Integrating the right leak inspection system in your blow molding line can save money
By Andrew Steiner
ALPS Inspection
If you oversee a line that produces containers, you are focused on producing as many usable containers as possible while minimizing scrap production. Each delay and unfit container eats into your valuable profit margin.
Many assume that leak inspection equipment is capital that provides no measurable return on investment, but the right leak inspection strategy can increase your margin by reducing scrap and keeping your operation online as much as possible. This ultimately differentiates you as a manufacturer and empowers you to win and retain more business.
How errors sneak into your production process
Preparing a production line to manufacture a new container is an exhaustive process, from laying out the new line, to determining which equipment will perform best based on the bottle specifications, to ramping up your production with as few errors as possible.
If you can accomplish all of that without error, you are in great shape.
But several barriers can prevent you from achieving your goal of producing usable containers while minimizing scrap production.
Production delays
- For manufacturers of all types, unpredictable and unresolved maintenance issues lead to excessive downtime. If the post-sale support for your equipment is not quick to respond, your downtime will grow.
- Production line jams can also create excessive scrap production, as well as downtime.
- For firms that manufacture different kinds of containers, slow changeovers and inflexible equipment also create delays in your process, not to mention the additional personnel costs and risk of changeover accuracy.
- Human error causes 23 percent of unplanned downtime in manufacturing. That’s 2.5 times higher than in other sectors, according to a 2017 study by market research firm Vanson Bourne. (source)
False rejects and false positives
- Assuming your production line functions properly and is supported appropriately, your next barrier has to do with quality issues. These can be devastating to a client relationship, so proper protection is a critical part of your production process.
- At the same time, if leak inspection equipment is improperly configured, you could be rejecting good containers.
All of these issues ultimately eat into your profit margins and result in lost revenue.
What causes errors in your production process?
When errors arise, they may indicate a glitch in the quality assurance process.
While having leak inspection equipment is a great starting point to preventing manufacturing errors, there are several components that can affect your overall success.
Improper equipment selection and configuration for your process
Configuring your inspection equipment to your manufacturing equipment and process is the first critical step. Certain equipment works better together, and different containers and quality thresholds require different testing protocols and calibration. If you’re using the wrong equipment or don’t have it properly calibrated, your process could be offline before it ever starts.
Take it from ALPS Inspection Business Development Manager Dan Caverly: “If you are producing bottles on a two-step machine — my mind shifts directly to our rotary platform and our available value-add options like additional gate inspection sensitivity, being these are fast, high-output PET machines.
“If a converter says they are manufacturing via extrusion, I know that speeds will be much slower, but they probably run several HDPE bottles and would value flexibility and a different set of options, like inclusion inspection, versus the company or application using a two-step PET blow molding process.
“Having multiple leak detection platforms and options allows ALPS Inspection to recommend the correct leak detector for not only the bottle application(s) at hand, but also the big picture around the blow molding platform/machine anchoring the line.”
Quality assessments are not properly quantified — no expectation standard set with your clients
Testing sensitivity is an often-overlooked capability of inspection equipment, but accurately calibrating tests to your container type and quality expectations is key. For instance, many testers cannot accurately detect a hole size smaller than a paper clip’s diameter. This is often due to their testing air-pressure requirement which, if too strong, can distort the results because it may distort the shape of the bottle. The lower the pressure required for each container test, the more accurate the test can be.
Service and support are unavailable or slow to respond, amplifying your downtime
Even the greatest inspection equipment is useless if it is not operational. When equipment runs into issues, how quickly and easily can the issues be resolved? When choosing an inspection equipment partner, the post-sale support is just as critical as the equipment itself.
ALPS Inspection can help you differentiate your organization
Ask yourself the following three questions. If you cannot answer “yes” to all of them, ALPS Inspection can help.
1. Are we able to guarantee a qualitative accuracy level with our brand clients, and deliver on that promise with confidence?
2. Is our inspection equipment supplier available 24/7 and partnering with us to ensure our process stays online as much as possible?
3. Do we understand all the available equipment and available value-added options in the marketplace to optimize our production facilities for today’s container designs?
ALPS Inspection implements solutions that consider your entire production process, not just your equipment needs:
- Ensure equipment and options integrate with your current equipment seamlessly
- Industry-leading quality assurance with quantifiable results you can guarantee to your clients
- Industry-leading 24/7 service and support to diagnose and resolve issues immediately
Everything you need and nothing you do not.
Steiner is a product manager with ALPS Inspection, focused on optimizing leak testing equipment and addressing the ever-changing customer needs in the leak testing industry.
Contact: ALPS Inspection, 877-969-2713, www.alpsleak.com
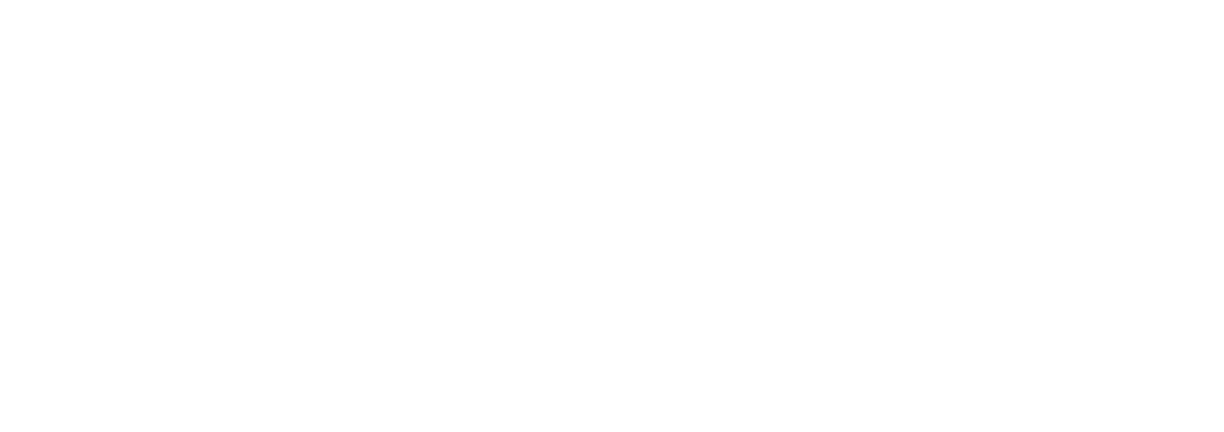