Special Report: Plasticizing elements enhanced for twin-screw extrusion
Manufacturers of twin-screw extruders are improving their machines with new plasticizing elements and barrel designs.
Coperion
To significantly increase throughput rates of its ZSK extruder series, Coperion developed special screw and kneading elements with a new and patented cross-section design. The company presented the new screw elements for the first time at Chinaplas 2017 in May.
These screw elements are ideal for highly filled resins, including those with high concentrations of calcium carbonate and titanium dioxide or talc.
In addition to higher throughputs, the new screw elements ensure higher loading of filler, better dispersion and homogenization, lower energy consumption and a significant increase in profitability, according to the company.
Tests at Coperion's lab in Stuttgart, Germany, showed significant increases in throughput. For example, when processing PP and 70 percent calcium carbonate on a twin-screw ZSK 58 Mc18 extruder, the new screw elements resulted in a throughput increase from 1,213 pounds per hour to 1,984 pounds per hour. The company had similar results when processing PE with 80 percent calcium carbonate on a ZSK 92 Mc18, with throughput increasing from 4,850 pounds per hour to 6,614 pounds per hour.
In addition to the new screw elements, the company at the K show introduced a revised, compact version of its ZSK Mc¹â¸ twin-screw extruder, which includes improved accessibility of the processing section. The machine is easier to clean, the twin-screw configuration can be changed more quickly, and ultimately, productivity of the entire system is increased.
eFactor3
EFactor3 LLC, the North American distributor for MAS Maschinen und Anlagenbau Schulz GmbH, Pucking, Austria, recently began selling extruders with a segmented barrel design.
The new design permits users to exchange individual barrel sections, rather than replace the entire cylinder. Users of a segmented barrel can replace a section of a worn barrel while keeping in place less-worn sections.
"The benefit to the customer in having more segments to the barrel is the wear costs are reduced," said Hartmut Bendfeldt, president of eFactor3. "All the sections that are basically plasticizing the material — the feed section and the melting section where you turn the solid into a liquid — that is where you create the most wear. Once it is molten, in a liquid form, the plastic doesn't wear much anymore."
The sections that wear most quickly can be replaced with individual cylinder sections with special wear protection, according to the company.
The new machines were introduced at the K show last year. The new extruder models have been sold to at least two plastics recyclers. One recycler is processing PP in a compounding operation. The second is recompounding and recycling an assortment of polymers.
MAS' conical co-rotating twin-screw extruders can be used for any kind of compounding operation that traditional twin-screw extruders can perform, but the benefit of the company's conical design is that it also can handle lower bulk density recycled material, typically in flakes, with the same ease as virgin pellets, Bendfeldt said.With the conical design, screws at the feed end are wider in diameter than at the outfeed end.
"Everybody can process virgin material in the form of pellets," he said. "But when it comes to recycled content, with the MAS extruder, because of its conical co-rotating design, it does not make any difference whether it is virgin pellets or lower- bulk-density regrind flakes. We have the same output and good homogenization."
Bruce Geiselman, senior staff reporter
For more information
Coperion Corp.,Sewell, N.J., 201-327-6300, www.coperion.com
eFactor3 LLC,Pineville, N.C., 704-944-3232, www.efactor3.com
Bruce Geiselman
Senior Staff Reporter Bruce Geiselman covers extrusion, blow molding, additive manufacturing, automation and end markets including automotive and packaging. He also writes features, including In Other Words and Problem Solved, for Plastics Machinery & Manufacturing, Plastics Recycling and The Journal of Blow Molding. He has extensive experience in daily and magazine journalism.
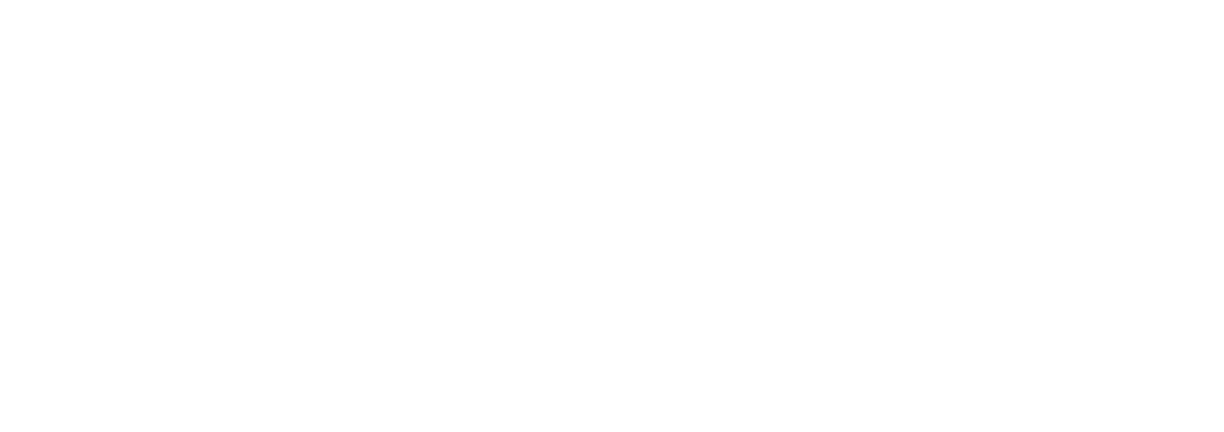