Fabricating and Assembly: Water-jet cutting offers unique fabricating advantages
Many common methods of cutting plastics have significant drawbacks. Die cutting is one option, but it can be expensive to have a die made — and when the part or material you're cutting changes, the die needs to change, too.Using a saw or drag knife is also a possibility, but that can produce shards and usually is appropriate only for straight-line cutting. Using a laser or plasma cutter, meanwhile, can melt or alter the composition of the plastic.
A new frontier for water jets
Happily, a new option is gaining traction. Water-jet cutting offers a unique set of advantages that are just starting to draw the attention of processors — and some of the machines can use their cutting precision to fabricate highly detailed parts.
"Water-jet cutting is still finding its way in plastics," said Stephen Bruner, VP of marketing with Omax. "But I think the more that people are exposed to it and get used to the idea, they'll start to take a look at the economics of the process."
In the basic water jet setup, Bruner said, the X-Y axis supports the cutting head, where the water (and the abrasive, if one is being used) is concentrated into a fine jet. That jet is directed down toward the material on the cutting table, and once the material is pierced, part of the jet passes through to a catcher tank, which collects the used water. "Unless you are using a closed-loop system in which the water is filtered and cooled, the catcher tank water is not reused," he said. "Normally the shop water source is what supplies the cutting water."
There are similarities in the way metal and plastics companies set up their production, which will speed the adoption process, said Wayne Silasi, marketing communications manager for WardJet.
"We're already seeing water jet reach deeply into the metal casting and forming industries for deflashing and degating applications," Silasi said. "Plastic injection molded parts require a lot of the same downstream clean-up processes; it is natural to think that water jets will make inroads in the plastics world, as the technology offers advantages over traditional trimming methods."
New capabilities are making the water-jet option more attractive to plastics companies, as well. The standard cutting head on a water jet typically is oriented perpendicular to the material's surface, allowing for straight, 90-degree edges. Often, that's all a plastics manufacturer needs.
However, recent advances in five-axis cutting technology have provided new capabilities — including the ability to cut bevels and 3-D parts.
"That includes the ability to cut shapes not possible on a standard cutting head, such as pyramids, diamonds, cones and even something as complex as a fan blade," Silasi said.
To take advantage of those possibilities, multiple water-jet manufacturers are actively marketing their new and upgraded products to the plastics industry.
Omax
"The vast majority of water jet's usage in the plastics industry falls into two buckets," Bruner said. "The first is rapid prototyping. You can take a block or sheet of plastic and use a water jet to do very complicated and very precise machining. It helps you determine, 'Is this the way we want to go?' Rather than build mold after mold to test changes in a plastic component, a water jet allows you to make small changes and incorporate them quickly and easily."
The other area is test-coupon cutting, which is done to determine the structural integrity of a part, such as its tensile strength. The old-school method would be to use a tool such as a jigsaw, but that doesn't offer the type of precision companies are looking for, Bruner said. "In destructive testing, you really want to dial in on the dimensions, because inaccuracy in coupon testing can directly affect the integrity of your final product."
For companies in need of that degree of precision, Omax offers the MicroMax JetMachining Center, which was upgraded last year. The Tilt-a-Jet feature, which now comes standard on the second-generation MicroMax, is a cutting head designed to achieve virtually zero taper — square edges — in final products, thanks to software that calculates the exact angle of the jet to offset the taper.
Another new feature will be of particular interest to plastics processors: an optional water-cooling system that ensures the liquid in the tank is maintained at a consistent temperature. Cutting with a water jet produces a lot of kinetic energy that causes the water in the catcher tank to heat up. Depending on the individual machine and the application, the cutting table might be positioned slightly above the water in the catcher tank, or the cutting table actually might be submerged in the water, which would reduce the noise and mess generated. Either way, the heat generated by the water in the catcher tank can cause big problems for fabricators.
"Depending on the substrate you're using, you can get some pretty significant dimensional changes if the water temperature changes from 65 degrees in the morning to 90 degrees in the afternoon," Bruner said.
Other upgrades in the new MicroMax include:• The X-Y cutting table is now isolated from the catcher tank to improve accuracy by minimizing vibration;• The resolution of the optical linear encoders for the drive system has been reduced to 0.1 micron (also to improve accuracy);• Omax raised the X bridge to facilitate more Z-axis travel so it could cut thicker materials;• The venting was clustered to accommodate HVAC ducting to manage water vapor; and• The new version is now compatible with Omax's variable-speed solids-removal system to eliminate the downtime that occurs when cleaning the catcher tank.
The MicroMax is capable of a positioning accuracy to within 5 microns or less. Its 7/15 Mini MaxJet5 nozzle can produce a kerf — a cut slit — as small as 0.015 inch.
Although the accuracy is provided by the built-in technology, it helps that the stiff construction of the MicroMax's full enclosure — designed for quiet operation — reduces vibrations.
The 7-foot-tall machine has a footprint of 74 by 84 inches, a table size of 35 by 36 inches, and an X-Y cutting envelope of 25 by 25 inches. The MicroMax can reach cutting speeds of 100 inches per second with a repeatability to within 0.0001 inch.
WardJet
Silasi cited flexibility as another selling point for water jetting.
"The versatility to switch the material you're cutting without reconfiguring your setup is where water jet really stands out," he said. "A plastics processor has a lot of options to choose from, but none truly equal the versatility a water jet has to offer. Water jet can cut anything from thin, delicate plastic to thick sheets of metal, all without producing a heat-affected zone, without the need to retool and with the ability to cut an infinite amount of shapes out of almost any material."
One of WardJet's biggest advantages is the ability to automate material loading and the speed of the cutting process. "By equipping your water jet with shuttle tables or a conveyor loading system, plastics manufacturers can load material without interrupting the cutting process," he said.
The ability to automate is a significant feature of WardJet's newest model, the E-2040, which can be paired with a variety of conveyors and loaders to save time and labor costs.
"When it comes to automation on the E series, a lot of our customers — plastic manufacturers included — will utilize shuttle tables," Silasi said. "Shuttle tables allow the operator to load and unload material while another cut is being performed, leading to increased production."
Shuttle tables come in many shapes and sizes, some manual and others fully automated. Some shuttle tables act like a system of drawers that are pulled out and pushed back in, while others slide through the water jet and out the other side.
"By connecting a series of sensors and controls to the tables, an operator can individually control each shuttle table or automatically have them switch out when the current cut is finished," Silasi said. "Used in combination with self-closing doors, it can keep the operator safe while loading the next batch of material."
The E-2040 can cut at speeds of over 750 inches per minute — a major advantage, given the machine's 6-foot-by-12-foot cutting envelope. "A large cutting envelope not only allows you to cut larger-sized parts," but also opens up many opportunities for savings. "The extra space allows you to cut multiple parts at a time with less loading and unloading. Also, the extra cutting area allows the user to add multiple cutting heads that can increase their overall production," he said.
Its large size doesn't compromise its accuracy, however, as it offers a positional tolerance to within 0.003 inch per axis and repeatability to within 0.001 inch per axis.
Users can add almost any cutting head configuration to the E-2040 depending on specific needs, including multiple five-axis or taper-compensation cutting heads.
Flow International Corp.
Wasted material and additional work caused by heat distortion and fracturing are the least of the risks some plastics-cutting methods bring to the production floor. The health of the workers is a concern, as well.
"In comparison to heat processes, cutting on a water jet is also safer for the working environment," said Michael Albert, lab supervisor with Flow International Corp. "Most plastics cut with heat can produce fumes and contaminants that are hazardous to your health."
Flow International offers a series of water jets that work well with plastics. The series includes everything from an entry-level machine that covers the basics to a huge model designed for large parts to a completely enclosed model for high-precision cutting. Within the last year, all models include the FlowXpert model-based CAD/CAM software.
The Mach 300 is practical and efficient, offering a small footprint, easy programming and operation, and a variety of options and configurations to match an individual company's needs. It offers a linear straightness accuracy of 0.003 inch per yard, a rapid traverse maximum speed (the speed it moves when it's not cutting) of 472 inches per minute and repeatability to within 0.0025 inch.
The Mach 500 is Flow International's quickest water jet. Cycle time — the factor that determines productivity — is not determined by top speed except when cutting in a perfectly straight line, the company said. Rather, cycle time is determined by how quickly the water jet accelerates and decelerates. The Mach 500 has a cycle time that is 20 percent faster than the machines that the Mach series replaced.
It offers a linear straightness accuracy of 0.0013 inch per yard, a rapid traverse maximum speed of more than 700 inches per minute and repeatability to within 0.001 inch.
The Mach 700 is the workhorse of Flow Waterjet Americas' lineup, designed to process large-format parts. Its all-steel construction makes it ideal for demanding, heavy-industry environments, and it offers three large base sizes: 26, 50 and 79 feet. It doesn't sacrifice speed or repeatability, either, managing a linear straightness accuracy of 0.0015 inch per yard, a rapid traverse maximum speed of more than 1,400 inches per minute and repeatability to within 0.001 inch.
Finally, there is the NanoJet, a small-format water-jet machining center that is completely enclosed for precise, clean and quiet cutting. The standard model is equipped with rotating-nut ball-screw drives, but when maximum speed is the goal, an optional linear motion drive also is available. It offers a linear straightness accuracy of 0.0024 inch per yard, a rapid traverse maximum speed of more than 590 inches per minute and repeatability to within 0.0004 inch.
Dynamic Robotic Solutions
Dynamic Robotic Solutions (DRS) has spent the last several months adding muscle to its lineup of water-jet cutting equipment. In July, the company announced the availability of a new system capable of trimming materials at 90,000 psi. Previously, its most powerful system topped out at 60,000 psi.
The 90,000-psi water jet "gives us the capability to process lightweight materials like CFRP [carbon-fiber-reinforced plastic] and thick plastics that in the past were thought not possible to process using a standard water jet without abrasive," said Bruce Potts, the company's CEO.
"Higher Corporate Average Fuel Economy requirements and lower CO2 emissions legislation are driving the light-weighting of vehicles, which often results in new materials which are stronger, but therefore also harder to cut. This is requiring the higher-pressure water-jet, and in some cases, laser technologies to cut parts that might have previously been stamped or die cut."
The 90,000-psi water-jet system is part of the DRS Process Solution Center (PSC), a customized combination of equipment and processes recommended by the company's experts. The goal is to determine what combination best suits the customer's specific quality needs, throughput requirements and financial situation.
One of the basic pieces of equipment used in the PSC for cutting plastics is a dual-robot A-Frame cutting system that includes two floor-mounted, six-axis AccuTrim WJ-44 robots from Fanuc, plumbed for high-pressure water jet cutting; a JetVac vacuum system for water and waste collection; and several types of productivity-enhancing water-jet software programs.
The complete system was designed to minimize space requirements and make better parts. "The systems which DRS supplies are able to group two to six robots together in a very tight work area, which allows cutting of the entire part in one station and on one fixture, thereby reducing floor space needs and improving quality," Potts said.
Going forward, Potts said some people have asked if 3-D printing might begin biting into water-jet cutting's market share, because it produces a net-shape product that might not require trimming. However, that hasn't happened yet. "So far, we have not seen an impact from 3-D printers in our cutting business," he said. "For now, the slower speeds of this technology have limited the number of applications that 3-D printing is a good solution for. Additionally, a good degree of the trimming that is done is best performed in a dynamic manner, very close to the final assembly, to adjust to differing build conditions."
Michael T. McCue, copy editor
For more information
Dynamic Robotic Solutions Inc.,Auburn Hills, Mich., 248-829-2800, www.drsrobotics.com
Flow International Corp.,Kent, Wash., 253-850-3500, www.flowwaterjet.com
Omax Corp.,Kent, Wash., 253-872-2300, www.omax.com
WardJet Inc.,Tallmadge, Ohio, 330-677-9100, https://wardjet.com
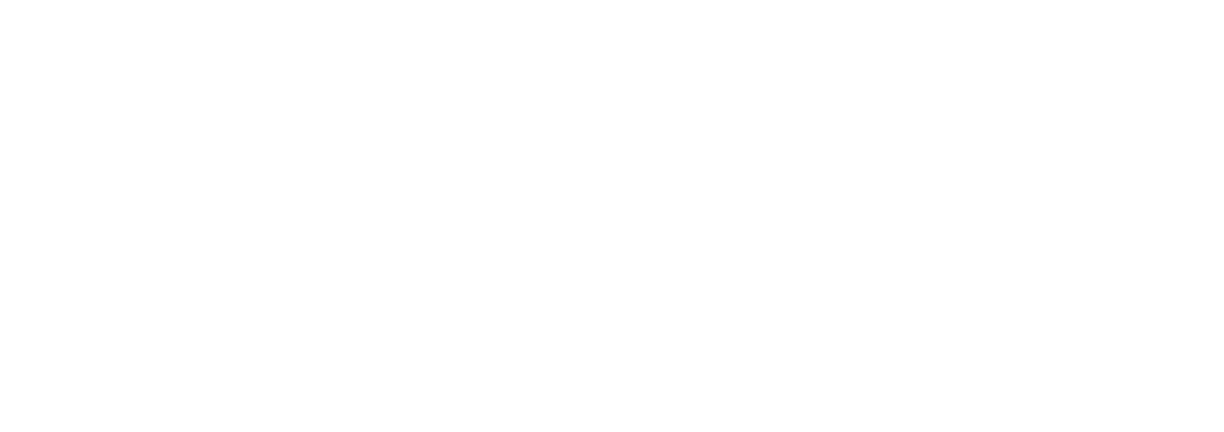