Universal Robots has expanded its Universal Robots+ online showroom of plug-and-play products, including end effectors and software for the company's six-axis collaborative robots.
The Danish company launched Universal Robots+ at www.universal-robots.com/plus/ last June. It has grown to feature about 50 products developed by third parties that are certified to work with the company's robots.
Douglas Peterson, GM of Universal Robots USA, compares Universal Robots+ to an app store for cell phones. Universal Robots manufactures its UR3, UR5 and UR10 collaborative robots, and third-party developers come up with products that will work with them. Universal Robots ensures the products work seamlessly with its robots before offering them for sale through the online store.
"We are launching more and more of these every day," Peterson said. "We have a goal to get to over 100 of these applications by the end of the year and just keep growing it from there, just like your app store keeps growing."
Third-party developers receive free support from Universal Robots. Once a developer comes up with a prototype, Universal Robots examines it and tests it to ensure it conforms to the company's quality requirements and can be integrated with UR robots.
The types of tools available on the Universal Robots+ website include grippers, screwdrivers, cameras, vision systems, scanners and torque sensors. In addition, developers have come up with sleeves that protect a robot from dust, debris, paint and liquids, and a protector that goes around a robot's teach pendant to protect it if it's dropped.
Bruce Geiselman, senior staff reporter
Contact:
Universal Robots USA Inc.,
Ann Arbor, Mich., 844-462-6268, www.universal-robots.com
Bruce Geiselman
Senior Staff Reporter Bruce Geiselman covers extrusion, blow molding, additive manufacturing, automation and end markets including automotive and packaging. He also writes features, including In Other Words and Problem Solved, for Plastics Machinery & Manufacturing, Plastics Recycling and The Journal of Blow Molding. He has extensive experience in daily and magazine journalism.
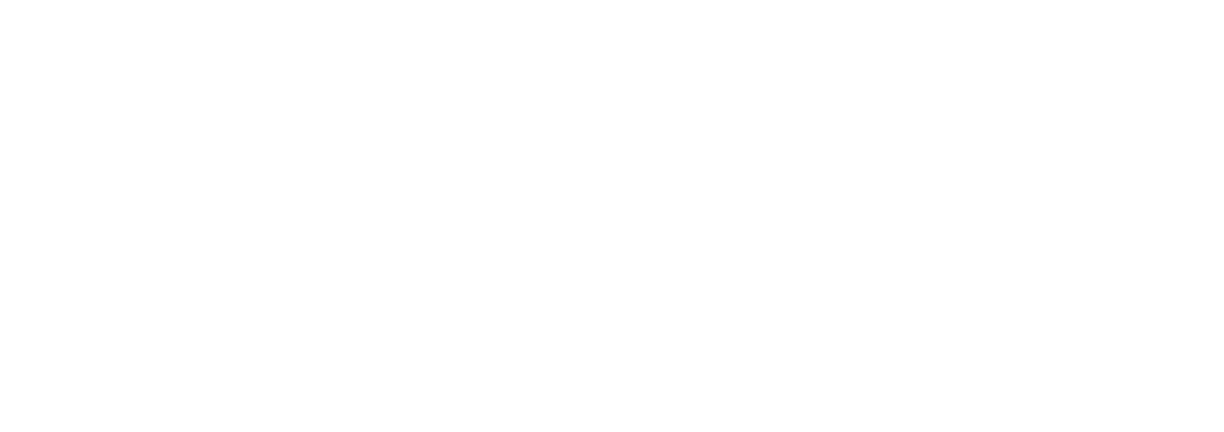