Founded in 1978, Macro manufactures lines for blown film, cast film and biaxially oriented films with up to 13 layers. The company also supplies sheet extrusion lines for specialty applications, along with extrusion coating and laminating lines. Planeta, 73, retired from the company on June 14. He discussed his career with Plastics Machinery Magazine senior staff reporter Bruce Adams.
When were you exposed to the plastics industry?
Planeta: My dad was a manager for a large plastic company in Czechoslovakia. I was a 15- or 16-year-old student when I worked in the summer at the plastics factory. I worked running extrusion lines and troubleshooting extruders. The plastics industry was not so developed then. Companies did everything on their own, including making their own equipment.
Did you initially stick with plastics?
Planeta: No. My dad was a mechanical engineer, and he wanted me to be one. I liked chemistry, and we had a chemical company nearby. At that time, they were throwing what they didn’t need in a dump outside. I would collect chemicals I needed from the dump. When I was in high school, I had a complete chemistry lab at home. I decided to study rocket propellants and was making rockets. At the time in the 1960s, the Russians had Sputnik. I worked with a colleague, and we had a couple of explosions in my lab. We did not have enough experience to be safe. I was not patient enough to do it properly. I decided it was safer to study plastics than rocket propellants.
How did you get from your lab in Czechoslovakia to founding Macro?
What was the initial focus for your company?
Planeta: When I started Macro Engineering, most of the job was in woven plastics for a packaging company that made plastic bags. I did engineering and design for folding and packaging the plastic bags. The first two years, that was most of my job. The air-ring development started later. Most of my time I spent improving blown film, binding and folding. Then, we went out of the molding business and more into processing. I built the first blown film line in 1986.
What are some innovations that Macro has developed?
Planeta: Macro is very good in double-bubble biaxial films and blown film lines and cast film lines. The double bubble is one of the best technologies in the world. It was developed at Macro Engineering. We developed it in 1998 and worked about two years to perfect it. Double bubble makes shrink film. It is used primarily to package cheese and meat. We made the machine, not the film. We’d sell the machines and the technology on how to make it and the recipe to use to make it. We called it a total solution because we provided the line and the recipes. We had three guys with Ph.D.s in polymers. They would develop the polymer structure. It continues to be very popular today. Biaxial and monoaxial become more popular. It gets stronger, and you can use less. The film gets stronger and stiffer, and it gets better barrier properties. Once you orient the crystals, they don’t let the oxygen or oils through.
What are the biggest extruder advancements that you’ve seen?
Planeta: In blown film, it was the development of multi-orifice air rings, because they greatly improved the output. Screw die air-ring improvement was a big jump. You could cut the price drastically because you were running at such a high output. You could get better quality and better mixing. Screw improvement with the barrier screw and cooling improvements, including air ring and IBC [Internal Bubble Cooling], were the biggest jumps in the plastic industry because you would improve your efficiency by about four times.
What major challenges did you encounter as your business grew?
Planeta: When I started the business in Canada, there were not enough people who were experienced in the plastics industry. We started the business, and later we faced the challenge when we were making custom machinery. Custom-building the machinery was the biggest challenge. You need the best people that you can get to custom-build machinery.
What are some of the most important milestones for Macro?
Planeta: The biggest milestone was when we decided to concentrate on engineering and not so much on production. Initially, we had big machine shops and we concentrated on production. The problem with the production is that now with the special machines, you need different machines and tools. Your effort is 80 percent in production and 20 percent in engineering. We wanted to reverse that, so we decided to concentrate on the engineering. That was a big challenge. We did the assembly, troubleshooting, development and engineering inside. Most of the manufacturing was done outside. Now, Macro went back to more manufacturing. They have several big CNC machines and make dies and other critical parts.
To what do you attribute your company’s success?
Planeta: Working with the people. We always had excellent relationships with everybody. At one point, we had 13 nationalities by birth working at the company. They are Canadians now. Everybody worked as a team. We never had a problem. Everybody adopted the philosophy of the company and worked together. In engineering, we had many nationalities. But there never were any issues. Diversity was a strength of the company.
What do you see as the next phase of development or machine automation in extrusion machinery?
Planeta: Computerization, artificial intelligence and the automation of the factory is what I see as the biggest change. You will see complete handling systems. More automatic systems to bring the material out. You will have complete automation of material mixing where you program the computer and get what you want. The rail car comes in with material and everything goes to the right silos and the operator doesn’t have to do anything, just program the recipe in the computer and it comes out.
Companies want to change from making one product to another in 10 minutes instead of one hour. More things will be done automatically. You will need more engineers to design equipment than you will need people to work simple jobs. The simple jobs will be given to robots. There is no question that will happen. It already is happening in the automotive industry. More automation in production also solves work rules for lifting or for working too many hours. Robots work 24 hours a day.
In extrusion lines, startup and exchanging the material will be automated, as well as watching all the parameters of the lines. You will have much more of this because computers are so cheap. Computers will learn on their own what the temperature, humidity and viscosity need to be. It will be fully automated in 10 years. Computer usage will be everywhere because computers and memory are becoming cheap.
What is your view of sustainability and the circular economy?
Planeta: We must have plastic packaging to preserve food, but we cannot infinitely pollute our planet. The problem comes from developing countries that dump their waste into the sea. Ninety-five percent of plastic waste in the ocean comes from developing countries. Developed countries have to realize that shipping plastic waste to developing countries solves nothing because they throw it in the sea. We have to start reprocessing plastic ourselves.
Plastic can be processed or biodegraded, but it depends on the will of the people and the cost. We developed biodegradable foam, but it was more expensive by about 20 cents per pound and the customer did not want to pay for it. Government must regulate the change and do it collectively so everybody will be exposed to the same cost. People won’t pay more money to protect the environment unless they have to. Almost every plastic, including foam, can be made biodegradable. But it costs more. Or you can burn plastic to create energy. We must put our money where our mouth is, or nothing will change. Society has to solve the problem. It’s past the time to put your head in the sand and pretend there is no problem.
What are you doing in retirement?
Planeta: I am helping companies now for free with recycling plastic and making plastic biodegradable. The circular economy is my worry. We are not going in the right direction. I would like to change it. Now, we are doing solutions that look good, but don’t solve the problem. I work on recycling. How do we make it recyclable? How do we make it work with all the mixed plastics? I work with private companies on the development side and with government on implementing workable solutions.
How would you like to be remembered?
Planeta: As a good person. When I retired, I told everybody my biggest achievement was I had people from all over the world working together happily as a team. Enjoy what you are doing at work because you spend a lot of time there.
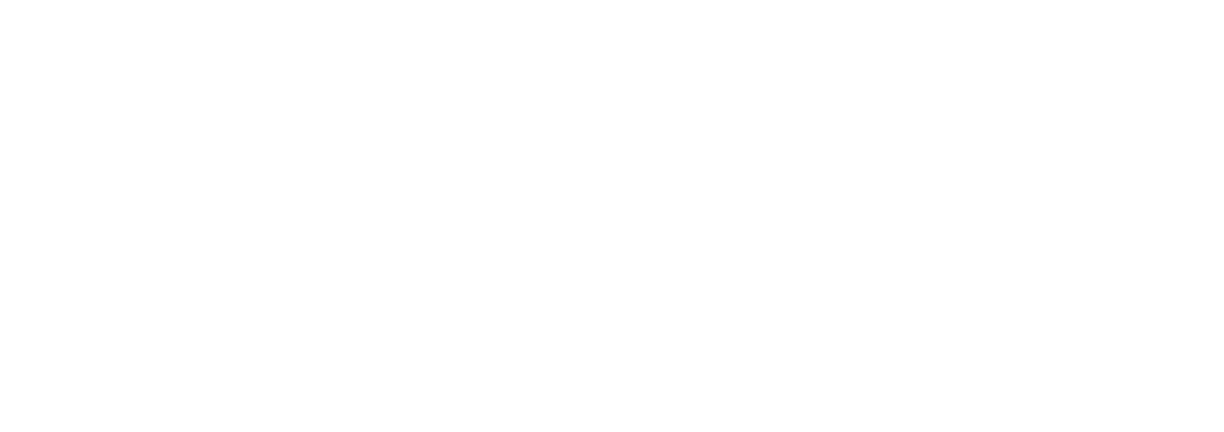