Emphasizing the role its equipment can play in a circular economy, Bekum America is rolling out a redesigned Hyblow 607D three-layer blow molding machine that will be manufactured in the U.S.
During a Sept. 30 open house in Williamston, Mich., the company will showcase the ability of the machine to boost the use of post-consumer resin, thanks to Bekum’s three-layer extrusion technology that allows recycled material to be embedded between layers of virgin plastic.
The open house coincides with Bekum America’s recent expansion, which added 40,000 square feet of manufacturing and office space to its 115,000-square-foot facility.
The redesigned Hyblow 607D features a sleeker appearance that is characterized by a modern color and shape, improved functionality and ergonomics, and large, lightly tinted viewing panels, the company said.
“We’ve adopted a new design standard in terms of the looks and appearance of our machines,” said Gary Carr, VP of sales. “It looks really good and sharp.”
Bekum America’s parent, headquartered in Berlin, introduced the new design at K 2019 in Düsseldorf, Germany, and began incorporating it on machines produced in Europe, but this will be the first U.S.-built Bekum blow molding machine with the new design, Carr said.
While the Hyblow 607D at the open house will be a hybrid electric model, the machine also will be available in all-electric and hydraulic versions, Carr said.
The redesigned machine also will have a control manufactured by Beckhoff, Carr said. The Bekum Control 8.0 reduces the number of switching elements on the control panel and simplifies machine handling by means of intuitive menu navigation, according to the company.
“The HMI is incredibly intuitive, with minimal screens for machine operation,” Carr said. “The operator station is kind of like in a Tesla car — we’ve got a big portrait 24-inch high-resolution screen for machine control.”
The machine demonstrated at the factory will be configured to produce three-layer HDPE bottles with post-consumer regrind in the middle layer.
“The three-layer HDPE will be run with the intent to maximize post-consumer regrind in the middle layer with a thin color outer layer and a very thin inner product protective layer,” Carr said. “What Bekum is demonstrating is the latest spiral blow-head technology. Spiral blow produces extremely uniform circumferential wall distribution, which allows them to run the layers at their thinnest potential.”
That means bottle producers can maximize the inner layer of regrind while producing extremely thin inner and outer layers of virgin HDPE.
“The thinner you can run the inner and outer layers, the more PCR you can load in the middle, which is good from a sustainability standpoint.”
The demonstration machine will be running with an HDPE developed by ExxonMobil Chemical Co. for the inner and outer layers. The company’s Paxon SP5504 is ideal for use with a PCR middle layer, Carr said. It offers environmental stress crack resistance, which compensates for the tendency of PCR in the middle layer to crack under stress, Carr said.
“We worked directly with ExxonMobil on some of the early blow moldability trials, and that product was just commercialized this year specifically for high-load PCR,” Carr said.
The demonstration machine will be a two-parison, four-cavity configuration producing 10-liter F-style agricultural chemical bottles that will offer a performance equivalent to all-virgin plastic bottles.
The Hyblow 607D is a double-sided shuttle machine with two 27-ton clamps. The nominal output of the four-cavity Hyblow 607D is 600 bottles per hour of 10 Liter F-style containers at 350 grams, Carr said.
Bruce Geiselman, senior staff reporter
Contact:
Bekum America Corp., Williamston, Mich., 517-655-4331, www.bekumamerica.com
Bruce Geiselman
Senior Staff Reporter Bruce Geiselman covers extrusion, blow molding, additive manufacturing, automation and end markets including automotive and packaging. He also writes features, including In Other Words and Problem Solved, for Plastics Machinery & Manufacturing, Plastics Recycling and The Journal of Blow Molding. He has extensive experience in daily and magazine journalism.
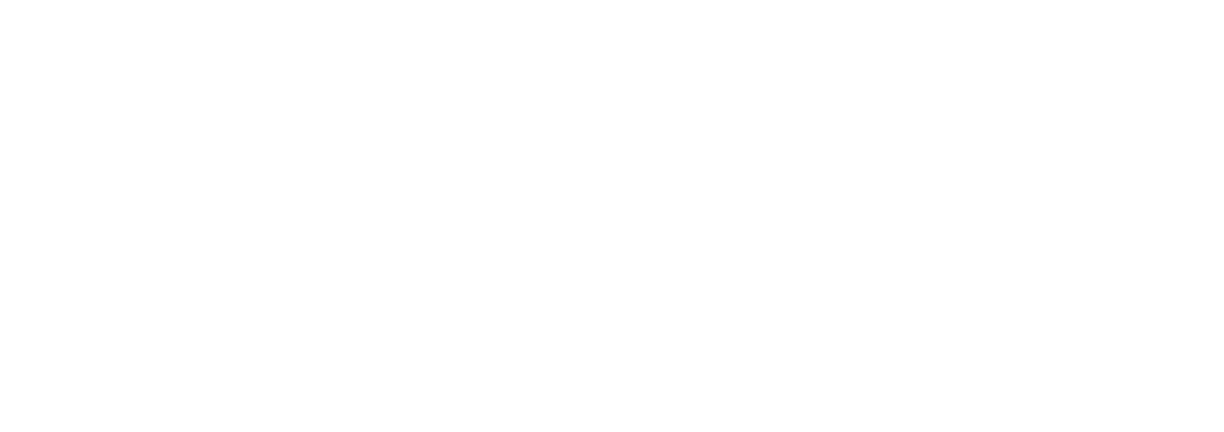