Processors in the automotive, medical and other markets are demanding precision when joining plastic components, say providers of welding systems.
Suppliers point to a number of advantages in using these systems. They include cost reductions, environmental cleanliness, the protection of sensitive electronics and other components, aesthetic design capabilities and reduced assembly time.
"Welding, when done properly, forms a thermoplastic molecular bond that is as strong or stronger than the original two pieces being welded," explained Dave Rothbard, product specialist, plastics fabrication for the U.S. for Leister Technologies.
Plastics, he said, present unique challenges during assembly. In some cases, this rules out other bonding strategies. "Other methods, like gluing, form a very thin bond that is prone to failure in cases of thermal expansion or elongation and shrinkage. Molecular bonds do not fail under these conditions. Typically, thermoplastics expand and shrink at a rate 10 times greater than steel."
Leister Technologies
Offering joining technologies for an array of industries, Leister provides hot-air hand tools, welding rods and welding machines that can be used in fabrication tasks involving plastics. Specifically, the tools are useful in the construction of storage tanks and promotional banners.
Last month, the company started shipping its Airstream ST, a plug-and-play unit that provides a constant supply of clean, dry air to up to two hand-held, manual units known as pen welders. With the Airstream ST, users can access the right amount of air without making any manual adjustments, Rothbard said.
The Airstream ST operates at a low decibel level and features an automatic cool-down mode to lengthen the life of the heating element. The use of a brushless motor, designed by Leister, reduces maintenance costs. The air-supply device is compact and, with the addition of casters, can be wheeled around the shop or used as a stationary unit. The mobility complements the company's pen welders. Commonly used for welding PVC, pen welders can handle precise temperatures and tight areas. Rothbard contrasted the items with larger extrusion welders, which bond molten beads of plastic.
"Due to the narrow melt [temperature] window and chemistry of PVC," he said, "not all extrusion welders are capable of welding PVC." The pen welders "are also commonly used in applications where an extrusion welder cannot reach."
In addition to debuting the Airstream ST, Leister also recently introduced its Hemtek ST, an efficient unit designed to weld hems from corner to corner — ideal for small- and medium-sized promotional banners and tarps.
Emabond Solutions
Electromagnetic welding-system maker Emabond Solutions notes a number of challenges in joining plastic parts, including the complex geometries and materials involved. Touting its "Heat-on-Command" technology, it makes systems that couple high-frequency energy with conductive or electromagnetic materials to create heat for joining materials. The systems can handle certain dissimilar materials, highly-filled thermoplastics and flexible to rigid substrates.
According to the company, the nonviolent, noncontact process results in strong welds with no unsightly weld lines. It requires no post-weld trimming or cleaning.
Steve Chookazian, VP of sales and marketing, said the company last year introduced its OEM I and OEM II welding machines. Since then, it has been exporting them all over the world. "The Emabond electromagnetic welding process provides superior structural strength and performance for a wide range of thermoplastic joining applications," he said. "The new machines offer the users a wide range of process controls and data acquisition for each weld cycle."
The OEM I is designed for parts as big as 25 inches by 15 inches by 33 inches. It includes a 1-, 2- or 3-kilowatt (kW) solid-state radio-frequency (RF) power supply, integrated water-cooling chiller, specially designed welding nest and RF coil, standardized pneumatic package and a touch-screen display.
Designed to weld parts of up to 40 inches by 30 inches by 35 inches, the OEM II includes the same features, but has a power supply of 3 Kw to 5 Kw.
Rinco Ultrasonics
Available with a choice of frequencies of 20 kilohertz (KHz) or 35 KHz, Rinco's new Electrical Motion ultrasonic welding system enables users to finely regulate the weld, using precise positioning of the sonotrode and the applied welding force to the welding rate. This means considerably better results, whether welding, punching, cutting or sealing molded thermoplastic parts, nonwovens or synthetic textiles. The machine is equipped with a high-performance, industrial PC that can be comfortably operated via a 12-inch touch screen, with the welding process controlled via an ergonomically designed, two-handed controller.
"This is a nice addition to our product line," Managing Director Gordon Hull said. "It helps push the limits of what our customers can do."
Hull said that the Electrical Motion is an evolution of the company's Dynamic 3000 ultrasonic welding machine, which was designed for demanding welding operations involving medium-sized to large thermoplastic parts.
Unlike welders that have a compressed air-driven design, in which the feed for the sonotrode returns after every weld cycle to the starting position in the pneumatic cylinder, the starting position with the Electrical Motion can be selected freely. As a result, the weld cycle can often be shortened, depending on the welded object's geometry. Users also can freely select the welding mode.
The Electrical Motion unit offers eight welding modes, from time, distance and energy-related modes, to a combination of time and energy and a mode for presetting the melting rate. For all welding modes, the operator can adjust the ultrasonic trigger for force, distance and time.
Depending on the welding mode, the actual process can be subdivided into as many as 10 steps, a level of detail that means a much more controlled welding process than with a pneumatic drive, Hull said. Even parts that were difficult or impossible to weld in the past now can be joined reliably using Electrical Motion with a reproducible and uniform weld, he said. The converter and booster are identical in construction with the pneumatic Dynamic 3000 series, so tooling already made for this machine also can be used with the new Electrical Motion.
The welder's Linux Ubuntu operating system is logically structured and easy to use, another big selling point, Hull said. The welder's monitor displays weld characteristics as graphs, and the results and parameter datasets can be exported. The system records and stores all results, including parameter changes providing a non-erasable audit trail, accessible only to authorized personnel.
"This is a great selling point," Hull said. "You can see who changed what and why."
It's important to know if a change in parameters results in a failed weld. With the traceability, the user can see if any changes result in any issues with the final product, which is something customers want to know, as well. "The audit trail should help produce a more repeatable part."
This traceability also helps provide a quick diagnosis of any problems. With the help of remote maintenance offered by Rinco, users can identify issues and, in most cases, correct any parameter errors.
In addition to the welder, the company recently added the CLA-50 and CLA-100 compact linear actuator models designed specifically for the automotive industry. OEMs have been building their own actuators because they couldn't find one that was cost-effective and met stringent industry requirements, Hull said.
The ultrasonic actuators can be used in combination to weld or stake the bosses that hold together interior automotive trim components, such as door panel assemblies, instrument panel assemblies and console assemblies. With them, vehicle manufacturers can custom-build automated machinery to match the configuration of the assemblies they're welding. For example, multiple actuators can be mounted on a platen that's married up to a door assembly; when the platen and the door assembly come into contact in an automated work cell, the actuators each weld or stake the boss opposite them on the door assembly.
Hull said the actuators have integrated air cooling with multiple mounting locations for tight layout patterns. They provide smooth, consistent operation, maintaining an optimum operating temperature for the ultrasonic stack.
Most actuators come without air cooling, meaning the buyer has to add it, he said.
Rinco offers the CLA units in conjunction with anti-rotating 40mm-diameter air cylinders with multiple stroke lengths of 50mm and 100mm, as well as various mounting configurations to meet any mounting arrangement.
Other optional features include position sensors on the air cylinder and distance monitoring feedback. The distance monitoring allows for finite control of the ultrasonic "on" signal that will result in a more consistent weld point than with a time-only feature. This monitoring can reduce potential read-through issues as well as increase weld point strength.
AMADA MIYACHI
Welding-system manufacturer Amada Miyachi supplies equipment to a wide range of markets, including the medical device, electric vehicle and solar industries, as well as the global electronics and automotive markets.
Earlier this year, it expanded its popular LMF series of laser welders with the LMF70-HP. According to product manager Mark Boyle, the welder can be used to join opaque and semi-transmissive plastics. "The most common application," he said, "is plastic welding of automotive electronic casings."
The beam width is ideal for areas no bigger than 6 inches by inches. Typically, welding plastics made of the same materials works best.
Amada Miyachi offers the welder as an OEM product with salvo scanning beam delivery and controller. The welder also can be integrated with the company's Laser Marking Workstation, or LMWS.
As with other LMF welders, the LMF70-HP is designed with multiple integration options to suit stand-alone operation, full production automation and low-volume prototype development. The air-cooled, sealed industrial package has been designed for operation in harsh environments and comes with powerful control software with a user-friendly interface.
LPKF Laser & Electronics
For LPKF, automotive taillights are a sign of what's ahead in welding. For such applications, laser welding provides the precision needed to accurately and cleanly weld parts, said James Liddle, director of North American sales. Older forms of plastics welding, he said, are detrimental to lighting products, such as taillights — an LPKF specialty.
"We are engaged with every lighting supplier in the automotive industry," he said. The 3-D welding process cuts cycle times by as much as 30 percent and costs by as much a third.
LPKF's PowerWeld3D 8000, which began shipping earlier this year, is designed for the high-speed series production of large components, including taillights, pillars, fenders and sunroofs.
"It was designed to allow the easy manufacturing of the latest OEM lighting designs, reduce costs, increase yields and improve quality," Liddle said.
The new welder takes on a number of challenges posed by emerging trends in automotive lighting designs. They include the growing popularity of rear combined lamps and the increasing thickness of skin molding lenses, measuring about 4mm or 5mm, rather than about 2mm or 3mm for regular molded lenses. In addition, automakers are increasingly looking to incorporate weld seams as design elements.
Using a method called quasi-simultaneous welding, in which the welder plasticizes an entire joint at once, the PowerWeld3D 8000 can bond 3-D components as large as about 39.4 inches by 29.5 inches.
The system also offers "wobble welding." In this quasi-simultaneous method, the laser beam moves rapidly and repeatedly around a contour, controlling the width of a weld while maintaining a stable temperature. This allows easy creation of weld seams with widths of between 1mm and 5mm.
It's ideal for automotive lighting assemblies, Liddle said, because it can compensate for changing geometries over the entire weld surface.
"This is accomplished by moving the beam in a circular manner and varying the forward velocity of the beam over the part while controlling the frequency of the oscillations to produce the same-size weld seam regardless of the angle or height of the lens under the laser beam," he said.
The PowerWeld3D 8000 is driven by new ProSet 3D software that automatically determines and sets up the process parameters in minutes rather than days, Liddle said.
Branson Ultrasonics
Branson, a business of Emerson, supplies welders that are used in the manufacture of automotive sensors and control modules, filter assemblies, electronic enclosures, irrigation systems and medical products. Designed for welding large plastic parts, such as those turned out by automotive and appliance manufacturers, its GLX-3 high-speed laser welder joins materials with clean, particulate-free seams.
With four levels of laser power options — 1,250, 1,500, 1,750 and 2,000 watts — the welder can deliver cycle times of 0.5 to 5 seconds on weld lines of about 6.6 feet, depending on part material and geometric complexity. It provides a wide range of clamping force, from 1 kilonewton (kN) to 25 kN, and closed-loop, clamp-force control.
It incorporates a number of advanced features, including Branson's patented Simultaneous Thru-Transmission Infrared (STTIr) process, which heats, melts and joins the entire weld line of two or more parts simultaneously. With the process, the welder can illuminate the entire welding surface at once, unlike other techniques that require scanning the weld joint. According to the company, the system is significantly faster and provides more precise melting of the weld line than scan or trace laser welders. Welding all of the joints simultaneously leads to more consistent welds.
The new system comes equipped with a high-speed, servo-driven lift table measuring about 55.5 inches by 23.6 with a high overhead clearance, capable of accommodating single- or multi-cavity tooling with combined weights of up to about 1,100 pounds. A 12-inch, color interface simplifies training, setup, adjustment and diagnostics. In addition to the GLX-3, Branson also recently released its GVX-2 H/HR vibration welder, which is designed for joining large parts. With a powerful vibration head that measures about 34.6 inches by 14.8 inches, it is part of a line of welders suitable for assembling a variety of products, including medical filters, gas tanks, taillights, and dashboards. It features a large lift table that can accommodate lower fixtures for part holding of up to 42.1 inches by 23.7 inches.
Phillip Britt, correspondent
For more information
Amada Miyachi America Inc.,Monrovia, Calif., 626-303-5676, www.amadamiyachi.com
Branson Ultrasonics Corp.,Danbury, Conn., 203-796-0400, www.emerson.com/en-us/automation/branson
Emabond Solutions,Norwood, N.J., 201-767-7400, www.emabond.com
Leister Technologies LLC,Itasca, Ill., 855-534-7837, www.leister.com
LPKF Laser & Electronics,Tualatin, Ore., 503-454-4200, www.lpkfusa.com
Rinco Ultrasonics USA Inc.,Danbury, Conn., 203-744-4500, www.rinco-usa.com
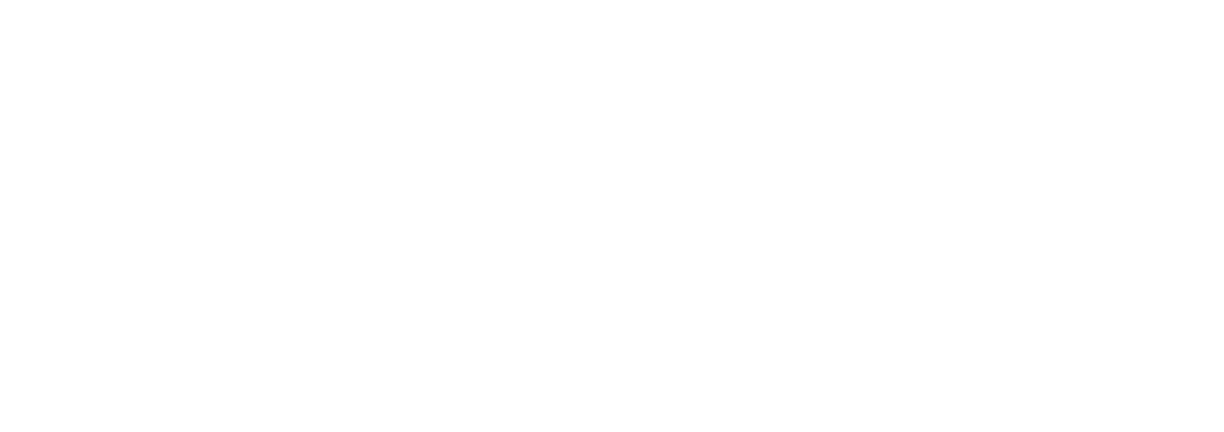