New predictive maintenance options are giving extrusion manufacturers a sense of what's happening under the hood — all without the need for downtime. From monitors and sensors that check the oil to full-blown systems that oversee the machine stem to stern, options are available that give users the chance to optimize production and avoid unplanned stoppages.
DAVIS-STANDARD
Davis-Standard's new DS Activ-Check system provides continuous monitoring of new extruders.
The smart technology is available as an option on Davis-Standard's Integrator, Epic III and DS-eVue control systems. Customers who choose to purchase the Activ-Check option at an additional cost receive an extruder equipped with a suite of sensors.
"It's available on any type of [Davis-Standard] extruder," John Clemens, the company's director of extrusion controls, said. "We are working on an aftermarket package that could be put on older machines, but we're not there yet. It is a goal."
Activ-Check provides processors with early notifications of potential extruder failures. That allows them to practice predictive maintenance and reduce unplanned downtime.
Activ-Check sends customers notifications by email or text message. In addition, authorized employees can monitor the status of an extruder on smart devices and remote computers. The system monitors the condition of the extruder reducer, lubrication system, motor, drive power unit and barrel assembly.
In addition to the automated remote messaging and monitoring, readouts on extruder HMIs can deliver warnings, and an overview screen for Activ-Check offers a cutaway picture of the gearbox and the reducer section. It displays data collected by sensors in real time. It also can display trends and graphics based on measurements.
Activ-Check provides a combination of predictive and preventive maintenance suggestions.
"Some of that is based on actual sensor readings, and some of it is based on running hours of the machine," Clemens said. "There are a couple of things we look at to predict a potential failure or what should be a planned maintenance activity."
The system not only can predict future equipment failures, it reduces the burden on processors to keep track of planned maintenance schedules.
"It makes it more automated, where we are alerting them," Clemens said. "It reduces their need to remember to perform the maintenance."
The Activ-Check system helps processors plan production around scheduled maintenance activities, he said.
"This technology will also allow customers to address a pending condition that could become a more serious issue in the future," Clemens said.
Vibration sensors on the extruder reducer provide data regarding the condition of the gears, bearings and lubrication system. Sensors monitor the extruder motor's temperature and vibrations. The reducer lubrication system includes pressure, flow and temperature sensors. Operators also can monitor key health indicators in the drive power unit.
If processors don't address alerts, the system will eventually send messages warning that "failure is imminent," he said.
CPM CENTURY EXTRUSION
CPM Century Extrusion offers several options for purchasers of its extruders interested in predictive maintenance. They range from a simple oil-condition monitor to the latest smart technology for CXE extruders introduced at NPE2018.
"We have been working with the gearbox vendors on what we can offer our customers to be able to a certain extent to predict when a failure is coming or when a rebuild is going to be necessary," said Janik Bessinger, CPM's head of engineering.
As an option, CPM offers extruders with gearboxes from Eisenbeiss that include the company's GearControl-Oil sensors. The sensors are submerged in oil and monitor its condition. The system has recently been updated.
"It monitors things like temperature and moisture content of the oil," Bessinger said. "It tells you the status of the oil."
The sensor measures impurities, soot formation, air content and acidification. It also keeps track of the age of the oil. Users can configure the thresholds for warning alarms.
Eisenbeiss offers its own simple controller that conveys the condition of the oil, Bessinger said. Users can immediately see oil condition by pushing a button on the face of the sensor, or they can use a laptop to connect to the sensor and download data on the key parameters that are measured.
Workers can either analyze the data themselves or send it to Eisenbeiss for analysis.
CPM has offered the option for several years, but about a year ago it began offering a more advanced Eisenbeiss product called i:Gear 4.0.
"I:Gear is an integrated condition-monitoring system for their gearboxes, and it can be fitted on most gearboxes," Bessinger said. "It uses accelerometers across the gearbox. They have their own controller and platform where they gather and process the data. You can put it online, and they can access the data whenever you want them to look at it. They can tell you the status of the gearbox and if everything is in good condition."
I:Gear 4.0 is capable of measuring oil condition; torque; speed; oil level, pressure and temperature; and filter status; as well as bearing and gear condition. Using a multi-parameter analysis, it detects fault conditions, such as improper viscosity or, in the case of force-fed lubrication, low flow. It comes with a stack light that indicates the condition of the gearbox. The controller the company provides offers a web interface that can be accessed via Ethernet to display the gearbox condition and indications in detail. A block diagram highlights the corresponding parts in case of alarm conditions.
In addition to the oil-monitoring technology, CPM now offers smart extruders with monitoring systems as a subset of its CXE line of extruders.
Known as the sHO series, or smart High Output series, the new smart multi-screw extruders offer a wide array of smart features.
"We install accelerometers all along the machines in critical positions," Bessinger said. "We trend the data over time and look for sudden increases in vibrations that we can say need to be looked at to determine what is going on with the machine."
The smart extruder package includes Eisenbeiss GearControl-Oil sensors to monitor oil condition, as well as measurement technology to monitor the torque of each shaft.
Since few systems measure the torque on each shaft independently, if a problem develops with only one shaft, other systems might not catch the problem in time to prevent machine damage, he said.
The extruders have energy-monitoring technology that allows processors to adjust certain parameters in their manufacturing process to see if they consume less energy.
"That is the beauty of being able to look at everything as a whole," Bessinger said.
AMERICAN KUHNE
American Kuhne is building new, standard input/output (I/O) diagnostics into the Navigator control systems for its extruders.
The diagnostics allow users to see the status of electrical system inputs and outputs in real time without having to open the electrical enclosure, the company said. Graphics displayed on the HMI match what the user would see inside the cabinet — the status of limit switches, transducers, e-stops and variable-frequency drives.
American Kuhne also introduced a monitoring and alert system for panel temperature. A thermocouple in every electrical enclosure monitors the panel temperature and triggers an alarm if temperatures exceed a predetermined level. The alarms could notify users of a problem, such as a clogged filter or the failure of a cooling system or fan, and help them diagnose and correct the problem prior to a system failure, according to the company.
American Kuhne extruders and extrusion systems also provide integrated documentation via the HMI. The operator's manual, maintenance manual, commercial documents, electrical and mechanical drawings and lists of spare parts are at the operator's fingertips, accessible by touch screen.
Bruce Geiselman, senior staff reporter
Contact:
American Kuhne, York, Pa., 717-848-3755, www.americankuhne.com
CPM Century Extrusion,
Traverse City, Mich., 231-947-6400,www.cpmextrusiongroup.com
Davis-Standard LLC,
Pawcatuck, Conn., 860-599-1010,www.davis-standard.com
Bruce Geiselman
Senior Staff Reporter Bruce Geiselman covers extrusion, blow molding, additive manufacturing, automation and end markets including automotive and packaging. He also writes features, including In Other Words and Problem Solved, for Plastics Machinery & Manufacturing, Plastics Recycling and The Journal of Blow Molding. He has extensive experience in daily and magazine journalism.
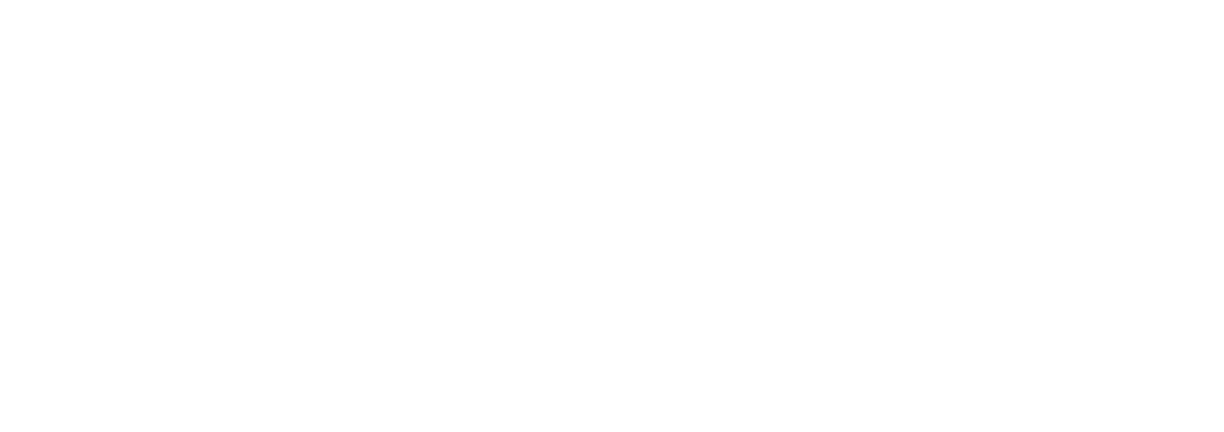