The maker of a piece of machinery originally created in 1961 to mix epoxy keeps finding new ways to reinvent the technology. Readco Kurimoto’s continuous processors combine multiple dry or liquid materials and then discharge a homogenous mixture. The company has found its way into new industries, and the machines have been used in the food, chemical and pharmaceutical sectors, as well as plastics.
David Sieglitz, president of Readco Kurimoto, said his company’s machines have processed resins such as HDPE, LDPE and PVC to increase their thermal, physical and mechanical properties. The machines mix in fillers and colorants.
“We’ve shown customers how, by separating the mixing in the continuous processor, and the extrusion in a standard extruder, we can actually increase the quality and also the throughput,” he said. “As long as we have control of our feeds, and we’re consistently feeding in the materials, we get rid of that batch-to-batch variation, and the consistency in our machine, the color match is spot on.”
While continuous processors share some features in common with extruders — they can accept material from hoppers or loss-in-weight feeders; they have twin, co-rotating shafts; they have a heated barrel; they can melt resins with a combination of heat and shear — they don’t operate at high pressure, and are available for approximately half the price of an extruder. The screw or paddle sections can be tailored to meet the mixing, kneading or shearing requirements of specific materials.
The continuous processors mix very efficiently and can be configured to complete all the mixing and compounding steps close to the barrel’s input end, then add the color through a vent port near the end of the process. “If it’s heat-sensitive, due to volatiles or anything like that … we can add the colorant right at the end of the machine, mix that in homogenously, but actually be able to reduce the amount of pigment that’s necessary to get that brightness that they’re looking for, to get that color match,” Sieglitz said.
“The other thing is if there’s [a] high level of fillers. So, if someone’s trying to put in fiberglass, carbon fibers, anything like that, we can get an extremely high level of fill compared to an extruder.” Other applicable fillers could include fire retardants, silica, titanium dioxide and calcium carbonate. “We can also incorporate that without breaking ... the strands. Once again, we add that after we do all the compounding at the very end, and just gently fold it in and get a homogenous product coming out.”
Sieglitz said prospective customers can pay Readco to conduct what is usually a two- to three-day test in Readco’s lab. Readco works with the customer to review its current process and formulation, and then refines the mix of paddles and screw elements to achieve the desired results.
Sieglitz said his company also rents continuous processors. “A lot of times customers will … rent one to either do further development, to prove this out in the company, or sometimes as a stopgap measure, as well. They can rent one of our machines as we’re building their machine to their specific needs and requirements.”
Continuous processors are also simple to clean. They are available in single- and double- clamshell designs, which allows the top or the top and bottom halves of the barrel to open away from the screws. This gives operators unobstructed access to the interior of the barrel for thorough cleaning or inspection.
David Tillett, copy editor
Contact
Readco Kurimoto LLC, York, Pa., 717-848-2801, www.readco.com
David Tillett
Associate Editor David Tillett writes and edits for Plastics Machinery & Manufacturing, Plastics Recycling and The Journal of Blow Molding. He covers new products, industry news, patents and consumer and business equipment. He has more than 20 years of experience in daily newspaper, online and magazine journalism.
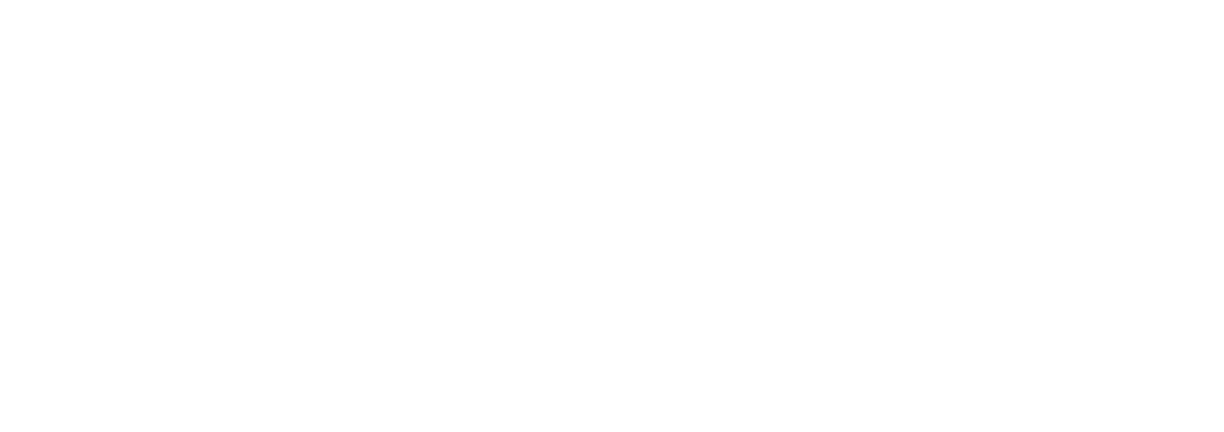