Technologies dealing with foamed PET sheet are among the latest innovations offered by sheet extrusion machine suppliers. In addition to SML and Gneuss, which have launched technologies for lightweighting, Breyer has improved its water-cooled extruder drives.
SML
SML is offering a new version of its FlexiPET sheet extrusion line that can produce three-layer PET sheet with a foamed inner layer, said Mark Jones, who handles SML North American business development and customer support. The pro- duction line also can make the inner layer from standard PET.
A conical twin-screw extruder produces the center layer, with the physical foaming performed by injecting carbon dioxide. The sheet, Jones said, is mainly used in thermoformed food packaging.
Manufacturing PET sheet with a foam center layer has been difficult, and the material is uncommon commercially, he said. It has a typical overall density of 0.7 to 0.9 kilograms per cubic decime- ter (about 44 to 56 pounds per cubic foot). That compares with 1.35 kilograms per cubic decimeter (about 84 pounds per cubic foot) for PET sheet with three rigid layers, he said. "The sheet with the foamed center layer results in considerable material savings. And material costs are the main costs for the sheet."
The biggest challenge with this development, Jones said, is designing the system to use a conical twin-screw extruder to yield a foam with good cell structure and quality.
"The manufacture of physically foamed PET requires that special attention is paid to melt treatment," the company said about the innovation in
a news release. "Accordingly, this was an absolute priority during the design of the melt-preparation equipment."
Varous aspects of the design ensure that the melt temperature is precisely controlled and that the melt
is homogenous, Jones said. Melt temperature and homogeneity have a strong impact on gas cell uniformity and growth, and are integral to foam quality.
The 90mm extruder used for the foam layer has a maximum output of 1.5 tons per hour. It can process materials ranging from 100 percent virgin resin to 100 percent regrind or bottle flakes. An advantage of the conical extruder is its large inlet. This makes it ideal for processing a high percentage of regrind, even for materials with a low bulk density.
A 75mm single-screw coextruder is used to produce the other two layers, and has a maximum output of 661 pounds per hour. The roll stack and downstream equipment have a roll width of 4.6 feet, which provides a net, edge-trimmed width of 3.6 to 3.9 feet.
The line is versatile, the company said, and can handle production switches between foamed sheet, solid sheet, cast film or laminated PET/PE, with minimum changeover times. Foamed, three- layer PET sheet makes a cost-effective product for the thermoforming of lightweight cups and trays.
The first PlexiPet line for foamed sheet was installed at a customer's plant in Europe and has been in full operation since August.
GNEUSS
Like SML, Gneuss has been working since
last year on extending its extruders' capabilities
to handle foamed sheet. Its new "foam module," which it piloted first in select customers' plants, is now commercially available and includes changes to the screw design of its MRS extruders, as well as an additional injection port and the integration of a melt-conditioning unit downstream.
Monika Gneuss, VP and marketing manager, said the module allows the MRS extruders to produce physically foamed sheet from PET with recycled content rates up to 100 percent.
Based on conventional single-screw extruders, the MRS extruders have a multiscrew section equipped with satellite screws in small extruder barrels for optimum devolatization. The extruders, also known as Multi Rotation Systems, ensure even distribution of the nucleating and foaming agents throughout the melt, and an online viscometer ensures correct viscosity. After extrusion and filtration, the melt is conditioned so that it foams appropriately.
"Thanks to the MRS foam module, foam sheet with a weight reduction of over 50 percent can be manufactured with a consistent foam structure and mechanical properties," the company said
in a press release. "And this from 100 percent post-consumer material, edge trim/skeletal waste, regrind or a combination of these." Products produced from the sheet can include containers, such as meat trays, egg cartons, cups and plates.
Because of the reduced density of the sheet, manufacturers can enjoy lower material costs, or even faster outputs.
MRS extruders are offered in a variety of sizes, with screw diameters ranging from 35mm to 200mm.
The module can be specified with new MRS extruders or added as a retrofit to existing machines.
BREYER
Breyer's sheet extruders now feature compact, water-cooled AC motors, said Joachim Bormann, sales and marketing manager. Previously, the firm's extruders had a water-cooled AC motor with a separate gear. The new motors include the gear, which means that only a single component needs to be connected to the extruder frame. The new motors can be retrofitted to existing Breyer extruders, Bormann said.
Breyer also has developed a mechanical shelving system to store calender rolls for embossing products. The system, which Bormann refers to as a "drawer," allows users to quickly change between rolls, depending on the pattern that's required for the sheet they are producing.
"With this drawer and an already-prepared next roll, the roll exchange is a matter of minutes instead of two or three hours," he said.
At the push of a button, the arm of the shelving system holding a roll ejects it within a few seconds, allowing the exchange of the roll for one with another embossing design.
The system is designed to be easy on the operator, as the roll is freely accessible and can be lifted out with a crane. When the calender is operating, the roll is hydraulically locked.
Allan Gerlat, correspondent
For more information
Breyer GmbH Maschinenfabrik,
Singen, Germany, 49-7731-920-0, www.breyer-extr.com
Gneuss Inc.,
Matthews, N.C., 704-841-7251, www.gneuss.com
SML Maschinengesellschaft mbH,
Gloucester, Mass., 978-281-0560, www.sml.at
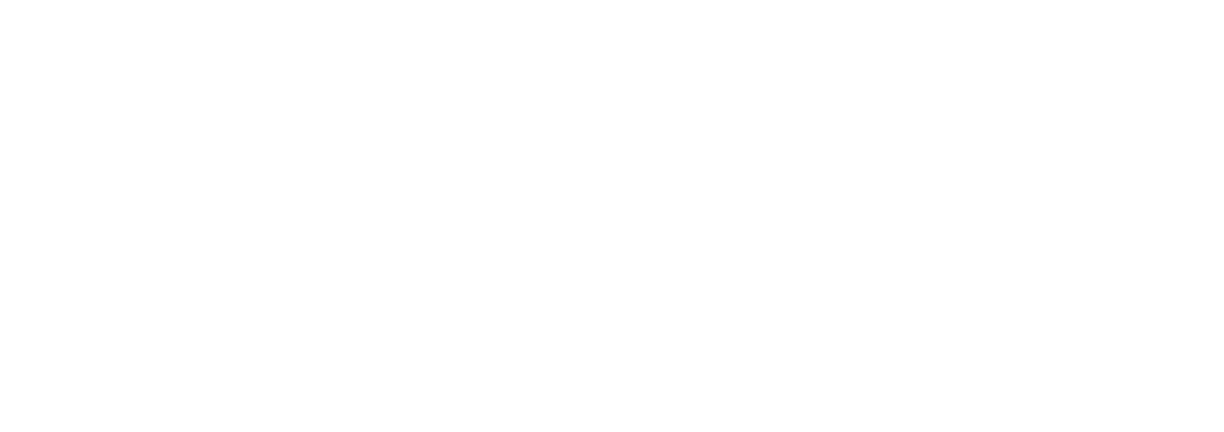