Making routine maintenance a click of a button, rather than a turn of the screw, is a priority for many OEMs, eager to meet their customers' demands for hands-off, downtime-free machine checkups.
Injection molding machine makers that have answered the call for easier maintenance and machine monitoring include Engel and Arburg. The companies' latest offerings including a new oil-condition software module from Engel and a targeted-lubrication system from Arburg.
ENGEL
Engel is unveiling two new condition monitoring modules for its e-connect.monitor system that it introduced in 2016.
The modules, which will be introduced this month at Fakuma in Friedrichshafen, Germany, monitor the condition of hydraulic pumps and oil on injection molding machines. They join existing modules that monitor plasticizing screws and spindles.
Condition monitoring makes it possible for companies operating Engel injection molding machines to check the condition of process-critical machine components during operation and reliably predict their remaining service life. As a result, unplanned downtime can be avoided and the working life of components maximized, according to the company.
"Condition-based predictive maintenance will be a crucial factor for high competitiveness in the factory of the future," said Joachim Kragl, director of advanced molding systems and processing at Engel. "E-connect.monitor is currently the only system on the market that allows condition-based, predictive maintenance of injection molding machine components."
Using the new oil-quality module, injection molding machine operators can monitor the quality of hydraulic oil online with the aid of sensors in the system. The sensors record data during production and transmit it by a secure data connection to Engel computer servers, where it's evaluated by software using Engel-developed mathematical models. The results are immediately transmitted back to the customer via Engel's e-connect customer portal.
Users receive information about the current condition of the oil and recommendations for planning for oil changes. Monitoring oil quality allows early detection of problems. Addressing poor oil conditions early averts equipment damage and unplanned downtime, according to the company.
The second new e-connect.monitor module oversees the condition of fixed-displacement pumps on servo-hydraulic Engel injection presses.
The efficiency of the pumps decreases continuously over their service life resulting in increased energy consumption. Normally, plastics processors notice a critical pump condition only when the machine cycle changes significantly or the machine fails, Engel said.
However, Engel's new pump-monitoring module works with Engel software to more accurately assess the condition of pumps. Engle conducted test runs on pump test beds and monitored pumps used in actual production to collect data that it used to develop algorithms that "precisely and conveniently show the customer the condition of their pumps," the company said.
The new e-connect.monitor module automatically records pump data, and Engel software can analyze the data without affecting production. The results are displayed in the e-connect portal as an easily understandable wear value, giving the user a basis for deciding whether and when to replace the pumps.
Engel will offer the new e-connect.monitor modules as retrofits for some existing machines. As a first step, the modules for monitoring hydraulic oil and pumps will be offered for injection molding machines with the current CC300 control generation. The company said it also is preparing retrofits for older generations of controllers.
ARBURG
In the summer, Arburg introduced targeted lubrication for all of its electric and hybrid Allrounder injection molding machines sold in the U.S.
The addition corresponds with the release in this country of Allrounder 1120 H, the largest injection molding machine in Arburg's Allrounder series.
The company plans to introduce a more sophisticated "performance-based" lubrication system that will be integrated into these machines in the near future.
As part of the rollout of the integrated lubrication system, Arburg optimized the electric toggle-type clamping units for condition monitoring and predictive maintenance. The central automatic oil system lubricates not only the toggles and planetary roller screw drives, but also all the guides and drives for the moving platen, drive platen and ejectors. The automated lubrication system eliminates the need for manual lubrication at numerous points.
Based on signals from the machine controller, an electric pump delivers measured doses of oil to lubrication points throughout the machine. Several pressure switches continuously provide oil-pressure feedback to the machine control. If a pressure change indicates a problem (caused by a broken or kinked line, for instance), the machine is immediately shut down before inadequate lubrication causes damage to the toggle system.
Grease lubrication, required at other points on the machine, is also centralized, with grease distributed through steel lines from a central location outside the machine guarding. While oil lubrication is automatic, grease lubrication is initiated manually. In both cases, however, the process is dramatically simplified because lubrication can take place while the machine is in operation and without removing machine guarding. This significantly reduces the time and costs associated with maintenance and results in increased machine availability.
The "performance-based" lubrication system that Arburg plans for the future will determine lubrication based on machine operating parameters such as forces, speeds, strokes and the timing of various portions of the cycle (clamping time, mold open time, etc.). This is in contrast to lubricating simply on based the number of machine cycles.
Testing has revealed that performance-based lubrication, supported by smart data analysis, can be expected to reduce lubricant consumption by as much as 30 percent depending on the machine's size and application.
Bruce Geiselman, senior staff reporter
Contact:
Arburg Inc., Rocky Hill, Conn., 860-667-6500, www.arburg.com
Engel Machinery Inc.,
York, Pa., 717-764-6818,www.engelglobal.com
Bruce Geiselman
Senior Staff Reporter Bruce Geiselman covers extrusion, blow molding, additive manufacturing, automation and end markets including automotive and packaging. He also writes features, including In Other Words and Problem Solved, for Plastics Machinery & Manufacturing, Plastics Recycling and The Journal of Blow Molding. He has extensive experience in daily and magazine journalism.
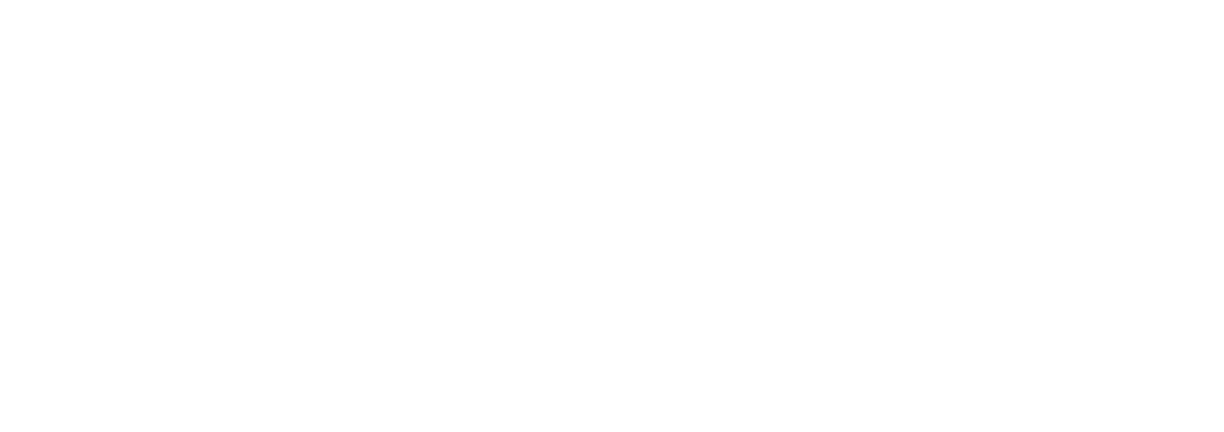