Static charges can build up during plastics manufacturing processes, causing machines to jam, parts to stick to each other and contamination to adhere to part surfaces. Equipment that eliminates static — or harnesses its power for holding products in place — can play an important role in part quality, worker safety and other surface treatment processes.
SIMCO-ION
“Materials are becoming increasingly thin and sensitive, while processes are becoming faster and leaner,” said Suzanne Serveiss, marketing manager for Simco-The company’s new, wide-format ionizing blower neutralizes static during the manufacture of various plastic products, including film, from up to 20 feet away. The IQ Power Fantom features an air outlet 20 inches wide and a blower that moves 600 cubic feet of air per minute for an effective coverage area of 2 feet by 20 feet.
“The IQ Power Fantom ionizing blower has the same static-eliminating capabilities as a static neutralizing bar … and is generally chosen when mounting a bar in close proximity [to the product] is not possible. Additionally, it works well for moving parts and 3-D parts, turret winders and in situations where there are piles or collected bins of objects,” Serveiss said.
The IQ Power Fantom has Industry 4.0 capabilities and comes from the factory ready to operate in fixed mode. It also has three specialized modes that are available when the blower is connected to the optional IQ power control station controller. The system’s manual narrow mode allows the user to fine-tune the ion output, while its manual wide mode provides bulk static elimination for products that are highly charged and moving quickly. In closed-loop feedback mode, the blower works in conjunction with an IQ Power sensor bar and continually adjusts the ion output based on current operating conditions.
Connecting to the IQ power control station is especially useful for turning the device on and off if it is mounted out of reach for manual operation.
The device has various mounting options and comes in 120-volt and 230-volt versions. It has a self-cleaning system for simple maintenance, and its ionizer/duct assembly can be easily replaced.
MEECH STATIC ELIMINATORS USA
Some processes benefit by adding static. This is the idea behind Meech’s new Hyperion IonCharge 30 and IonCharge 50. Slated for display at K 2019 this month, the IonCharge models are static-generation systems that are primarily for film. “A static charge can improve web handling, winding and fabrication,” GM Matt Fyffe said. The numbers refer to the systems’ power-generation capabilities: 30 kilovolts (kV) and 50 kV.
Static can help with sealing a web so there are no air pockets, which assures tight, even rolls after processing; improving lamination of layers; and creating crisp folds in gusseted bags. Fyffe said the device also can be used to charge a film winding core so that the film adheres to it without adhesives.
The IonCharge mounts at or near the end of a film line. Multiple sizes are available in the two kV ranges. Sizes run from a 2-inch-diameter nozzle to a 9.8-foot-wide horizontal bar. Despite the ability to generate up to 50 kV, amperage is low, so operators are not exposed to shock hazards, Fyffe said.
At K 2019, Meech also plans to show a long-range ionizing bar for film and solid parts called the Hyperion 960IPS. The unit produces 24 volts of pulsed direct current, which generates ions over distances of 6 inches to 3 feet, Fyffe said. Treatment widths run to 13 feet. IPS stands for internal power supply.
The Hyperion 960IPS generates extremely powerful ionization of up to 15 kV and provides 50 percent greater maximum working distance than a previous ionizing bar, the 929IPS. Fyffe said the Hyperion 960IPS uses pulsed DC technology to deposit ions on products — no air is in the mix. “Air can blow dust and debris onto products, and oil and moisture,” he said. The unit has adjustable voltage, frequency and balance, making it suitable for a range of applications.
The Hyperion 960IPS handles web speeds of up to 1,500 feet per minute. It can be mounted near the end of a film line to treat a web, over a conveyor belt for solid parts or on a benchtop.
EXAIR
Exair’s product range includes ion air systems that eliminate static charges on plastic surfaces. “Our target is any process where non-conductive materials experience issues with a surface-level static charge,” said application engineer Brian Farno.
Offerings include the Gen4 static eliminator line, which comprises eight products. The devices can treat areas from 3 inches to 4 feet wide and eliminate dirt and contaminants, as well as static.
The latest addition to the line is the Super Ion Air Wipe, a circular device that attaches to a processing machine and envelops parts moving through it in a 360-degree flow of ionized air. Available in 2- and 4-inch diameters, the Super Ion Air Wipe processes hose, pipe, wire and cable extrusions and 2-D and 3-D profiles. Two ionizing points powered by a 5-kV generator fill the airstream with the static-elimination ions that attach to part surfaces. The units run on 115- or 230-volt power supplies.
Pat Toensmeier, correspondent
Kathy Hayes, copy editor
Contact:
Exair Corp.,
Cincinnati, 513-671-3322, www.exair.com
Meech Static Eliminators USA Inc.,
Akron, Ohio, 330-564-2000, www.meech.com
Simco-Ion Industrial Group,
Hatfield, Pa., 215-822-6401, www.simco-ion.com
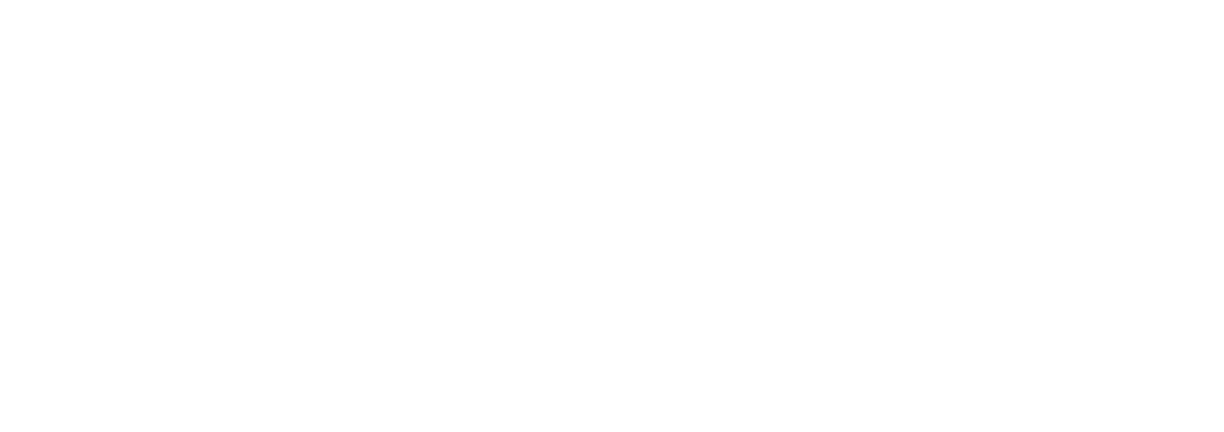