a small, long film like a bag and to research material quality, strength, visibility [appearance] and aesthetics,” said Paul Nardone, Brabender’s North American sales manager. “Rather than go into the large, large blown film lines and taking up time from production machines, they can run a small sample on one of our extruders and make a very small bag to film-test.”
According to Nardone, the previous take-off unit was limited to single-layer film production. The new unit, which replaces it, has a cantilevered tower that allows for height adjustment. It also handles film at a faster speed of up to 80 feet per minute. An optional ultrasonic measuring system can control flattened film width.
Brabender’s laboratory extruders can be used for testing the processing behavior of new recipes or incoming materials, final material inspection and quality control during production.
The new unit works with Brabender’s new MetaBridge software for more user-friendly control. Using a touch screen with MetaBridge, operators can more precisely set parameters such as working height, winding torque and settings for cooling air.
Bruce Geiselman, senior staff reporter
[email protected]
Contact:
C.W. Brabender Instruments Inc., South Hackensack, N.J., 201-343-8425, www.cwbrabender.com
Milabtech LLC, Fenton, Mich., 810-516-1700, www.labtechengineering.com, www.milabtech.com
Bruce Geiselman
Senior Staff Reporter Bruce Geiselman covers extrusion, blow molding, additive manufacturing, automation and end markets including automotive and packaging. He also writes features, including In Other Words and Problem Solved, for Plastics Machinery & Manufacturing, Plastics Recycling and The Journal of Blow Molding. He has extensive experience in daily and magazine journalism.
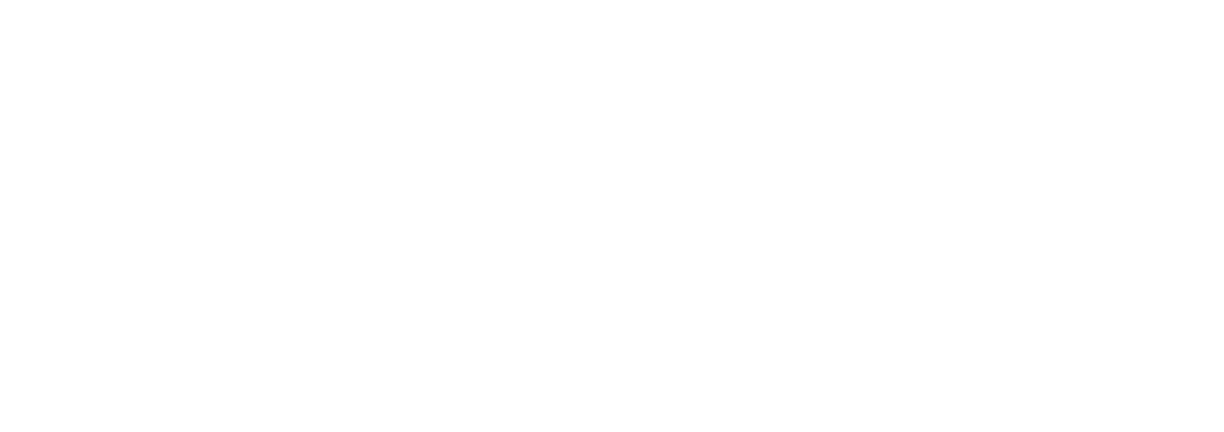