Integrating robots into a processing plant is getting easier. You can now buy a collaborative robot, take it out of the box and have it performing very simple tasks after three to four hours of fiddling with it.
But for complex tasks with intricate or tiny parts, you need more expertise.
"When they ask, 'How can I do that,' we can come up with a solution," Rick Brookshire, group product manager for robots at Epson, said during a visit by Plastics Machinery Magazine. Brookshire leads product development efforts as part of the global Epson Robots product development team. This requires working closely with Epson's Applications Engineering Department in Carson, Calif., which conducts about 150 feasibility studies a year for both customers and non-customers.
A simple feasibility study can take a few hours, especially if it can be accomplished with Epson's simulation software. But a more complex problem that includes cameras and vision equipment or force sensing can take as long as two weeks. Epson does not charge for the service but uses it to help current clients and close sales to prospective customers.
Epson, which has the No. 1 market share globally for SCARA robots and offers six-axis and linear module robots as well, sells directly to processors and through systems integrators. The primary customers for Epson robots are makers of automotive, electronic, consumer and medical products.
The Applications Engineering lab is filled with robots in various sizes, conveyors in many configurations, cameras and vision equipment and all sorts of fixtures, trays and tooling. When feasibility clients first approach Epson, they provide drawings or parts to illustrate what they need the robots to do. "They always want to know if a robot can do it or can the robot meet a certain cycle time," Brookshire said.
During PMM's visit, engineers were performing a feasibility study for a packaging application in which a robot grabbed plastic pieces from containers as if the parts had just come out of an injection press and placed them in a tray in a box. The pieces needed to be identified using vision software, picked up, oriented correctly and placed in the tray that would be displayed on a store shelf. All that had to take place as the parts moved down a conveyor.
Epson sells hundreds of robot configurations, but Brookshire said the lab also uses a lot of "3-D printed components and simplistic fixturing or setups to make things work here. We only have to make it work one time to show the proof of concept and cycle times. Our customer can then put it in his factory and use a lot of nicer components and fixtures so that it will work constantly over the long run."
The feasibility study can include recommendations for the correct size of robot, end-of-arm tooling, vision equipment, conveyor speed, tray or fixtures, flexible feeders, placement of the robot and orientation of the trays and conveyors.
Epson teams with VTR Feeder Solutions for high-speed flexible feeders. The feeder integrated into an Epson system separates, or singulates, small parts so the vision system can identify and tell the robot to pick up an individual part from a group. VTR also makes the tray, or fixture, that drops into the flexible feeder to orient parts. Each one is custom-made for a specific part.
During the visit, an engineer was working to get a robot to pick up a tiny washer from a tray of washers and install it on a plastic piece. Epson added a backlight to help the vision system identify the washers after they had been separated. Once the two pieces were joined and moved to a staging area, another vision system was used to verify that the washer was properly seated.
Once an entire system is working, Epson provides the customer with all the software it needs and even a video of how to make the system work in the required cycle time.
Brookshire said feasibility studies are performed only for "real projects" and not theoretical or research questions. "This can be a big investment and the people we do them for understand it needs to be an actual project," he said. He declined to estimate an average cost to Epson for conducting a feasibility study. He said the lab has all the robots and other equipment on hand and its engineers have created thousands of feasibility studies over the years so they have learned how to keep the total development time to a minimum.
In another recent project, a customer wanted to place a very tight-fitting cap over part of a printed circuit board without bending the cap or damaging the circuit board. Vision software was not up to the job, so Epson's integrated force guidance product was used to first pull the cap onto one corner, then pull the second side onto the part. "It took us three or four days to build that, but the end result was a solution to a problem that the customer was not previously able to solve with other automation tools," Brookshire said.
Feasibility studies are nearly always confidential. "We cannot take information we learned from one company's project and apply it to a competitor's similar project," Brookshire said. "If it is an unrelated project for a non-competitive customer, we might be able to use a little bit of what we learned, but 99 percent of the studies are confidential when it comes to sharing the 'how to' with other companies, so we generally work on unique solutions for each application."
The lab also is working on ways to better integrate third-party automation products so they can handle different parts without requiring adjustments or new software. Moving forward, Epson is working on using artificial intelligence so the robots can determine the best or fastest movement path and way to place parts.
"Let's do more things automatically so the user does not have to think about it," Brookshire said.
That means that problem-solving in the lab is translating into smarter robots that figure things out for themselves.
Ron Shinn, editor
For more information
Epson America Inc.,Carson, Calif., 562-290-5910, www.epsonrobots.com
VTR Feeder Solutions,Grimsby, Ontario, 800-313-8655, www.vtrfeedersolutions.com
Ron Shinn | Editor
Editor Ron Shinn is a co-founder of Plastics Machinery & Manufacturing and has been covering the plastics industry for more than 35 years. He leads the editorial team, directs coverage and sets the editorial calendar. He also writes features, including the Talking Points column and On the Factory Floor, and covers recycling and sustainability for PMM and Plastics Recycling.
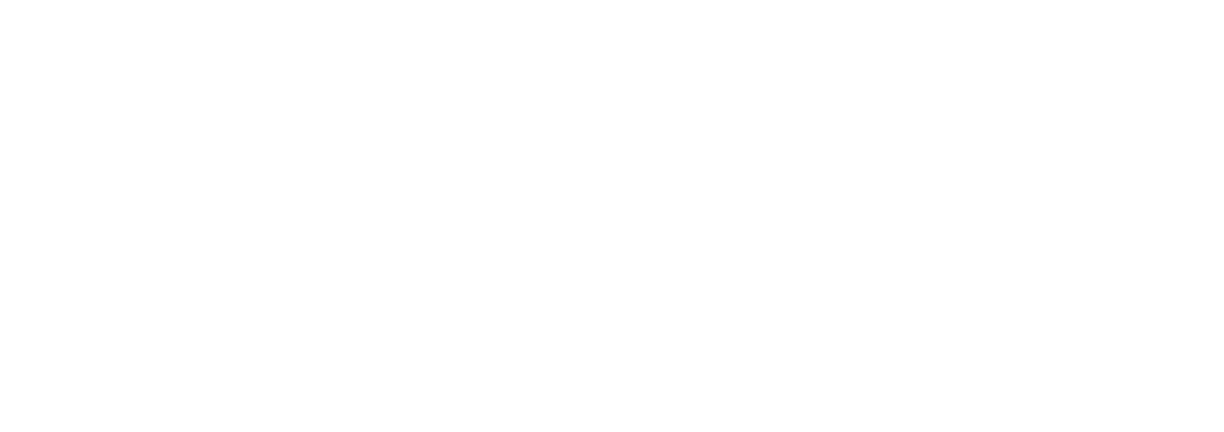