By Bruce Geiselman
Processing temperature-sensitive PVC creates special challenges for compounders, so Buss now offers a new configuration of its Compeo compounders designed to limit shear and the buildup of hydrochloric acid.
The discharge and pelletizing units of the new Compeo units are decoupled from the compounder, and the melt exiting the extruder falls freely through a connecting metal chute into a discharge unit. From there, it is fed through a pelletizer.
Buss launched sales of the new PVC configuration, which it calls a “cascade design,” more than two years after highlighting its first Compeo compounder at NPE2018.
The chute that connects the compounder to the discharge unit contains a degassing unit. The connection chute features a vacuum port, where a vacuum pump and trap can be attached. This eliminates the need for a degassing module, which shortens the compounder’s processing section and reduces the residence time of the PVC.
A viewing window built into the chute allows the operator to watch for potential fill up of the chute should the compounder provide more material than the discharge unit can take. Also, a temperature sensor in the connecting tube can alert an operator as the tube is filled.
The design generates pressure for pelletizing with a single screw discharge unit arranged at a 90-degree angle from the compounder. The discharge extruder is designed in 4 L/D or 6 L/d versions, depending on the pressure build-up requirements. The discharge extruder screw is water-tempered while the discharge extruder housing is electrically heated and air-cooled.
Depending on process requirements, the die-faced pelletizingThe die plate, which permits visual monitoring of the pelletizing process, is equipped with a pressure sensor that activates an automatic safety shutdown if the maximum permissible pressure is exceeded. A braked motor ensures that the knife drive is locked securely. The knife arm is equipped with a stand-still monitor. Access to the pelletizing area is possible only when the system is in a secured state.
The special configuration provides precise temperature control.
“While PVC is a particularly versatile, robust, tough and durable polymer, it also posts some very unique processing challenges,” said Dino Kudro, head of design and engineering for Buss AG. “Particularly, its tendency to degrade and expel hydrochloric acid (HCL) under excessive thermal or mechanical stress is what makes this polymer’s processing demands unique. Not only does HCL cause excessive corrosion to metal components in contact with the polymer, it also acts as a catalyst for further degradation of the polymer and causes a deterioration of the polymer’s mechanical and visual properties. To avoid the degradation of PVC and subsequent formation of HCL, the shear rates and melt temperatures must be carefully controlled. Local shear peaks, stagnation zones or hot spots must be avoided.”
By minimizing the residence time of PVC within the extruder, Buss’ design prevents the buildup of HCL. According to Kudro, PVC has a tendency to stagnate near the tips of extruder screws, as well as in indentations and gaps and screws.
The PVC configuration is available on all Compeo compounders, including Models 55, 88, 110,137 and 176. The model numbers represent the compounder’s screw diameter in millimeters.
Bruce Geiselman, senior staff reporter
Contact:
Buss Inc. USA, Carol Stream, Ill., 630-933-9100,www.busscorp.com
Bruce Geiselman
Senior Staff Reporter Bruce Geiselman covers extrusion, blow molding, additive manufacturing, automation and end markets including automotive and packaging. He also writes features, including In Other Words and Problem Solved, for Plastics Machinery & Manufacturing, Plastics Recycling and The Journal of Blow Molding. He has extensive experience in daily and magazine journalism.
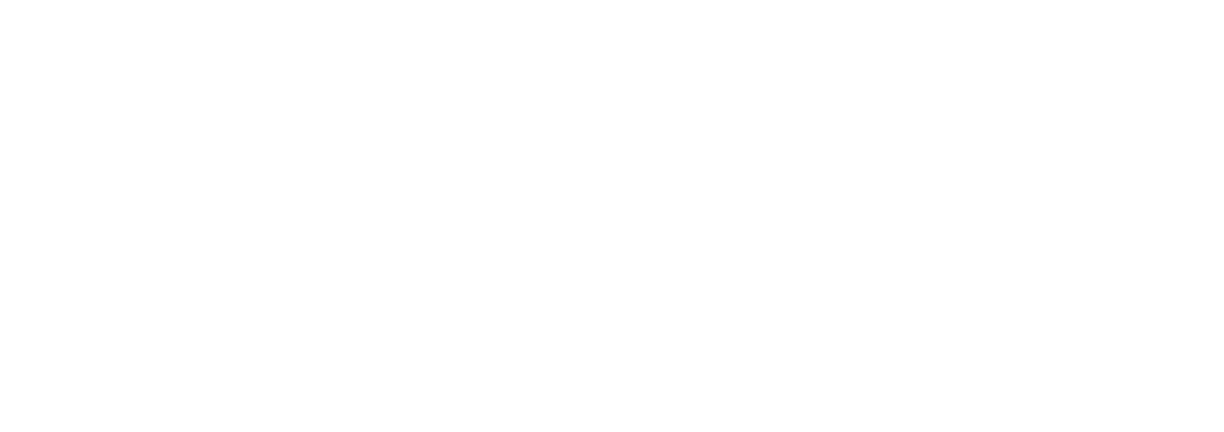