Special Report: Nozzle, tip components gain broader use in molding
Zeiger Industries has updated its Continuous Taper Front End (CTFE) cap, nozzle and nozzle-tip components with a new design and new metallurgy to improve their performance when processing clear polymers or fire-retardant resins, as well as for operations that require frequent color changes.
Zeiger's CTFE components were made primarily for processing PVC. Featuring a tapered design, they promote self-cleaning of the end cap, nozzle and nozzle tip with each shot of material. Zeiger realized this design could be of benefit to injection molders processing polycarbonate, acrylic and nylon, as well as halogen-free fire-retardant (HFFR) materials to minimize material hang-up and degradation, said Stan Glover, sales director.
Clear polymers moving through a traditional nozzle body with a straight bore can stagnate. That material can build up and degrade, becoming the source of black specks in a part that should be clear, such as a lens. With HFFR materials, a straight-bore nozzle body may impart a higher shear that can alter the performance of the material. Depending on the type of metal used in the nozzle body, HFFR materials can cause corrosion, especially in the presence of moisture, Glover said.
The geometry of the updated CTFE components minimizes stagnation points, imparts low mechanical shear to the polymer and clears the flow passages of material for every shot, which minimizes reject rates, Glover said.
The CTFE design for PVC processing incorporates what Glover calls a long and pointed nose. Such a design is "detrimental when processing traditional thermoplastics rather than a rigid PVC," he said. "We designed the updated CTFE with a 60-degree nose angle for thermoplastic molding instead of a long nose angle for PVC processing, of 20 or 22 degrees," Glover said.
The degree of taper is based on the diameter of the plasticizing screw, but generally the rear opening of a replaceable nozzle tip or replaceable end cap is 0.5 inch in diameter, Glover said. "We are not changing the nose angle of the molder's existing machine, so the screw tip, screw and barrel geometry remain constant. The updated CTFE components just modify the low-cost end, nozzle and nozzle tip," Glover said.
In addition to the updated design of the nozzle, tip and end cap, the company is are utilizing a new selection of substrate metals. The nozzle, which Zeiger traditionally manufactured from a hardened stainless steel, is now made using a vanadium-bearing stainless steel. For the nozzle tip, Zeiger uses a precipitating hardening 17-4 tool steel. When the end cap is used for processing non-PVC resins, it is made from a vanadium tool steel. "The design and the material composition of the end cap, nozzle and nozzle tip have to be matched to overcome processing challenges when molding clear or HFFR materials," Glover said.
Zeiger has numerous upgraded CTFE components installed in commercial manufacturing operations.
Mikell Knights, senior staff reporter
Contact
Zeiger Industries Inc.,Canton, Ohio, 330-484-4413, www.zeigerindustries.com
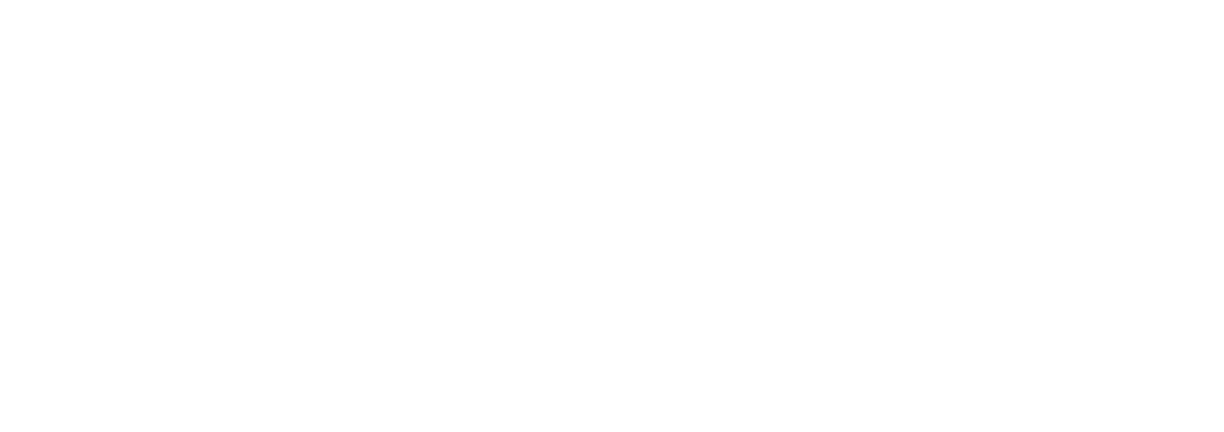